Plant Tour: Holland Composites, Lelystad, Netherlands
Balancing performance with affordable production, this industry veteran continues to explore composites’ infinite possibilities.
Foiling catamarans, building facades and more. Located less than an hour’s drive from Amsterdam, Holland Composites pursues a wide variety of highly technical projects in its 4,500-m2 facility. Source, all images | Holland Composites
Located in a 4,500-square-meter building, less than an hour’s drive from Amsterdam, Holland Composites (Lelystad, Netherlands) focuses on four markets: marine/offshore, architecture, renewable energy and special projects. Holland Composites uses a mix of prepreg carbon fiber-reinforced polymer (CFRP) and Nomex honeycomb for highly loaded parts, and resin infusion and glass fiber for the building industry and lower-margin projects. “We are still able to pull off high -performance even with these more cost-effective constructions, and we maintain low overhead for the parts using advanced materials,” says Sven Erik Janssen, Holland Composites’ co-managing partner, along with founder Pieterjan Dwarshuis. “This is unique.”
The company also operates the brand DNA Performance Sailing, producing foiling multihull sailboats, including the 5.5-meter F1X catamaran, the 11-meter TF10 trimaran and 14-meter F4 catamaran. The 12-meter G4 catamaran is no longer in production, “but it showcases our capabilities for advanced composite yacht building and high performance,” notes Janssen. “This boat is a dual-purpose foiling racer and family cruiser with berths, kitchen and head, yet achieves a speed of more than 35 knots. The ability to foil with more than 4,000 kilograms in weight and only a six-person crew — there is still no competition in this field short of multi-million-dollar America’s Cups yachts.”
Marine to road and air transport
Before the tour begins, Janssen gives a history of the company and the composite structures it produces. Holland Composites was formed in 1992 by Janssen and Dwarshuis, who were, at the time, students at the Technical University in Delft (TU Delft, Netherlands). They built carbon fiber masts for Hobie sailing catamarans, an 18-meter yacht tender using CFRP and Nomex honeycomb in 1993, and a 100-foot sailing yacht using resin infusion processing in 1994. “By that time, everything we were building was made from carbon fiber using prepreg or infusion,” recalls Janssen. However, he adds, because the business was subject to the typical ups and downs of the marine market and one-off projects, “We looked to diversify, but wanted to stay in advanced composites versus FRP [meaning less advanced, more commodity glass fiber and polyester resin].”
The company began exploring lightweight solutions for road transport, producing 35 truck trailers featuring a glass/carbon fiber composite monocoque chassis, which cut weight by 3,500 kilograms. “The trucks were carrying dense loads, like potatoes, and would max out in weight before filling their volume,” Janssen explains. Holland Composites also made refrigerated trailers, he adds, “But we were a bit too early; the market was not yet ready — companies were not yet able to calculate the yearly gains from transporting more cargo and maintenance savings of the composite trailers versus their higher initial cost.”
At about the same time, VRR (Rotterdam, Netherlands), a supplier of custom air cargo solutions, approached the company. “They were doing work for Airbus, Boeing and the airlines,” recalls Janssen. “We developed a featherweight container with a carbon/aramid fiber composite monocoque, which is still not matched in low weight today,” he says. Though Holland Composites made a few thousand of these, the market quickly became saturated with low-cost FRP products.

OOA-cured structures. Large carbon composite structures for its DNA Performance Sailing brand of foiling multihull sailboats are cured in flexible ovens (right) comprising insulated panels with heating and air circulation computer-controlled from an exterior unit (inset).
Marine remains a core strength
In 1999, the Dutch Navy approached Holland Composites to produce solid glass fiber composite sonar domes for submarines. “These were traditionally built in two halves which were bonded together,” says Janssen, “but the seam causes a disruption in the field of ‘view.’ We were asked to build these in one piece. These sonar domes are large — 11.5 by 3 by 3 meters and 45 to 110 millimeters thick — and difficult to infuse, comprising 5,000 kilograms of vinyl ester/epoxy hybrid resin supplied by Romar-Voss Composites (Roggel, Netherlands). The finished structure weighs 6,500 kilograms. They must be rigid and resist slamming loads because they are located at the forward section of the hull. “We also have to match the density and sonar transparency of water,” says Janssen. “We do this for destroyer-type vessels for quite a few naval forces around the world.”
At the other end of the weight spectrum are the DNA performance foiling multihulls. “Our small boats were the first foiling catamarans in competition,” says Janssen. Holland Composites also produces the composite hydrofoils for record-setting racing yachts like MOD70’s Team ARGO and Beau Geste. “We have a technique in-house that can create really highly loaded parts without failure, and a unique one-shot production method for these very high-performance foils,” he adds. “We work with the best sailors in the world to reach the next level of foiling performance and produce all of the foils for the NACMA17 Olympic class boats.”
The lightweight CFRP deckhouse that Holland Composites produces for Windcat Workboats wind farm service/support vessels (see “Composite deckhouses cut weight”) uses resin-infused CFRP foam sandwich construction for stiffness to achieve a large, open span without pillars inside the cabin. “The monocoque deckhouse is lightweight enough that we can put it on good dampeners to isolate [it] from engine and wave vibration in the hull,” says Janssen. “Windcat is known for its really quiet ride, and the boats are well-liked by the large wind turbine OEMs. All of these wind farms must be maintained, so there is a new market for high-speed catamarans of 50 to 60 feet in length.”

