Airtech launches recycled-grade Dahltram T-100GF resin
Thermoplastic polymer resin was designed to tackle distinctive industry challenges of large-scale 3D printing while also assisting with sustainability initiatives.
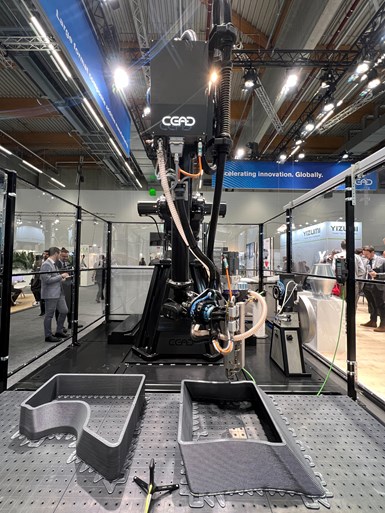
Live printing using the Dahltram T-100GF resin. Photo Credit: Airtech Advanced Materials Group
Dahltram T-100GF resin is Airtech Advanced Materials Group’s (Huntington Beach, Calif., U.S.) first recycled-grade thermoplastic polymer resin for pellet-fed, large-scale 3D printing. Developed with precision, the material was designed to tackle distinctive challenges of large-scale 3D printing while contributing to sustainability initiatives in the industry.
Dahltram T-100GF combines the power of recycled grade co-polyester resin with the strength of fiberglass reinforcement, resulting in a sustainable material that is suitable across diverse applications, including rapid prototyping, low-temperature molding, trimming tools, architectural structures, casting patterns and more. Airtech says it remains commited to expanding its product line with solutions that drive sustainability and contribute to a greener future through the use of large-scale additive manufacturing (AM) technologies.
Other benefits of Dahltram T-100GF resin beyond sustainability include the resin’s strength and durability. The inclusion of fiberglass reinforcement improves the material’s strength, promoting good durability and reliability across a spectrum of applications. The resin is also highly versatile, catering to a range of applications from rapid prototyping to architectural structures, offering an adaptable solution for manufacturers across various industries.
Dahltram T-100GF also provides an economically attractive alternative to traditional materials while still delivering performance. Airtech says this makes the resin an option for businesses aiming to streamline their production processes without compromising quality.
Related Content
-
Recycling end-of-life composite parts: New methods, markets
From infrastructure solutions to consumer products, Polish recycler Anmet and Netherlands-based researchers are developing new methods for repurposing wind turbine blades and other composite parts.
-
Plant tour: Daher Shap’in TechCenter and composites production plant, Saint-Aignan-de-Grandlieu, France
Co-located R&D and production advance OOA thermosets, thermoplastics, welding, recycling and digital technologies for faster processing and certification of lighter, more sustainable composites.
-
Bio-based acrylonitrile for carbon fiber manufacture
The quest for a sustainable source of acrylonitrile for carbon fiber manufacture has made the leap from the lab to the market.