Cutting time for composites design allowables
New approach by Dr. Stephen Tsai and Daniel Melo promises to reduce the required number of tests from 1,000 to mere dozens, providing results in days vs. months and at much lower cost.
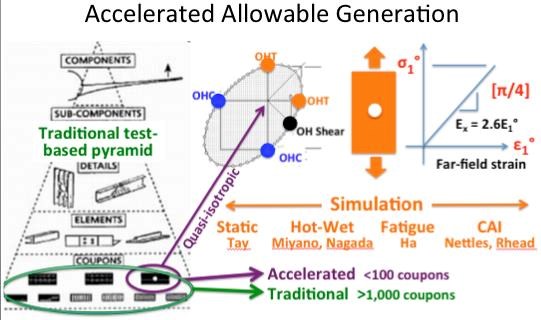
New vs. traditional approach to design allowables.
SOURCE: Dr. Stephen W. Tsai and Jose Daniel D. Melo.
HPC reported on this new approach in the July issue: “Overnight design allowables? An invariant-based method for accelerating aerospace certification testing.” For more details and the full series of charts and graphs, see the white paper from Dr. Tsai and Daniel Melo posted on CW’s White Papers page.
Dr. Tsai comments, “The recognition of invariants that can significantly simplify design and testing of composites structures was discovered by Daniel and me by accident. The number of tests for design allowable generation can be reduced from one thousand to a few dozen if not fewer. More importantly, key tests can be made a matter of hours instead of days, weeks or months.” He adds that the only stiffness data needed is the value of trace, a sum of the diagonal components of the stiffness matrix. “For strength, one tensile or compressive strength of open hole coupons at room temperature can be sufficient to generate allowables, and the accelerated testing of fatigue strength can also be done based on the shift factor of viscoelastic behavior of composites.”
To put it more in layman’s terms and get a critical review, I asked Dr. Rik Heslehurst to read and comment on the white paper. Heslehurst is a former aeronautical engineering officer in the Royal Australian Air Force (RAAF), in charge of material and process engineering for almost two decades. He also instructs advanced composite engineering courses for Abaris Training (Reno, Nevada) and has consulted for a wide variety of companies including Boeing, the U.S. Air Force, Lockheed Martin and Bombardier. Heslehurst’s response:
"The basic premise is that all composite materials (plies and laminates) have a stiffness relationship that is essentially invariant (statistically low variation). This invariant term is called TRACE. With knowledge of the axial longitudinal modulus value for any composite material the TRACE factor can be determined and the resulting stiffness matrix of a ply and thus a laminate can be determined. This approach is a significant and positive step in reducing the cost of determining materials allowables.
I would caution, however, that the assumptions made, such as the major Poisson’s ratio as 0.3 and the derivation of the shear modulus term, require a sufficient knowledge of composite materials properties computation as well as design allowables generation — for example, the differences between that for unidirectional tape and cloth.
I believe that the development of the shift factors for open hole, environmental and fatigue is also a very positive step, and fortunately, there is now extensive materials data available on these effects to allow close comparison with simulated data.
I am encouraged by the approach and already see several applications in my own work that will allow early and rapid development of composite designs, but I would reiterate that a novice not use this approach without due understanding and caution."
The foundation of invariants and implications on composites design allowables testing will be covered extensively by several speakers in the upcoming Composites Durability Workshop 19 (July 27-29) hosted by Stanford University’s Department of Aeronautics & Astronautics (Stanford, Calif., USA).
Proposed advances that can simplify design allowables generation will be presented by representatives of Stanford, Wichita and other universities, as well as end users and the FAA. Potential issues in expanding the adoption of this approach will also be discussed and help in using tools and templates for one master ply will be available during and after workshop.
A formal technical paper, “An invariant-based theory of composites,” has just been published online in the journal Composites Science and Technology.
Related Content
Plant tour: Daher Shap’in TechCenter and composites production plant, Saint-Aignan-de-Grandlieu, France
Co-located R&D and production advance OOA thermosets, thermoplastics, welding, recycling and digital technologies for faster processing and certification of lighter, more sustainable composites.
Read MoreNovel composite technology replaces welded joints in tubular structures
The Tree Composites TC-joint replaces traditional welding in jacket foundations for offshore wind turbine generator applications, advancing the world’s quest for fast, sustainable energy deployment.
Read MoreNatural fiber composites: Growing to fit sustainability needs
Led by global and industry-wide sustainability goals, commercial interest in flax and hemp fiber-reinforced composites grows into higher-performance, higher-volume applications.
Read MoreBio-based acrylonitrile for carbon fiber manufacture
The quest for a sustainable source of acrylonitrile for carbon fiber manufacture has made the leap from the lab to the market.
Read MoreRead Next
All-recycled, needle-punched nonwoven CFRP slashes carbon footprint of Formula 2 seat
Dallara and Tenowo collaborate to produce a race-ready Formula 2 seat using recycled carbon fiber, reducing CO2 emissions by 97.5% compared to virgin materials.
Read MoreVIDEO: High-volume processing for fiberglass components
Cannon Ergos, a company specializing in high-ton presses and equipment for composites fabrication and plastics processing, displayed automotive and industrial components at CAMX 2024.
Read MoreDeveloping bonded composite repair for ships, offshore units
Bureau Veritas and industry partners issue guidelines and pave the way for certification via StrengthBond Offshore project.
Read More