Composites help offset battery weight for electric waste trucks
Fraunhofer IWS develops cost-effective joining of aluminum frames and fiber glass-reinforced thermoplastic panels.
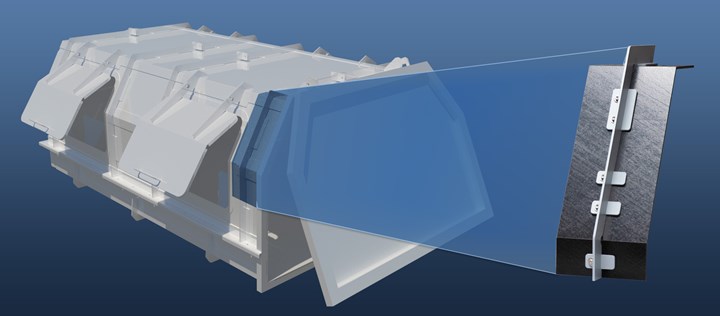
Constructive concept of a container superstructure for a municipal waste collector in alternative-mixed construction based on aluminum profiles and composite panels. Photo Credit: EBF Dresden/Fraunhofer IWS Dresden
The Fraunhofer Institute for Material and Beam Technology IWS Dresden, along with five other Central German research institutes and companies have recently joined forces for the UTILITAS (”Ultralight structures for commercial vehicles in municipal service operations”) project, which aims at sustainable and cost-effective solutions supporting municipalities to meet their climate protection goals with locally available resources. Together, the companies plan to construct better collection containers made of light metals and fiber-reinforced composite plastics. These solutions will replace the heavy steel superstructures of classic waste trucks with an alternative that will be one-third lighter.
“This new generation of electric vehicles would then be able to transport as much waste per load as a classic small waste truck,” emphasizes Annett Klotzbach, who heads the Bonding and Fiber Composite Technology group at Fraunhofer IWS Dresden.
However, the project’s overarching goal means more than just constructing better refuse vehicles. “This is why the alliance is developing not only the container, but also the related practical production technologies,” explains Klotzbach. “The important point here is to ensure that the new containers can also be built profitably in small series and be quickly repaired in local workshops.” The project partners are said to be relying on container constructions made of aluminum frames and fiber glass-reinforced thermoplastic panels, and are also testing various joining methods.
“The container prototypes should be ready by beginning of 2021,” announces Klotzbach. ”We expect the first waste collection vehicles to be on the road within two years.”
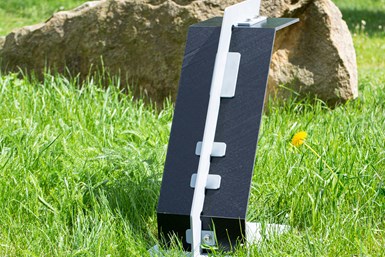
Partial section of the superstructure with the four joining technologies applied: Adhesive bonding, mechanical joining using inserts, thermal direct joining using HPCi and hybrid joining (adhesive bonding & mechanical joining). Photo Credit: Fraunhofer IWS
One of the novel joining technologies developed at Fraunhofer IWS, the “HeatPressCool-integrative” (HPCi) is additionally being employed. A laser first roughens the aluminum components, creating grooves in the metal that are thinner than a pin and only about 200 micrometers deep. Subsequently, the tool presses the plastic component against the aluminum strut and briefly heats the metal. During this process, the thermoplastic melts on the aluminum surface, flows into the laser-molded grooves and is anchored there during cooling. After a few seconds, aluminum and composite plastic are said to be permanently and firmly bonded.
In the course of the development cooperation, the IWS engineers also aim at determining the long-term durability of the joined lightweight container compared to screw or adhesive solutions. According to Fraunhofer IWS, the container will have to withstand high loads in daily use, for example when the vehicle mechanics compress the collected waste. In previous experiments, the HPCi-joined containers proved to be particularly durable and much easier to repair than glued constructions. Measurements have shown that the HPCi joints can withstand tensile forces equivalent to the pressure of a hydraulic arm of up to 25 megapascals.
