CTC GmbH and KTM E-Technologies develop innovative joining technologies for urban air mobility
Partnership develops lightweight approaches including Conexus technology for robotic ultrasonic welding of CFRP laminates.
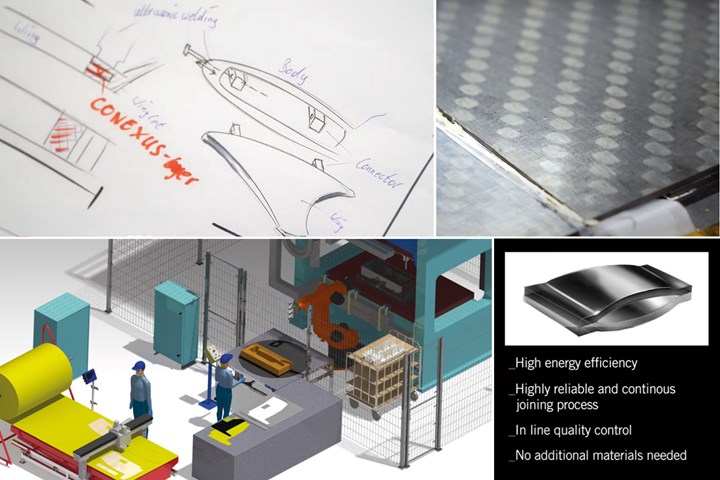
To implement smart and efficient lightweight designs for future competitive urban air mobility (UAM) systems, Airbus' Composite Technology Center (CTC GmbH, Stade, Germany) and KTM E-Technologies (Salzburg, Austria) have merged their know-how from the aerospace and motorsports/automotive industries. Their aim is to identify, combine and develop holistic lightweight approaches for UAM in order to enable innovative architectures in collaboration with the OEMs.
In addition to the holistic system approach, this collaboration focuses on the joint development of key technologies, such as efficient multi-material designs and innovative joining technologies.
Innovative joining technologies
Three essentials for future joining technologies are:
- Fiber-optimized designs with high mechanical performance,
- Improved eco-efficiency by avoiding additional auxiliary materials,
- A highly automated process.
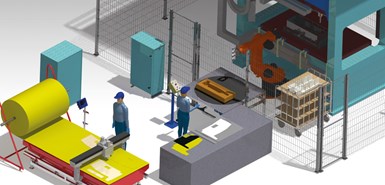
Robotic ultrasonic welding is integrated into an automated production cell. Photo credit: CTC
The robotic ultrasonic welding process, developed at CTC, fulfills all three of these requirements, offering a promising approach to join both thermoplastic and thermoset composite materials efficiently and quickly. It is based on the application of high-frequency, ultrasonic vibrations and can be used to create both spot and continuous welds. This welding process features high energy efficiency, a small heat-affected zone, rivet-free joining, short process times and the ability for all process-relevant data to be recorded online and used for quality assurance.
Merging of aerospace and automotive experience boosts high performance and lightweight design. Photo credit: KTM E-Technologies
When welding thermoset materials, the Conexus coupling layer, developed by KTM E-Technologies, is used as an enabler. This thermoplastic material is adapted to the specific thermoset matrix being used and can be applied directly to the component surface with reliability during the part manufacturing process, for example, in a press. During subsequent assembly, not only can fiber-reinforced components be joined together but injection-molded brackets or stiffening elements can also be integrated via welding or overmolding directly onto the part.
Together with CTC, cross-industry opportunities and new mobility solutions are being created,” says Stefan von Czarnecki, director sales and business development for KTM E-Technologies. “This comprehensive cooperation opens up new possibilities for smart and efficient lightweight construction.”
“New mobility concepts offer enormous potential,” says Marc Fette, CEO for CTC. “However, they also present significant challenges with regard to weight, cost, rate capability, quality level and ability to be certified. Robotic ultrasonic welding is one promising solution for both thermoplastic and thermoset composite materials to meet these challenges. We look forward to continued knowledge transfer and cross-industry collaboration with KTM E-Technologies, that will, no doubt, produce many other enabling solutions.”
Related Content
-
Manufacturing the MFFD thermoplastic composite fuselage
Demonstrator’s upper, lower shells and assembly prove materials and new processes for lighter, cheaper and more sustainable high-rate future aircraft.
-
Developing repairs for thermoplastic composite aerostructures
HyPatchRepair project proves feasibility of automated process chain for welded thermoplastic composite patch repairs.
-
Plant tour: Sekisui Aerospace, Orange City, Iowa, Renton and Sumner, Wash., U.S.
Veteran composites sites use kaizen and innovation culture to expand thermoplastic serial production, 4.0 digitization and new technology for diversified new markets.