Holland Composites supplied the structural composite facade for the University of Groningen Life Sciences building, using their translucent RAFICLAD panel system and large (3.6 by 3.3 meter) panel sizes, achieving weight savings and maximum thermal insulation.
Entry into architecture
In the early 2000s, facing a shortage in university student housing — with 3-4-year waiting lists — the Dutch government began a search for alternative solutions. “We had developed a composite capsule for another customer and thought if we enlarged it to be a standalone living unit, we could stack these and provide a solution,” says Janssen. This became the Space Box, a 6-meter-long by 3-meter-wide by 3-meter-high modular building unit that was an instant success.
“Delft University of Technology initially trialed 125 units,” says Janssen. “They were a funky shape, and we made them in bright colors. They were also very energy-efficient.” Holland Composites sold 2,000 units but quickly found itself in new territory: “We didn’t know anything about the building industry,” he says, “but we had to arrange the electricity, sewer — the whole bit. All of a sudden, we were the main contractor.”
Gaining notice from architects, Holland Composites was chosen in 2004 to work on the Life Sciences building for the University of Groningen (Groningen, Netherlands). The nine-story building was reportedly the first structural composite facade of this size, covering 9,220 square meters. “The original design was very heavy, but we were able to save weight,” notes Janssen. “Also, there were instrumented labs that faced south, so thermal insulation was an issue. If you build in big panels, you can reduce thermal leakage, but you need greater stiffness and load-carrying capability, which composites can provide.”
Holland Composites made the 3.6-by-3.3-meter by 200-millimeter-thick curtain wall facade panels using glass fiber-reinforced polyester hybrid resin and foam core. Janssen contends that “when using a metal frame plus cladding construction approach, you can never really hit the R-value [thermal resistance] theoretically possible. But with cored composites, which integrate the structural frame and cladding into a single panel, we not only hit that theoretical value but exceeded it.”
Holland Composites also succeeded in aesthetics, matching the building’s theme and natural setting with its translucent RAFICLAD composite panels, which feature glass fiber reinforcement in a plant-like, fibrous form. Being translucent, these green-tinted bio-inspired exteriors allowed light to transmit into the building’s interior. RAFICLAD is also used to produce photoprint facades and unusual designs, highly valued by architects and their clients.

Seventy-five 40 by 60-meter composite sections were shipped to Israel, laminated together and hoisted into place to create the wing-like roof sections for the Yitzak Rabin Centre in Tel Aviv.
“Everything we do is structural”
For the Yitzak Rabin Centre (Tel Aviv, Israel), the company was asked to build wing-like roof structures that would be too heavy if made from concrete. “Again, we made the largest sections possible,” says Janssen. Seventy-five 40-by-60-meter sections were resin infused using glass fiber and epoxy-based vinyl ester resin, and then shipped to Israel. On site, these were laid upside down into jigs in order to laminate them together into “wing roofs” with a maximum span of 31 meters. Janssen notes that the project was very challenging structurally. “These panels are 200 to 300 millimeters thick and hold the glass facade together, including an 11-meter cantilever section. The composite material can withstand all of the forces, giving you the possibility to design such free-hanging roof spans.”
The Fletcher Hotel tower is another such project, completed in 2012-2013. It began as a shopping mall next to a highway but required a substantial acoustic attenuation in the structure after the decision was made to convert the building to a high-end hotel. “The concrete skeleton could not cope with much additional load, so we were called to provide a lightweight solution,” says Janssen. Holland Composites devised 8.5-by-3-meter composite panels to which the plate glass facade could be fastened. “The glass actually hangs onto our panels, which helps to handle the load,” he points out. “We then fastened our panels to the concrete skeleton. This combination of the glass in front of the composite sandwich panels with the airgap in between creates an enormous acoustic barrier.” Each composite panel was paint-ready for interior walls on one side and finished with UV-resistant coatings on the glass-facing, exterior side.
“This was also a very fast way to mount cladding to a round-shaped building,” says Janssen. “We mounted the complete facade in one step and achieved an insulation R value of 8, which is twice the rating of normal building exterior materials.” Expanding on this idea, Janssen says he believes energy neutrality is critical to future building construction. “Not much energy is needed to heat the buildings that use our structural composite cladding, so our approach is very efficient to achieve a net-zero footprint. BREEAM is the Dutch certification for energy efficiency, and the first two buildings that achieved this use our composites.”

