HAV Group receives preliminary approval for hydrogen-based energy system for ships
Norwegian Maritime Authority approves LH2 tank design under the FreeCO2ast project, paving the way for commercialization of the zero-emissions marine system.
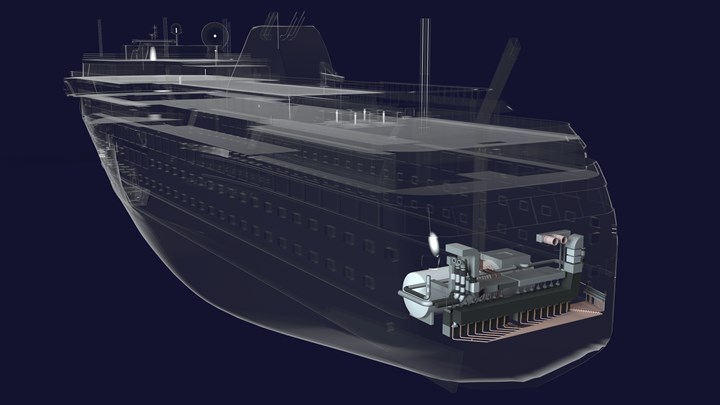
HAV hydrogen-based marine system rendering. Photo Credit: HAV Group ASA
HAV Group ASA (Fosnavaag, Norway) is said to be one of the first companies to be granted preliminary approval by the Norwegian Maritime Authority for the hydrogen-based energy system developed in the FreeCO2ast project. The approval is reported to be a major step towards the commercial use of hydrogen fuel by a commercial vessel.
“Hydrogen can be the key to achieve zero-emission shipping. This regulatory approval takes us an important step towards commercializing our hydrogen solutions and realizing the zero-emission ambition,” Kristian Osnes, project manager for the FreeCO2ast Project and managing director at HAV Hydrogen, says. “The learnings from this comprehensive approval process are highly important for HAV Hydrogen’s competence in designing hydrogen system solutions.”
According to the issued statement, HAV Group’s alternative design — comprising a liquid hydrogen (LH2) tank below decks — is considered feasible and sound in accordance with IMO guidelines on alternative design (MSC.1/Circ.1455) and is ready to advance into the final design phase.
“We are now in a position where we can offer shipowners the necessary competence in selecting hydrogen system solutions and guide them through their approval processes, as well as delivering the marine zero-emission systems. The key is to align the right technology for the right need at the right time,” Osnes adds.
HAV Hydrogen’s energy system is a spin-off from the FreeCo2ast project, which is currently developing a high-capacity hydrogen energy system that can be retrofitted onboard one of Havila Kystruten’s coastal cruise ships.
The FreeCo2ast project is supported by the Norwegian Research Council, Innovation Norway (Oslo, Norway) and Enova (Norway). Major project partners include Havila Kystruten and HAV Group’s subsidiaries HAV Design, Norwegian Electric Systems and HAV Hydrogen, in addition to the research institutions Sintef Ocean (Trondheim, Norway) and Prototech (Hordaland, Norway). Fuel cell manufacturer Powercell AB (Sweden) and tank system supplier Linde Engineering GmbH (Pullach im Isartal, Germany) have contributed with knowledge and expertise in their respective areas.
“The almost four years of cooperation with internal and external project partners in the FreeCo2ast project is a major contributor towards the preliminary design approval,” Gunnar Larsen, CEO of HAV Group ASA, adds. “The ability to cooperate closely with highly experienced sister companies covering both ship design, electrical integration and hydrogen systems, gives us a competitive edge as a group.”
Implications for composites
Though the use of composites is not specified, long-time Type IV composite pressure vessel manufacturer Hexagon Composites (Alesund, Norway), and its zero-emission spin-off Hexagon Purus Maritime (Alesund), estimates a 630% increase in tank revenues from 2025 to 2030.
“We are now seeing that the maritime requests and activities for hydrogen are rising quickly,” explains Jørn Helge Dahl, sales and marketing director at Hexagon Purus. “Hexagon Purus Maritime will develop onboard storage systems, from the shipside fuel line feeding into the storage and from the storage down to the fuel cell. We think composites are the ideal storage solution for maritime applications, due to the harsh environment, including corrosion.” For more details, see “The potential for hydrogen to fuel composites growth, part 1.”
CW also wrote about the SpaceTech4Sea project, where project coordinator Ocean Finance (Athens, Greece) worked with Cimarron Composites (Huntsville, Ala., U.S.) to develop a composite tank for cryogenic liquid natural gas (LNG) storage at -196°C that is certified for the marine market by the American Bureau of Shipping (ABS, Houston, Texas, U.S.). This tank will provide weight savings of more than 85% versus a conventional metal tank, according to the project partners, who have also completed a trade study looking at the technical and economic factors of using liquid versus gaseous hydrogen for marine vessels (see “CFRP pressure vessels for hydrogen”). Note that Cimarron Composites was acquired by Hanwha Solutions (Seoul, South Korea) in December 2020. The latter announced in 2021 that it will invest $130 million in a new production facility for Type IV pressure vessels in Opelika, Ala., U.S., part of its strategy to become a global leader in high-pressure tanks by 2030.
Related Content
Recycling hydrogen tanks to produce automotive structural components
Voith Composites and partners develop recycling solutions for hydrogen storage tanks and manufacturing methods to produce automotive parts from the recycled materials.
Read MoreHonda begins production of 2025 CR-V e:FCEV with Type 4 hydrogen tanks in U.S.
Model includes new technologies produced at Performance Manufacturing Center (PMC) in Marysville, Ohio, which is part of Honda hydrogen business strategy that includes Class 8 trucks.
Read MoreECOHYDRO project to enable recyclable composites for hydrogen storage
With the involvement of two schools from the Institut Mines-Télécom, the 4-year project aims to improve the intrinsic properties of a composite material based on Elium via four concrete demonstrators.
Read MoreComposites end markets: Batteries and fuel cells (2024)
As the number of battery and fuel cell electric vehicles (EVs) grows, so do the opportunities for composites in battery enclosures and components for fuel cells.
Read MoreRead Next
Developing bonded composite repair for ships, offshore units
Bureau Veritas and industry partners issue guidelines and pave the way for certification via StrengthBond Offshore project.
Read MoreAll-recycled, needle-punched nonwoven CFRP slashes carbon footprint of Formula 2 seat
Dallara and Tenowo collaborate to produce a race-ready Formula 2 seat using recycled carbon fiber, reducing CO2 emissions by 97.5% compared to virgin materials.
Read MoreVIDEO: High-volume processing for fiberglass components
Cannon Ergos, a company specializing in high-ton presses and equipment for composites fabrication and plastics processing, displayed automotive and industrial components at CAMX 2024.
Read More