Composites and the call to space
CW editor-in-chief Scott Francis discusses the role of composites in recent and upcoming space missions.
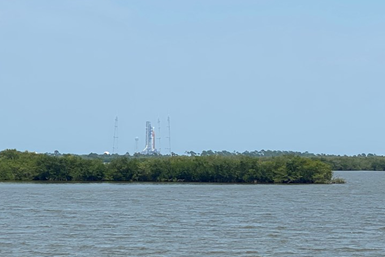
NASA’s Artemis 1 Space Launch System during engine testing at Kennedy Space Center in Cape Canaveral, Fla., U.S. in June 2022. Photo Credit: CW
When I was 14, I thought I wanted to be an astronaut and convinced my parents to let me go to Space Camp in Huntsville, Ala., U.S., an educational experience that touches on topics such as space exploration, aviation and robotics. When I arrived at camp, there were a variety of simulators, IMAX theaters and experiences designed to impart the feeling of spaceflight. However, none of it went quite according to plan. It turns out that having an innate fear of heights and a propensity for motion sickness means you actually do not want to be an astronaut. Later in life, I’ve occasionally wondered where my career path might have taken me if I had invested less energy in the astronaut fantasy and paid more attention during the Space Camp tours of NASA’s Marshall Space Flight Center production facilities. It didn’t dawn on me at the time that there were very important ways to be involved in the space program without being launched into outer space.
When I initially joined CompositesWorld about five years ago, I was thrilled to learn more about the ways composite materials enable a wide range of space applications. I started volunteering for as many stories on these topics as I could and it became my unofficial beat. I recall attending the Space Foundation Space Symposium in 2019 and listening to a keynote address from NASA administrator James Bridenstine as he ticked off a list of mission goals and dates: The Artemis program was gaining momentum, having been formally established in 2017, and the U.S. Space Force, a new branch of the armed services spun out of the U.S. Air Force’s Space Command division, had just been formed. The U.S. space program felt reinvigorated and the atmosphere of collaboration between commercial companies, NASA and the military was palpable. Our country was on the brink of a new golden age of space exploration.
Composites have played a role in each of these space initiatives in myriad ways.
Several years later, and much has been accomplished. In May 2020, U.S. astronauts were launched into orbit for the first time since the end of the Space Shuttle Program in 2011 — and it was accomplished on a Falcon 9 rocket and Crew Dragon capsule built by SpaceX, beginning a new chapter of space exploration where private companies are partnering with NASA in new and exciting ways. Commercial space launches increased in frequency and new milestones in space exploration seemed to come every few months. The Mars rover, Perseverance, landed safely on the red planet in February 2021. The James Webb Space Telescope — which has been the culmination of decades of development and testing — was launched in December 2021 and is now safely in L2 orbit, sending home images that are enabling us to see farther into the universe than ever before with unprecedented clarity. The Artemis program is also well underway — the uncrewed Artemis I made a trip around the moon in November 2022 and a crewed Artemis II is scheduled for lunar flyby in November 2024.
Composites have played a role in each of these initiatives in myriad ways from carbon fiber skins on payload fairing sandwich structures and heat shield components to telescope structures capable of maintaining stability in the extreme temperatures of space.
In the November 2023 issue of CW, I’m excited to revisit reporting on space applications with a story about the Type V composite tanks that will be featured on an upcoming lunar lander mission currently scheduled for mid-November 2023. The lander was designed and constructed by Intuitive Machines as part of NASA’s Commercial Lunar Payload Services (CLPS) initiative and the mission will explore an area of the moon’s south pole region as a potential landing site for the Artemis III mission that promises to return humans to the moon. Read the full story on p. 36.
In addition, check out Ginger Gardiner’s story about a composite molding compound that replaces Invar for optics housings in small satellites on p. 22. While Invar’s low coefficient of thermal expansion has traditionally made it a material of choice for such applications, the material is heavy. This new weight-saving approach may alter the paradigms behind use of composites in commercial space.
One of the reasons I love working for CW is learning about technologies that are involved in defining our time in history. It’s fascinating to see the sheer amount of R&D and engineering that go into space applications, and a reminder that so many talented people in the composites industry contribute to making each of these missions a success. I hope these same fascinations are imparted to you as you read about these new developments.
Related Content
Revisiting the OceanGate Titan disaster
A year has passed since the tragic loss of the Titan submersible that claimed the lives of five people. What lessons have been learned from the disaster?
Read MoreHow composites have become a necessity
Composites used to be one of many material options across industries and applications, but that's not the case anymore.
Read MoreLooking at composites through the lens of U.S. history
When you’re a tourist with a background in writing for manufacturing it’s impossible not to notice all of the ways in which composites have resulted in significant milestones in the U.S. — historically and in the present.
Read MoreRemembering Don Adams
When one thinks of composites test methods, one thinks of Don Adams. Don passed away at the end of 2022. We remember him here.
Read MoreRead Next
ESA StarTiger project showcases innovation, collaboration in space industry
ESA initiative brought together a multidisciplinary team to harness advances in space technology and manufacturing such as metal and composites AM, robotics and advanced perception capabilities.
Read MoreThoughts from the trade show floor
As the trade show season kicks off, CW editor-in-chief Scott Francis shares observations from industry events.
Read More“Structured air” TPS safeguards composite structures
Powered by an 85% air/15% pure polyimide aerogel, Blueshift’s novel material system protects structures during transient thermal events from -200°C to beyond 2400°C for rockets, battery boxes and more.
Read More