CAMX 2021 exhibit preview: Carbon Axis
Carbon Axis showcases compact AFP solutions for the preforming of small parts with the XCell, XPlace mk2 and IdeaLab.
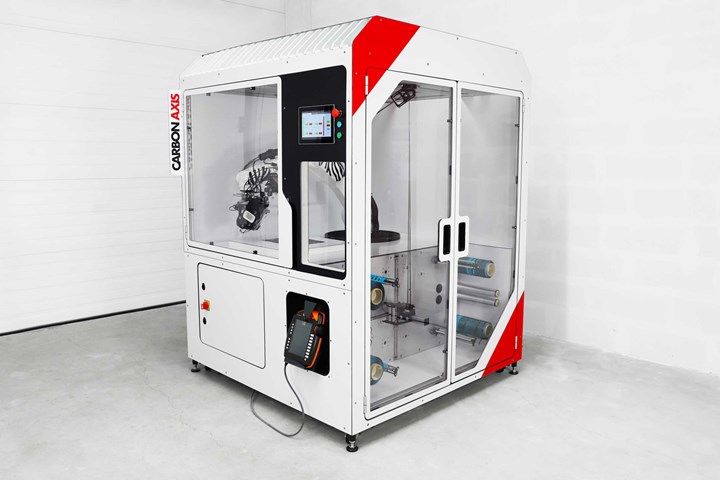
Carbon Axis (La Rochelle, France) showcases its XCell machine, a compact automated fiber placement (AFP) solution for the preforming of small parts (up to 1 x 0.5 x 0.5 m). The XCell machine, said to be a turnkey solution with a small footprint, can be easily integrated into any shop floor; total machine size is less than 2 x 2 m.
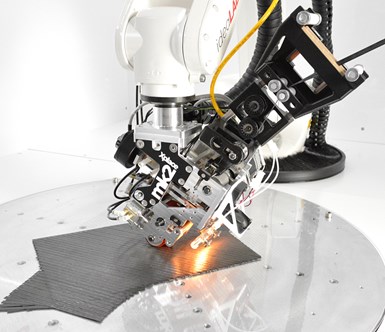
XPlace mk2.
The XCell has been designed for easy setup and safe operation. It comprises an insulated and temperature-regulated cell in which a small payload six-axis Kuka (Augsburg, Germany) robot carries Carbon Axis’ proprietary AFP head, the XPlace. The machine uses industry standard 3″ core bobbins of raw material, stored in a creel system that is tension controlled and that can be set up through the human machine interface. This flexible preforming cell can process both thermoset towpregs and dry stabilized tapes.
Carbon Axis’ patented AFP head design is said to incorporate the “angle cut” feature, which enables the manufacture of net shape preforms by eliminating the stepped contour traditionally found with AFP. Carbon Axis says this technology sees potential application in automated aircraft repair. Its latest developments for the XPlace mk2 also enables the deposition of fibers with a minimum fiber length of 50 mm for the development of preforms with more detailed contours.
The XCell currently has customers in the sports industry and R&D centers and is looking to expand to other markets such as motor sports, e-mobility or other new spaces.
Further, the company has recently commissioned an in-house dedicated R&D machine, the IdeaLab, that reportedly streamlines the transition towards automation to go from concept to product, prototype fabrication and small series production.
Related Content
-
STUNNING project completes lower half of MFFD
Clean Sky project has delivered the 8 × 4 meter welded aerostructure component, aided by advanced thermoplastic composite technologies and smart robotics.
-
The potential for thermoplastic composite nacelles
Collins Aerospace draws on global team, decades of experience to demonstrate large, curved AFP and welded structures for the next generation of aircraft.
-
Rocket Lab begins installation of large AFP machine for rocket production
The 99-ton AFP machine, custom-designed and built by Electroimpact, is claimed to be the largest of its kind, expecting to save around 150,000 manufacturing hours in the Neutron rocket’s production process.