CAMX 2021 exhibit preview: Gascogne Flexible
Gascogne Flexible showcases a tight release valve for ATL applications, a low coefficient of friction, solvent-free release liner and a high-porosity kraft paper for thin ply prepreg applications.
Share
Read Next
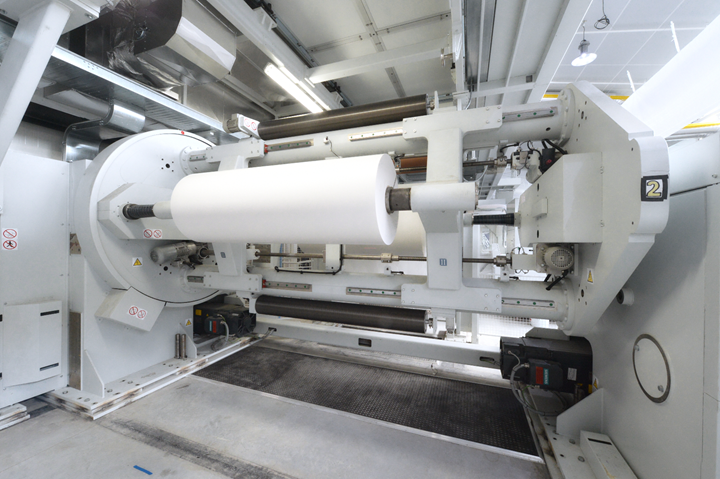
Photo Credit: Gascogne Flexible
Gascogne Flexible (Dax, France) has more than 30 years of experience developing and producing release liners designed for the prepreg industry. The company’s product range covers aeronautic, automotive, rotor blades, ballistic, sporting goods and specialty manufacturing applications.
At CAMX 2021, Gascogne showcases its latest innovations, including (1) a tight release valve for automated tape laying (ATL) applications which uses a supercalendered paper substrate for optimum surface smoothness and slitting accuracy, (2) a low coefficient of friction, solvent-free release liner with a heavy-weight clay-coated substrate for dimensional stability in humid environments and (3) a high-porosity kraft paper for thin ply prepreg applications that reportedly eases the evaporation of solvent during the manufacturing of thin ply prepregs.
The company claims its products are informed by expertise in thermal coating technologies (aqueous, solvent and solvent-less) and supported by coating equipment with precise tolerances, double-side coating capability and speeds up to 800 m/min. Gascogne employs strict quality management with a foreign object debris web inspection apparatus, automatic quality controls, an automatic feeder, contact-free polymerization and web cleaning systems.
Related Content
-
Graphene-enhanced SMC boosts molded component properties
CAMX 2023: Commercially sold GrapheneBlack SMC from NanoXplore increases part strength, stiffness and provides other benefits for transportation, renewable energy, energy storage and industrial markets.
-
Isobaric double belt press is well suited to continuous production
CAMX 2023: Flexible and robust double belt presses from Held Technologie are adaptable to various base composite material requirements to produce top-quality, long-lasting products.
-
CAMX 2023 Show Daily: Thursday, Nov. 2
CW is reporting live on the CAMX show floor in Atlanta, Georgia. Download today’s Show Daily covering interesting exhibitors and technologies, the committee members and volunteers that make the show possible, “Good Day, CAMX” results and a look back at show floor activities.