CAMX 2021 exhibit preview: Revolution Composites
Revolution Composites’ triaxial braiding process uses a wide range of fibers for for thrusters, nozzles and conical shapes in spaceflight.
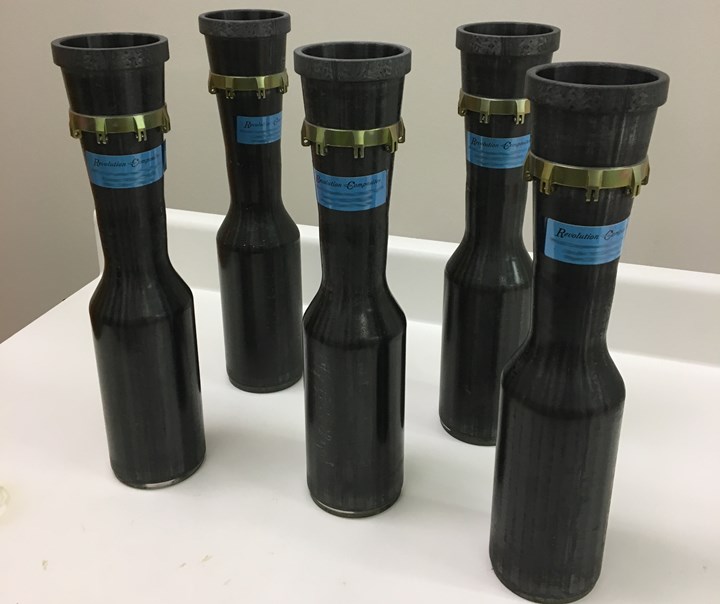
Rocket motors. Photo Credit: Revolution Composites
Revolution Composites (Norwood, Mass., U.S.) produces advanced composites for aerospace and defense customers in the spaceflight market. The company provides triaxial braiding of a wide range of fibers for subsequent molding via resin transfer molding (RTM), often with cyanate ester resins. The braiding process is used for thrusters, nozzles and conical shapes in spaceflight, particularly in high-temperature structures made by carbon or ceramic matrix composites (CMC) processes.
According to Revolution Composites, braiding allows for the custom combination of continuous fibers in an oriented pattern over a tool of nearly any shape or size, eliminating the need for cuts, splices or darts inherent with other composite fabrication methods.
The triaxial braiding process creates a single ply of tubular fabric by interlacing both helical (±) and axial (0º) yarns. Triaxial braid can be constructed as a quasi-isotropic laminate, with similar material properties in all directions, or designed to add strength and stiffness to reduce weight. Revolution Composites says the process is similar to plastic extrusion and can be controlled by the rate at which the braid is pulled relative to the speed of formation. This allows for NC programmable control to be used to specify the extrusion rate, which in turn determines and maintains the desired tow orientation throughout the part.
Another advantage of triaxial braiding is the ability to easily create continuous, conical and tapered geometries. Braiding is conducive to creating preforms of cone-like shapes for subsequent manufacturing of high temperature thrusters, nozzles, rocket motors and other complex geometries. Because the braid angle can be controlled throughout the tapered regions, engineers can ensure that all thermal and structural requirements are satisfied.
Related Content
-
“Structured air” TPS safeguards composite structures
Powered by an 85% air/15% pure polyimide aerogel, Blueshift’s novel material system protects structures during transient thermal events from -200°C to beyond 2400°C for rockets, battery boxes and more.
-
Industrializing additive manufacturing in the defense/aerospace sector
GA-ASI demonstrates a path forward for the use of additive technologies for composite tooling, flight-qualified parts.
-
Pull-wound carbon fiber poles enable lightweight, compact, rigid emergency stretcher
Based on military feedback, Epsilon Composite developed an optimized, foldable stretcher that combines telescopic pull-wound carbon fiber tubes.