For the Fletcher Hotel, Holland Composites realized an aesthetic, noise-reducing exterior by attaching curved composite panels to the building’s concrete skeleton, to which the glass facade could be fastened without adding excessive dead load.
Janssen singles out the Stedelijk Museum of contemporary art in downtown Amsterdam as the pinnacle of Holland Composites’ technical building projects (see “Big museum, big structures”). “It was an extreme exercise in managing thermal expansion and illustrates what we do.” Holland Composites has also pioneered earthquake-proof structural facades, which are now required in certain parts of the Netherlands, Janssen explains, because the soil has been destabilized due to hydraulic fracturing (fracking). The Wiebenga building in Groningen features an earthquake-proof facade that can move 30 centimeters without failure. “Typical steel and concrete cannot handle this type of movement,” he adds.
Though balancing the myriad requirements with cost and schedule is a challenge when building structures, Janssen notes the largest issue currently is fire resistance. “Wrong implementations of composites have brought the composites industry a bad name in this regard,” he explains. “We now use only fire-resistant materials on these building projects and complete fire testing per approved regulations.”

Holland Composites builds blades for tidal turbine generators using carbon fiber prepreg, cured in an autoclave, to handle the large loads placed on these low-speed, high-torque structures.
Offshore and renewable energy
Holland Composites also has long-term contracts in the offshore oil and gas industry. “Composites here offer not just light weight and corrosion resistance, but also easy repair,” says Janssen. “Offshore rigs and vessels are not allowed downtime. However, repair to metal structures requires welding and sparks, so production has to be stopped due to fire hazard. We can patch composites without this disruption.” The company has new clients requesting such products for a variety of offshore constructions.
It also has manufactured blades for tidal turbines. The harvesting of tidal energy is still new, says Janssen, but the first projects have been completed and the results are impressive. “Tidal turbines offer a reliable energy source,” he explains. “The tides are always there, compared to wind and solar, so you can reliably predict the power output, which is key for power companies.” Holland Composites uses autoclave-cured carbon fiber prepreg for these blades because the loads are enormous. “The blades move at low speed but with high torque,” says Janssen. “You want the maximum translation of rotor speed into the motor to produce power, so the turbine manufacturers need strong but efficient structures that are shaped to get as much energy as possible out of tidal movements.”
Each turbine has two 3-meter-long blades that are 18 millimeters thick. There are five turbines per tidal generator. “The load on these turbine blades is described as equal to a 13,600-horsepower tugboat going forward in full power,” says Janssen, “but the customer also needs blades that are stiff, lightweight and low-maintenance with good fatigue resistance for durability. Steel would have been too heavy, making the generators less efficient.” Holland Composites makes only the blades; fairings, nose cone and non-structural cladding are made by FRP fabricators.
Future-oriented facility
The tour begins in the layup area, which features a large layup table, parts for the DNA performance sailboats and a variety of CFRP foils being readied for installation. The ceiling is low here because of a mezzanine for materials storage. This opens onto a high-ceilinged production floor, featuring a Zünd (Altstätten, Switzerland) automated cutting machine just beyond the layup area. The cutter has a 5.7-by-2.8-by-0.3-meter cutting range to process prepreg, dry fiber and foam materials up to 25 millimeters thick.

The Zünd automated cutter in the foreground supplies cut reinforcements and foam to the layup area, which can be seen in the back, at right, with the materials storage mezzanine above. The enclosed tooling area lies behind the yellow roll-up door, seen here behind the side of the CMS machining center, which is next to the Zünd cutting table.
Turning around from the Zünd cutter, we walk to a glass-enclosed tooling room that abuts the layup area. Entering through a yellow roll-up door, there are multiple tools in process and parts are being cured under vacuum bags. “We make our own molds,” says Janssen. “For CFRP parts, we use CFRP or aluminum for the tooling, as well as ventilation holes for air circulation within the tools, which helps to ensure even curing across the part.”

The CMS machining center is situated between the cutting table on its left (out of view) and the autoclave (far right, against wall).
Coming back out of the tooling room, we pass the 5-by-2-by-1.8-meter 5-axis CNC milling center (CMS SpA, Zogno, Italy) and can see the 6.5-by-2.2-meter autoclave (Tankbouw Rootselaar, Nijkerk, Netherlands). “We typically cure at 125° C with a pressure of 6 bar,” Janssen notes.

