Toray Composite Materials America launches flexible, adaptive 2700 prepreg system
Particularly geared toward emerging aerospace programs, the epoxy-based meets demands for high performance and process flexibility from prototype to high-volume production.
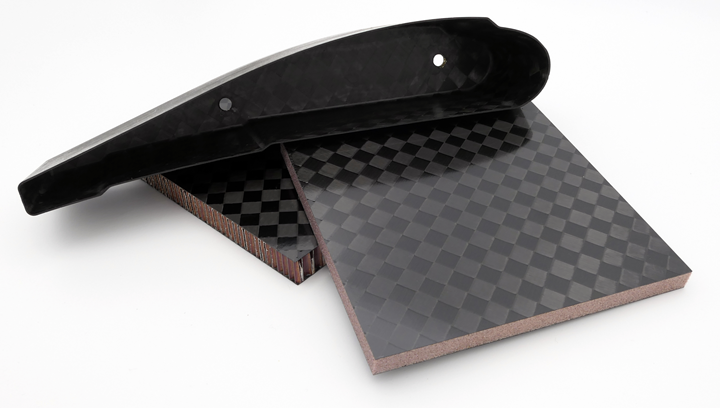
Photo Credit: Toray Composite Materials America Inc.
On July 20, Toray Composite Materials America Inc. (TCMA, Tacoma, Wash., U.S.) a producer and supplier of carbon fiber materials and advanced composite prepreg, announced the launch of the Toray 2700 prepreg system. Epoxy-based 2700 is a high-performance, patented resin technology geared toward emerging aerospace programs. TCMA says it satisfies stringent aerospace structural design drivers and enables the manufacture of high-quality, high-volume, cost-effective composite parts.
According to Timothy Kirk, vice president of aerospace sales, the 2700 system not only performs well in low-volume environments, but it is also highly adaptable for automation and other high-rate production processes. Specifically engineered for heat resistance and low moisture absorption, it is said to be suitable for applications where parts are exposed to high-heat and high-humidity environments (i.e., hot/wet conditions). It accommodates flexible cure temperatures (250-350ºF/121-177ºC) and satisfies aerospace structural drivers such as compression properties.
Final product configurations of 2700 include combining it with various Torayca unidirectional carbon fibers and other woven carbon or glass fibers. This prepreg is drapable and press cures in less than five minutes, TCMA says, enabling the rapid production of parts with complex geometries. It also provides low void content and excellent all-around structural properties.
Toray 2700 can also be used in compression molding of high-volume small parts such as aircraft clips, molded brackets and wing ribs, while larger parts may be processed via out-of-autoclave (OOA) and vacuum bag only (VBO). Other suitable processing methods include automated tape laying (ATL), automated fiber placement (AFP) and hand layup.
Related Content
-
Plant tour: BeSpline/Addcomp, Sherbrooke, QC, Canada
Composites automation specialist increases access to next-gen technologies, including novel AFP systems and unique 3D parts using adaptive molds.
-
Nine factors to consider when designing composites cure tooling
Gary Bond discusses the common pitfalls and compromises when designing good cure tooling and their holistic significance for a robust composite production process.
-
STUNNING project completes lower half of MFFD
Clean Sky project has delivered the 8 × 4 meter welded aerostructure component, aided by advanced thermoplastic composite technologies and smart robotics.