AIT Bridges unveils composite tub girder bridge system
The fiber-reinforced polymer tub girder system provides an affordable, long term solution to traditional steel and concrete medium span deck bridges.
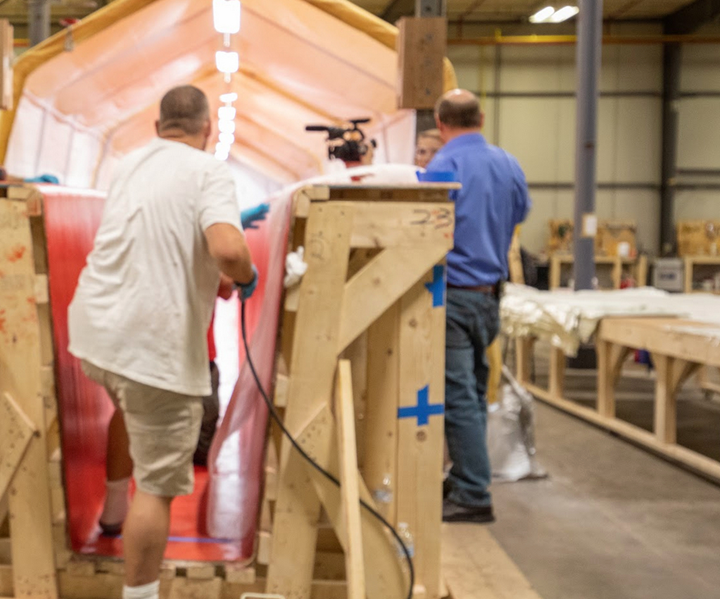
Source | AIT Bridges
AIT Bridges (Brewer, Maine, U.S.), a division of Advanced Infrastructure Technologies (AIT), a designer and supplier of composite bridge systems and structural components for commercial construction, announced on August 6 the addition of a composite tub girder, known as the AIT CT Girder, to its composite bridge system offerings.
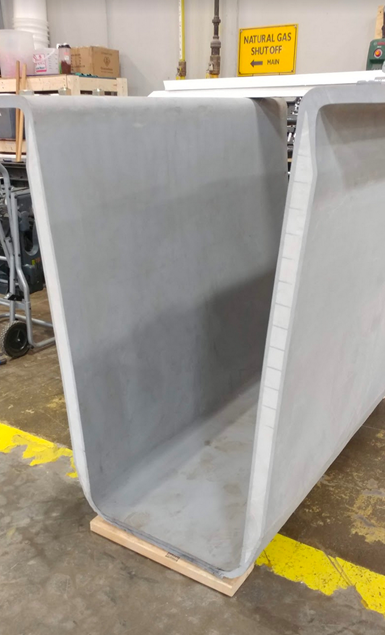
The AIT CT Girder consists of lightweight fiber-reinforced polymer (FRP) tub girders supported on standard foundations with either a precast concrete panel deck or a cast in place concrete bridge deck. Source | AIT Bridges
“Our composite tub girder is, ultimately, going to be a game-changer in the bridge construction sector,” says Brit Svoboda, chairman and CEO, AIT Bridges. “It is versatile, strong but lightweight, affordable and ultimately intended to replace concrete and steel girders in the marketplace.”
Developed in cooperation with The University of Maine’s Advanced Structures and Composites Center (Orono, Maine, U.S.), AIT Bridges is known for its composite arch bridge system, which has been commercially available since 2010.
“For anyone that knows of our arch system, the AIT CT Girder is a natural extension of what we already offer,” explains Svoboda. “It can be used as a highway, rail or pedestrian bridge, even as part of a building structure, parking garage system, marine structure and in many other places where steel and concrete support girders are used.”
The AIT CT Girder was created to provide an affordable, long term solution to traditional steel and concrete medium span deck bridges. It consists of lightweight fiber-reinforced polymer (FRP) tub girders supported on standard foundations with either a precast concrete panel deck or a cast in place concrete bridge deck. The company says spans up to 100 feet are achievable.
AIT Bridges claims the tub girder system offers several advantages for bridge construction. The manufacturing process and installation is said to yield a reduced carbon footprint over conventional steel and concrete girders. The girder requires little maintenance, is naturally corrosion resistant and is made of materials designed to withstand environmental challenges. The system is 50% lighter than steel and 75% lighter than concrete girders. This reduction in weight allows for a decrease in large equipment on the construction site and reduces transportation costs.
According to AIT Bridges, the CT Girder has the lowest life cycle cost in the industry and in many cases offers a lower initial cost than similar steel and concrete solutions.
Related Content
-
Composite wrap system combats corrosion in industrial tank repair
A fiberglass and carbon fiber composite wrap system enabled an Australian nickel mine to quickly repair a stainless steel ammonium sulphate feed tank and protect against future corrosion.
-
Owens Corning initiates review of strategic alternatives for glass fiber business
Owens Corning considers alternative options like a potential sale or spin-off as part of its transformative move to strengthen its position in building and construction materials.
-
CirculinQ: Glass fiber, recycled plastic turn paving into climate solutions
Durable, modular paving system from recycled composite filters, collects, infiltrates stormwater to reduce flooding and recharge local aquifers.