Arris, U.S. Army and LIFT launch collaborative project to lightweight combat vehicles
Project will apply Arris’ Additive Molding technology to demonstrate significant vehicle weight reductions via part consolidation, topology optimization and a continuous carbon fiber composite structure.
Share
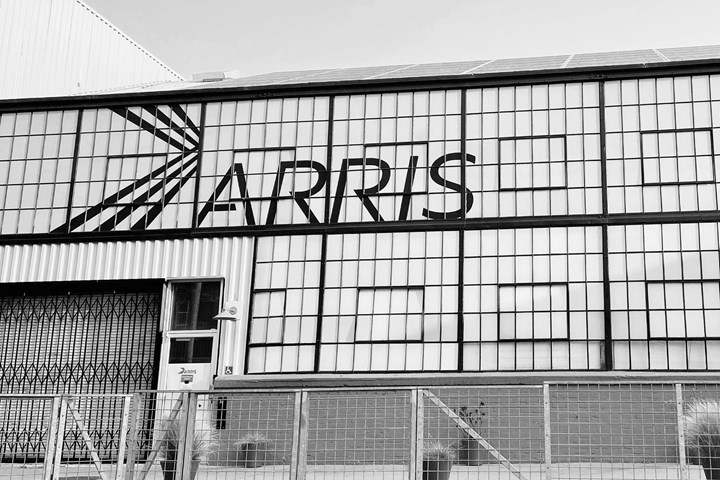
Photo Credit: Arris Composites.
Arris Composites (Berkeley, Calif., U.S.), an advanced manufacturer enabling the use of high-performance composites in mass-market products, transportation and industrial applications, has announced a project with the U.S. Army’s Michigan-based Combat Capabilities Development Command Ground Vehicle Systems Center (DEVCOM GVSC) focused on vehicle seats to demonstrate significant vehicle weight reductions through part consolidation, topology optimization and an aligned continuous carbon fiber composite structure.
This initial project will use Arris’ scalable Additive Molding manufacturing technology platform. The project is being contracted through LIFT (Detroit, Mich., U.S.) a public-private partnership between the Department of Defense (DOD), industry leaders and academia and operated by the American Lightweight Materials Manufacturing Innovation Institute (ALMMII).
“Working with LIFT and the Army to bring together advanced composites and advanced structural design in a key vehicle subassembly is an important step in advancing vehicle architectures,” says Ethan Escowitz, CEO and founder at Arris. “This pioneering work with LIFT will pave the way for broader adoption of lightweighting, and realization of the associated performance, efficiency and sustainability benefits.”
Army vehicles have been increasing in weight over time due to new technology and safety components for soldiers, and this partnership is part of the Army’s effort to advance the use of cutting-edge technologies that enable high-strength, lighter, more fuel-efficient tactical vehicles with superior mobility and protection. By replacing an assembly of metal components in crew seats with a single continuous fiber-reinforced composite structure, Arris says it will demonstrate the advantages of its manufacturing technology for broader vehicle applications.
“The real significance of a weight savings approach for vehicle design depends on its broader applicability. High-end, high-cost vehicles have lightweighting approaches that don’t translate to mass production and cost-sensitive industries. Arris’ unique ability to combine lightweight materials, lightweight structural designs and cost-effective manufacturing is an important set of capabilities to drive LIFT strategic objectives,” says Nigel Francis, CEO and executive director at LIFT. “Our collaboration with Arris and the Army is an important step in lightweighting vehicle structures for the military and the competitiveness of the U.S. automotive industry as a whole.”
Related Content
-
Infinite Composites: Type V tanks for space, hydrogen, automotive and more
After a decade of proving its linerless, weight-saving composite tanks with NASA and more than 30 aerospace companies, this CryoSphere pioneer is scaling for growth in commercial space and sustainable transportation on Earth.
-
PEEK vs. PEKK vs. PAEK and continuous compression molding
Suppliers of thermoplastics and carbon fiber chime in regarding PEEK vs. PEKK, and now PAEK, as well as in-situ consolidation — the supply chain for thermoplastic tape composites continues to evolve.
-
Recycling end-of-life composite parts: New methods, markets
From infrastructure solutions to consumer products, Polish recycler Anmet and Netherlands-based researchers are developing new methods for repurposing wind turbine blades and other composite parts.