Not your average carbon fiber part
A Swedish industrial designer and artisan, Ragnar Friberg, contacted CW recently about a new project: a one-of-a-kind custom champagne glass and an accompanying storage cabinet that incorporates carbon fiber — along with a number of high-end materials.

This exclusive champagne glass and protective cabinet, incorporating carbon fiber/epoxy, comes from Swedish designer Ragnar Friberg.
A Swedish industrial designer and artisan, Ragnar Friberg, contacted CW recently about a new project: a one-of-a-kind custom champagne glass and an accompanying storage cabinet that incorporates carbon fiber — along with a number of high-end materials including diamonds, gold, porphyry stone and black oak wood from the 15th Century. The founder of the design firm RAF (Stockholm), Friberg tells us that his years of experience with composites in power boat racing, where he constructed his own boats, led him to eventually build a business where he combines carbon fiber with other fine materials to make beautiful, exclusive yet useful articles.
Friberg envisioned a 305 mm-tall champagne flute with a carbon fiber/epoxy cup combined with a gold stem ornamented with inlays, on an 18K solid gold base. The entire glass weighs 190 grams, with the base weighing 100 grams, “to balance the cup when it’s been filled with champagne,” says Friberg. He explains that the cup was made with 6 plies of a 1k 2x2 woven twill, 150 grams per square meter (gsm) and 1 mm thick, with the fabric supplied by textile weaver C. Cramer & Co. (Heek, Germany). The fabric was wet out with an epoxy supplied by Huntsman Advanced Materials (The Woodlands, TX, US). Friberg explains that he rejected prepreg because “It looked too perfect, too sterile. I wanted to add a blue color to the epoxy resin, so that the cured cup and stem inlays would be faintly blue.” The biggest challenge was applying the gold leaf. After wetting the first ply with resin, he placed the gold leaf onto the wet-out fabric on a vacuum table, he explains: “I had to get the gold leaf to really sink into the fiber weave, and the vacuum helped in that regard.” Placing the gold-treated ply in the mold was also tricky, to avoid air entrapment and cracking of the very thin gold layer. After nearly 100 attempts to get the gold layer as he wanted it, Friberg says he switched to an epoxy with higher flexibility, which prevented cracking in the gold. To ensure the integrity of the gold/carbon bond, the cup was molded in two halves, with the inner 3 plies (including the gold) molded around an conical aluminum mandrel, and the outer three plies placed in a matching female mold. The entire layup was oven-cured at 60°C for 16 hours.

The cup is supported by four gold legs, which dovetail into the stem, which has carbon fiber inlays.
After demolding, the cup halves were bonded together (with seams offset by 90°), and the cup was sanded, clear-coated and polished. The photos show how the bottom of the cup is finished with an adhesively-bonded cast gold cone. Four thin, solid gold legs were glued to the cup’s exterior; the legs extend down past the cone to the square stem, where they are attached via dovetailed slots. The stem combines more carbon/epoxy, 15th Century black oak and lizard skin inlays over solid 18K gold; the stem in turn is fastened to the gold base with 4 gold screws. Three diamonds totalling 2.09 carats are part of the flute, including one that is set inside the cup at the bottom. Says Friberg, ”The diamond inside stimulates the champagne bubbles and boosts the bouquet.”
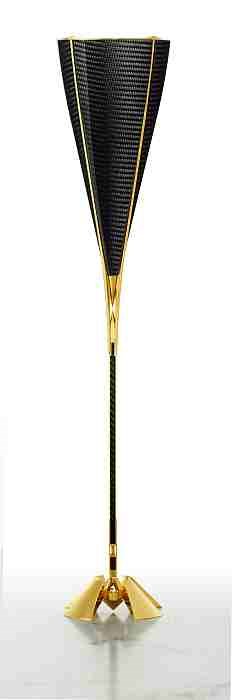
The cup is made with a 1K carbon twill, with gold leaf applied to the cup's inner surface before cure.
The hefty 8 kg, 450 mm-high cabinet exists to hold and protect the glass. It is a combination of gold, porphyry stone, lizard skin and silk. All together, Friberg estimates that more than 1000 hours have gone into making the glass and cabinet, which, when offered to the market, will command approximately $120,000. When asked what motivates his work, Friberg says that he got interested in composites in the 1990s and has been working on projects that would showcase carbon fiber ever since: “I came up with the idea to make something really nice — to make a truly beautiful thing is worth trying.” Friberg's web site (rafstockholm.com/index.html) has more photos and other products as well.
Related Content
Highly tunable, woven lattice reinforcements target automotive structures
CAMX 2023: Startup Weav3D will be demonstrating its two collaborative automotive demonstrator parts and present two conference papers.
Read More3D-woven composites find success in aerospace, space
CAMX 2024: Bally Ribbon Mills experts are displaying the company’s various joints, thermal protection system (TPS) technologies and other 3D woven composites for mission-critical applications.
Read MoreBraskem demonstrates PP solutions using Weav3D composite lattice technology
Partnership combines Braskem’s polypropylene sheets with Weav3D Rebar for Plastics technology to address new structural, automotive applications requiring high-strength, lightweight material solutions.
Read MorePlant tour: Albany Engineered Composites, Rochester, N.H., U.S.
Efficient, high-quality, well-controlled composites manufacturing at volume is the mantra for this 3D weaving specialist.
Read MoreRead Next
VIDEO: High-volume processing for fiberglass components
Cannon Ergos, a company specializing in high-ton presses and equipment for composites fabrication and plastics processing, displayed automotive and industrial components at CAMX 2024.
Read MorePlant tour: Daher Shap’in TechCenter and composites production plant, Saint-Aignan-de-Grandlieu, France
Co-located R&D and production advance OOA thermosets, thermoplastics, welding, recycling and digital technologies for faster processing and certification of lighter, more sustainable composites.
Read MoreDeveloping bonded composite repair for ships, offshore units
Bureau Veritas and industry partners issue guidelines and pave the way for certification via StrengthBond Offshore project.
Read More