Stratasys adds two novel composite-ready 3D printers to F123 Series
Novel composite printers and Nylon-reinforced carbon fiber material expand applications for additive manufacturing with dimensional repeatability of up to 99%.
Share
Read Next
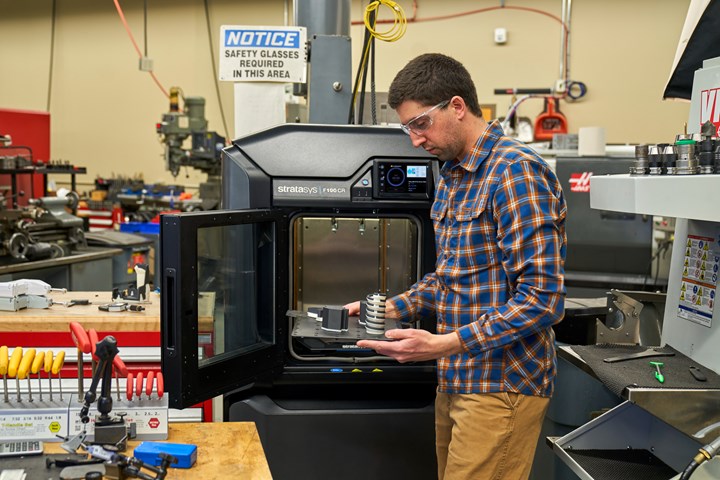
Photo Credit: Business Wire
Polymer 3D printing solutions provider Stratasys Ltd. (Eden Prairie, Minn., U.S. and Rehovot, Israel) has expanded its F123 Series of 3D printers with the introduction of the F190CR and F370CR 3D printers, plus new FDM Nylon-CF10 material reinforced with carbon fiber. The new printers offer high stiffness and strength materials in a hardened machine ready for composite material printing, the company reports.
The novel composite 3D printers are designed for manufacturers and industrial machinists to supplement traditional fabrication technologies with high-strength composite 3D printing. The printers are said to help manufacturers produce end-use parts faster and more cost effectively, and are ideal for jigs, fixtures and workholding tools.
Stratasys says they include integrated GrabCAD Print software that provides a simple and intuitive CAD-to-print workflow and includes advanced features to ensure successful prints. Stratasys also provides enterprise application connectivity through the MTConnect standard and its GrabCAD Software Development Kit. The composite-ready F123 Series printers include reusable build trays, a built-in camera for remote monitoring and a 7-inch control touchscreen. The F370CR printer also offers auto-changeover of materials to eliminate interruptions during a build to replace materials — a new canister is simply put in place and the build continues.
Verified and published data has also proven the new printers have dimensional repeatability of up to 99% regardless of part size or geometric complexity, according to Dick Anderson, senior vice president, manufacturing for Stratasys.
Moreover, compared to comparable competitive printers, Stratasys contends that its composite-ready F123 Series of printers offer more material availability, a larger build volume, soluble support options and a lower cost-per-build volume due to the large oven size. Further, the larger, fully heated build chamber of the F190CR and F370CR printers, coupled with the ability to use stabilizer walls, reportedly enables manufacturers to build taller parts than could be printed in competitors machines.
Stratasys has also introduced FDM Nylon-CF10, a composite material for the F123 Series printers that is more than 60% stronger and nearly three times as stiff as its base nylon material. The chopped carbon fiber material is just one of many thermoplastic materials available for the F123 Series printers. When used with Stratasys soluble support, manufacturers have the ability to print any geometry without restriction. The F190CR and F370CR printers also support several other engineered thermoplastics.
The new composite-ready F123 Series printers and FDM Nylon-CF10 are available for order now and are expected to ship in June.
Related Content
-
PEEK vs. PEKK vs. PAEK and continuous compression molding
Suppliers of thermoplastics and carbon fiber chime in regarding PEEK vs. PEKK, and now PAEK, as well as in-situ consolidation — the supply chain for thermoplastic tape composites continues to evolve.
-
Plant tour: Joby Aviation, Marina, Calif., U.S.
As the advanced air mobility market begins to take shape, market leader Joby Aviation works to industrialize composites manufacturing for its first-generation, composites-intensive, all-electric air taxi.
-
A new era for ceramic matrix composites
CMC is expanding, with new fiber production in Europe, faster processes and higher temperature materials enabling applications for industry, hypersonics and New Space.