Raise3D launches fused filament fabrication 3D printer aimed at small-batch production
The large-format RFM500 fabricates carbon fiber-reinforced end-use parts with industrial-grade precision and repeatability.
Share
Read Next
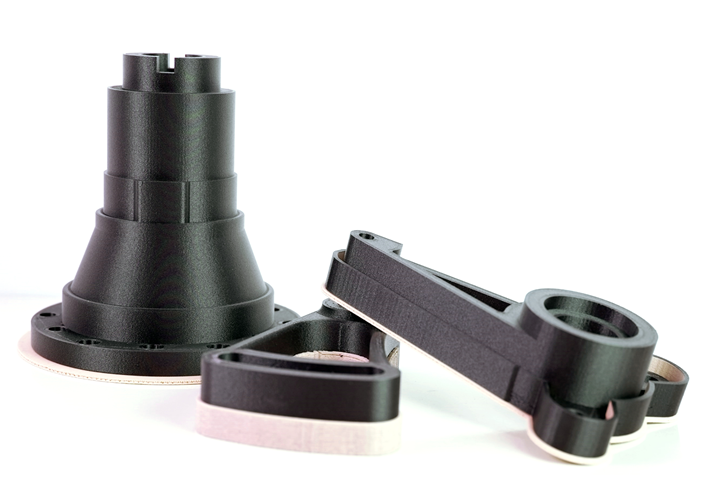
Carbon fiber-reinforced parts developed via the RFM500 printer. Photo Credit: Raise3D
Raise3D (Rotterdam, Netherlands and Irvine, Calif., U.S.), a global provider of additive manufacturing (AM) solutions for small- and large-scale enterprises, launches the Raise3D RMF500, a large-format fused filament fabrication (FFF) 3D printer aimed at small-batch production in the industrial sector. The printer can fabricate carbon fiber-reinforced end-use parts with highly accurate production repeatability, high speed and large build volumes.
The RMF500 has a 500 x 500 x 500 mm build area. It can reach print speeds of up 300 mm/s along with an acceleration of up to 2G and movement of up to 1,000 mm/s. An independent dual extruder system (IDEX) also makes it possible to execute two print jobs simultaneously.
Linear motors help the RMF500 achieve an accuracy of 0.001 mm along the X and Y axes and 0.0009765 mm along the Z-axis. Its 1 μm closed-loop, synchronous control reduces speed variations with load changes of the motor, further enhancing precision.
Use of a carbon fiber-reinforced filament is said to ensure reliable printing of strong end-use parts and a good alternative to metal parts. The material offers high rigidity, a low shrinkage ratio and does not require a heated chamber to avoid warping, as is customary in 3D printing. According to Raise3D, this leads to a far more efficient printer that does not need to draw so much power; for example, 120 watts is used to power a single hotend.
Moreover, for trouble-free, uninterrupted printing, the RMF500 is equipped with four 2.5-kg cartridges (main and auxiliary) so the 3D printer can switch automatically between main/auxiliary cartridges, reducing the need for constant intervention. Positive pressure humidity control keeps chamber humidity under 5% relative humidity.
RMF500 offers additional benefits. The 3D printer’s load-bearing structural parts are made of high-grade hardened steel, with a Z-axis that can withstand a maximum load close to 100 kg and has a deflection error that is reported to be 50% lower than that of conventional offerings. The linear motor driven system also has low clearance and low maintenance requirements.
Related Content
-
Plant tour: Joby Aviation, Marina, Calif., U.S.
As the advanced air mobility market begins to take shape, market leader Joby Aviation works to industrialize composites manufacturing for its first-generation, composites-intensive, all-electric air taxi.
-
McLaren celebrates 10 years of the McLaren P1 hybrid hypercar
Lightweight carbon fiber construction, Formula 1-inspired aerodynamics and high-performance hybrid powertrain technologies hallmark this hybrid vehicle, serve as a springboard for new race cars.
-
PEEK vs. PEKK vs. PAEK and continuous compression molding
Suppliers of thermoplastics and carbon fiber chime in regarding PEEK vs. PEKK, and now PAEK, as well as in-situ consolidation — the supply chain for thermoplastic tape composites continues to evolve.