Toho Tenax rolls out thermoplastic recycling solution
Tenax-E COMPOUND rPEEK CF30 features waste materials from production of the company's ThermoPlastics material and contains semicrystalline PEEK polymer.
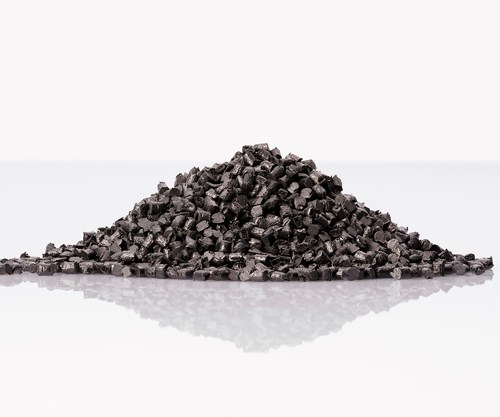
Toho Tenax' Tenax-E COMPOUND rPEEK CF30 features waste materials from production of the company's ThermoPlastics material and contains semicrystalline PEEK polymer.
Toho Tenax Co. Ltd. (Tokyo, Japan) announced on March 7 that its German subsidiary Toho Tenax Europe GmbH (TTE) has developed a new compound, based on recycled thermoplastic carbon fiber material and PEEK (polyetheretherketone) thermoplastic. A serial aircraft wing access panel was manufactured as a demonstrator part.
Tenax-E COMPOUND rPEEK CF30 is a reinforced material that combines waste materials generated during processing of Tenax ThermoPlastics and recycled semicrystalline PEEK polymer, which contains 30% carbon fiber by weight and offers high performance in strength and stiffness for injection molding applications.
This compound, says Toho Tenax, has almost identical performance to virgin standard material in terms of tensile modulus and strength, which also includes elongation, viscosity, chemical resistance, abrasion and a very low moisture to absorption ratio. The created value of this compound is linked to the combination of high-performance materials as well as a price point 40-60% that of virgin carbon fiber-reinforced PEEK compounds.
Toho Tenax says it worked with it aircraft OEM manufacturer and Sintex NP Group to fabricate the wing access panel. The Sintex NP Group was selected as the partner responsible for the part manufacturing process.
Toho Tenax developed three ThermoPlastic Recycling Solutions: Compound, Chips and Crushed. They are reinforced material combinations made of recycled Tenax TPCL and Tenax TPWF and recycled semicrystalline polyetheretherketone (PEEK) polymer. The TPCL material (Thermoplastic Consolidated Laminates) using PEEK are used to press-form cleats, brackets and clips in the fuselage structure of the Airbus A350 XWB. Toho Tenax says it supplies 10,000-15,000 sheets of material per year (depending on build rate) for this program.
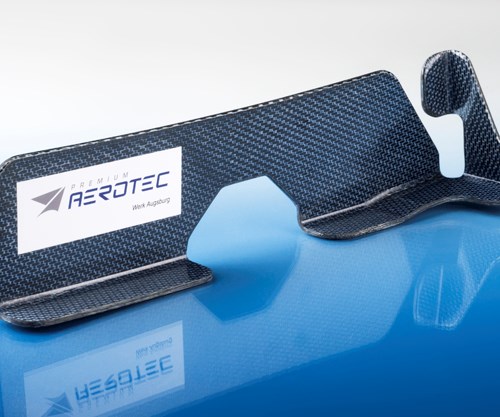
Airbus A350 XWB clip.
Related Content
-
Cryo-compressed hydrogen, the best solution for storage and refueling stations?
Cryomotive’s CRYOGAS solution claims the highest storage density, lowest refueling cost and widest operating range without H2 losses while using one-fifth the carbon fiber required in compressed gas tanks.
-
The state of recycled carbon fiber
As the need for carbon fiber rises, can recycling fill the gap?
-
Manufacturing the MFFD thermoplastic composite fuselage
Demonstrator’s upper, lower shells and assembly prove materials and new processes for lighter, cheaper and more sustainable high-rate future aircraft.