MakerBot 3D printing platform offers expanded advanced composite materials portfolio
Available through MakerBot Labs, the newly qualified 3D printing materials are ideal for demanding engineering applications that require high strength and heat resistance.
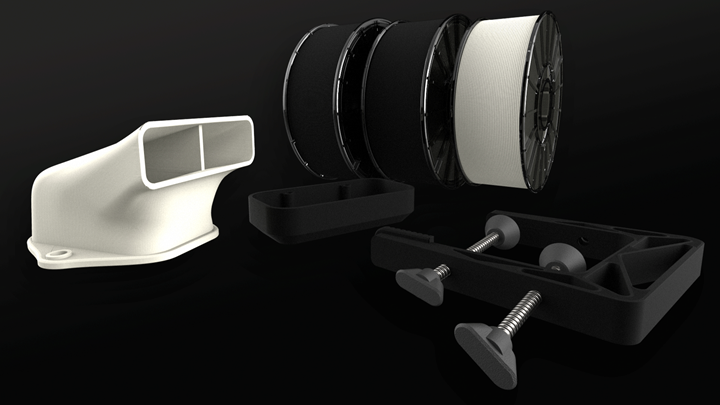
Photo Credit: MakerBot Industries
3D printer manufacturer MakerBot Industries (New York City, N.Y., U.S.) has expanded its advanced engineering materials offerings for the MakerBot Method 3D printing platform with the addition of three new Luvocom 3F materials from Lehvoss Group (Hamburg, Germany), a provider of high-performance thermoplastics for industrial sectors. This brings the number of Method materials up to 30, MakerBot says, giving customers an even wider selection of manufacturing-grade materials with which to explore.
Luvocom 3F PAHT 9825 NT, Luvocom 3F PAHT CF 9891 BK and Luvocom 3F PET CF 9780 BK are available to use with the MakerBot LABS GEN 2 Experimental Extruder for both the Method and Method X 3D printers. The Labs extruder transforms Method into an open platform that is able to print qualified advanced engineering materials from leading filament suppliers.
Designed for 3D printing and industrial applications, the Luvocom 3F materials have similar properties to their compounded versions used for injection molding. These materials are optimized to provide an easy-to-print experience and to achieve next-level properties and quality. Parts printed with these materials are said to result in strong, stiff prints with a high-quality surface finish, and are ideal for prototyping, jigs and fixtures and end-use applications.
The qualified Luvocom 3F materials include:
Luvocom 3F PAHT 9825 NT: A high-temperature polyamide (Nylon) material with continuous service temperature of up to 100°C and the strength of PA/Nylon 6. The material has 50% reduced water uptake and a four-times slower absorption rate compared to PA6, MakerBot says. Low moisture absorption can help minimize printing issues as well as property changes of the printed part. This material is optimized for low warpage, high strength and impact resistance and excellent surface finish for end-use parts, such as flanges and fixtures.
Luvocom 3F PAHT CF 9891 BK: This carbon fiber-filled grade reports lower water uptake and good resistance against harsh chemicals like automotive fluids. The addition of carbon fiber strengthens the thermal and mechanical properties, and has a continued use of up to 150°C while retaining 50% of its mechanical properties. The material is suitable for high-temperature environments such as automotive under-the-hood applications, such as housings or engine covers. In addition to its high mechanical performance, the material is easy to print and does not warp.
Luvocom 3F PET CF 9780 BK: A carbon fiber-filled polyethylene terephthalate (PET) material that is easy to print, with low warping and exhibits an optimized surface finish straight from the printer, MakerBot says, reducing the need for post-processing. It provides high strength, elevated temperature resistance up to 120°C and chemical resistance, reportedly outperforming PETG.
Related Content
-
Plant tour: Spirit AeroSystems, Belfast, Northern Ireland, U.K.
Purpose-built facility employs resin transfer infusion (RTI) and assembly technology to manufacture today’s composite A220 wings, and prepares for future new programs and production ramp-ups.
-
Combining multifunctional thermoplastic composites, additive manufacturing for next-gen airframe structures
The DOMMINIO project combines AFP with 3D printed gyroid cores, embedded SHM sensors and smart materials for induction-driven disassembly of parts at end of life.
-
Manufacturing the MFFD thermoplastic composite fuselage
Demonstrator’s upper, lower shells and assembly prove materials and new processes for lighter, cheaper and more sustainable high-rate future aircraft.