The autoclave is also seen below with a CFRP tool (note holes for air ventilation) and large CFRP foil being cured under vacuum bag for a performance multihull sailboat.
The wall beside the autoclave cuts the production area into two halves, running the length of the building along the tooling room. We turn around and pass through a door to the second half of the Holland Composites facility, which contains a waterjet cutting machine (8-by-2-by-0.5-meter cutting range), several ovens sized up to 15-by-10-by-3.5 meters, and the company’s 19-by-12-by-3.5-meter paint booth. “Currently, we are producing large panels for a project in Qatar and a series of CFRP deckhouses for the Windcat boats,” says Janssen.
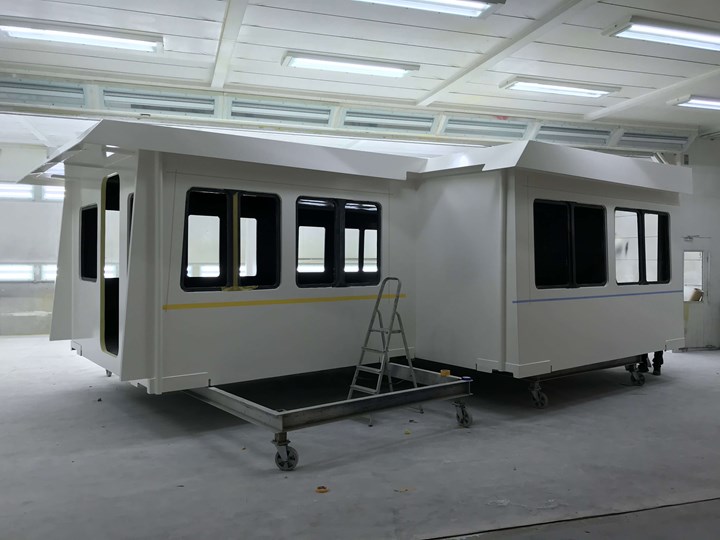
The CFRP deckhouses that Holland Composites produces for Windcat Workboats catamarans are painted in the company’s 19-by-12-by-3.5-meter paint booth.
Holland Composites’ latest installation is a Massivit 3D (Lod, Israel) 1800 Pro printer with a build volume of 145 by 111 by 180 centimeters. “We are partners innovating 3D printing of molds using three printheads, where two are printing the skins of a sandwich and the center nozzle prints the infill or lattice structure in between,” Janssen explains. “We will use fiber-reinforced material in future developments, but for now, we can print accurate tooling with minimal milling needed. We use much less material and see very fast mold production times. We now have a complete process chain, with the ability to go from design to molds to painted parts in a short time period.”
He notes that the company is still exploring how to increase its use of automation to further advance its products, but without driving up cost. “It comes down to ingenuity. We are drawn to highly complex problems that few others dare to tackle, but as boatbuilders, we have always had to be very creative with limited resources. For what we do in composites, we see many opportunities in the future.”
Related Content
Carbon fiber, bionic design achieve peak performance in race-ready production vehicle
Porsche worked with Action Composites to design and manufacture an innovative carbon fiber safety cage option to lightweight one of its series race vehicles, built in a one-shot compression molding process.
Read MoreOptimized approach to predict delamination failure in CFRTP structures
ARRK Engineering and Mitsui Chemicals improved delamination prediction accuracy to help optimize absorbed energy/failure load for an overmolded TAFNEX CF/PP UD tape bumper beam.
Read MoreOptimizing a thermoplastic composite helicopter door hinge
9T Labs used Additive Fusion Technology to iterate CFRTP designs, fully exploit continuous fiber printing and outperform stainless steel and black metal designs in failure load and weight.
Read MoreNine factors to consider when designing composites cure tooling
Gary Bond discusses the common pitfalls and compromises when designing good cure tooling and their holistic significance for a robust composite production process.
Read MoreRead Next
Developing bonded composite repair for ships, offshore units
Bureau Veritas and industry partners issue guidelines and pave the way for certification via StrengthBond Offshore project.
Read MoreAll-recycled, needle-punched nonwoven CFRP slashes carbon footprint of Formula 2 seat
Dallara and Tenowo collaborate to produce a race-ready Formula 2 seat using recycled carbon fiber, reducing CO2 emissions by 97.5% compared to virgin materials.
Read More“Structured air” TPS safeguards composite structures
Powered by an 85% air/15% pure polyimide aerogel, Blueshift’s novel material system protects structures during transient thermal events from -200°C to beyond 2400°C for rockets, battery boxes and more.
Read More