Williams evolves composites-intensive EV platform
British engineering firm uses a composite battery case as a structural member of its rolling chassis for a range of electric vehicles.
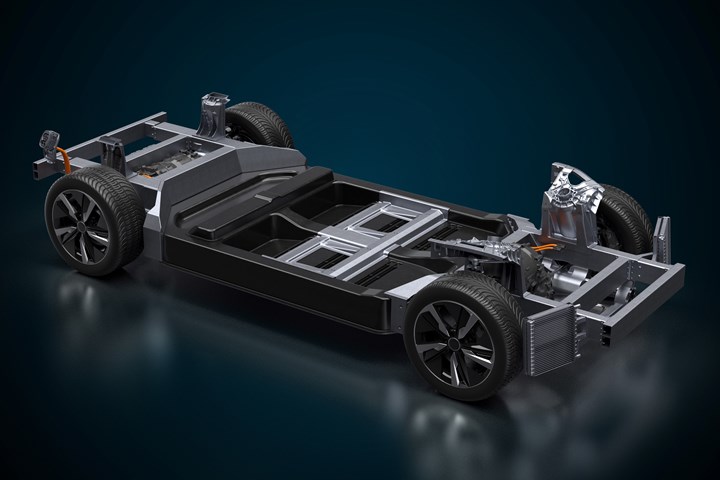
The EVX electric vehicle platform developed by Williams Advanced Engineering uses the composite battery case as a structural member. Photo Credit: Williams Advanced Engineering
Williams Advanced Engineering (WAE, Grove, Oxfordshire, U.K.) introduced its FW-EVX electric vehicle (EV) platform in 2017, designed to give vehicle manufacturers a modular system with which to develop new vehicles.
WAE reports that it is applying this innovative modular platform for use in a series of EVs — sedans, sports cars, convertibles and crossovers, alike — with the top hats engineered for the vehicles by Italdesign (Moncalieri, Italy), one of the leading transportation design and body engineering companies in the world.
As first reported by CW in 2018, this WAE approach is, like many EV platforms being developed, skateboard-like in that the rolling chassis is integrated into a flat structure. However, what is different about the Williams solution is that the battery is housed in a molded composite case that is part of the vehicle load structure: front and rear chassis elements are attached to it. Crash loads are transferred through internal reinforcements that are within the side sills.
To build this structure WAE is using both recycled composite material and aluminum; the company claims that the structure “sets new standards for static and torsional stiffness.”
WAE was the original supplier of batteries for the FIA Formula E World Championship series that launched in 2014, so it has substantial familiarity with battery engineering. The EVX battery has been developed by WAE; it is rated at 104-120 kilowatt-hours, though the company says that because a modular design approach is being taken, it could go to 160 kilowatt-hours, thereby providing a range of up to as much as 621 miles.
Because EVX is being targeted at the upper premium end of the electric vehicle market, it is anticipated that annual production volumes will be comparatively low — an upper end of 10,000 units.
Explains Paul McNamara, technical director at WAE, of the anticipated execution of the program with Italdesign, “Demand for high-performance electric vehicles is continuing to show considerable growth, but to date, there has not been a complete EV production solution. This unique relationship brings together state-of-the-art EV rolling chassis technology with one of the world’s leaders in vehicle body engineering.”
McNamara adds, “We will be able to support both new automotive entrants in bringing halo EVs to market — and established OEMs on lower-volume, high-performance models — with turnkey project delivery across the board, homologation included.”
Antonio Casu, CTO of Italdesign, says, “We aim to develop vehicle architectures in the GT, sedan, crossover and convertible markets, fully customizable inside and outside. We are targeting business cases that will cover different production volumes from an Ultra Limited Series up to 10,000 units a year, 500 of which can be built by Italdesign at our facilities in Turin.”
Related Content
-
Cryo-compressed hydrogen, the best solution for storage and refueling stations?
Cryomotive’s CRYOGAS solution claims the highest storage density, lowest refueling cost and widest operating range without H2 losses while using one-fifth the carbon fiber required in compressed gas tanks.
-
Plant tour: Joby Aviation, Marina, Calif., U.S.
As the advanced air mobility market begins to take shape, market leader Joby Aviation works to industrialize composites manufacturing for its first-generation, composites-intensive, all-electric air taxi.
-
Automotive chassis components lighten up with composites
Composite and hybrid components reduce mass, increase functionality on electric and conventional passenger vehicles.