The IWS experts are convinced that the new joining process is not only suitable for waste container constructions, but also for lightweight constructions in aircraft, railways, industrial facilities, or ships. Industrial customers also intend to use HPCi in the production of dishwashers and other household appliances. Meanwhile, in order to support the broad practical application of the project’s new joining technology, the Dresden researchers say they have developed compact HPCi joining guns that are not much larger than a standard hand drill. They can be modularly mounted on robots, for example, in order to quickly start a small lightweight production run. Since this new tool is so promising, the Fraunhofer scientists also intend to set up a company soon that will series-produce the HPCi joining guns.
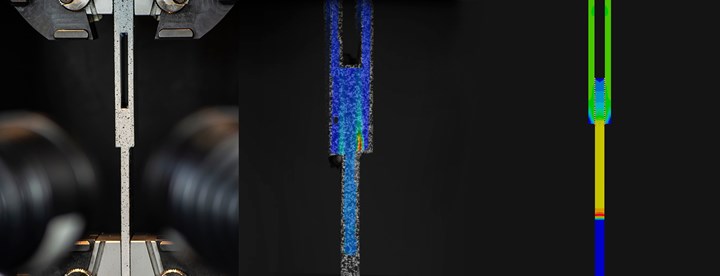
Mixed joint of glass fiber-reinforced plastic and aluminum in the form of a bonded double overlapped tensile shear test specimen. Left: Mechanical test with optical strain measurement using black and white speckles. Middle: Colored stress curve of a snapshot taken during mechanical testing. Right: Stress image of the joint in the simulation tool PAM-Crash. Photo Credit: Fraunhofer IWS
With the state of current developments, the company adds, the first electric waste trucks with new lightweight containers will soon shape the urban scene of many large cities. “The container prototypes should be ready by beginning of 2021,” announces Klotzbach. ”We expect the first waste collection vehicles to be on the road within two years.” The developers envisage municipal companies as the main customers.
Six partners are involved in the UTILITAS project: Fraunhofer IWS Dresden, the Chair for Structural Lightweight Design and Plastics Processing at Chemnitz University of Technology (Chemnitz), Marko Pfaff & Co. Spezialfahrzeugbau GmbH (Bad Lausick), Car systems Scheil GmbH & Co. KG, the PROFIL Verbindungstechnik GmbH & Co. KG (Friedrichsdorf) and the EBF Dresden GmbH (Dresden).
Related Content
Bioabsorbable and degradable glass fibers, compostable composite parts
ABM Composite offers sustainable options and up to a 60% reduction in carbon footprint for glass fiber-reinforced composites.
Read MoreOwens Corning initiates review of strategic alternatives for glass fiber business
Owens Corning considers alternative options like a potential sale or spin-off as part of its transformative move to strengthen its position in building and construction materials.
Read MoreAl Seer Marine, Abu Dhabi Maritime unveil world’s largest 3D-printed boat
Holding the new Guinness World Record at 11.98 meters, the 3D-printed composite water taxi used a CEAD Flexbot to print two hulls in less than 12 days.
Read MoreNovel composite technology replaces welded joints in tubular structures
The Tree Composites TC-joint replaces traditional welding in jacket foundations for offshore wind turbine generator applications, advancing the world’s quest for fast, sustainable energy deployment.
Read MoreRead Next
EV battery enclosure inspires material, process innovations
High unit volume and low weight requirements for electric bus battery enclosures fueled development of TRB Lightweight Structures’ specialized epoxy system and automated composites production line.
Read MoreAll-recycled, needle-punched nonwoven CFRP slashes carbon footprint of Formula 2 seat
Dallara and Tenowo collaborate to produce a race-ready Formula 2 seat using recycled carbon fiber, reducing CO2 emissions by 97.5% compared to virgin materials.
Read More“Structured air” TPS safeguards composite structures
Powered by an 85% air/15% pure polyimide aerogel, Blueshift’s novel material system protects structures during transient thermal events from -200°C to beyond 2400°C for rockets, battery boxes and more.
Read More