Impossible Object offers high-performance, PEEK 3D-printed products at PA12 prices
Combination of the company’s proprietary CBAM process and lower cost source saves customers up to 80% and offers stronger, better performing products.
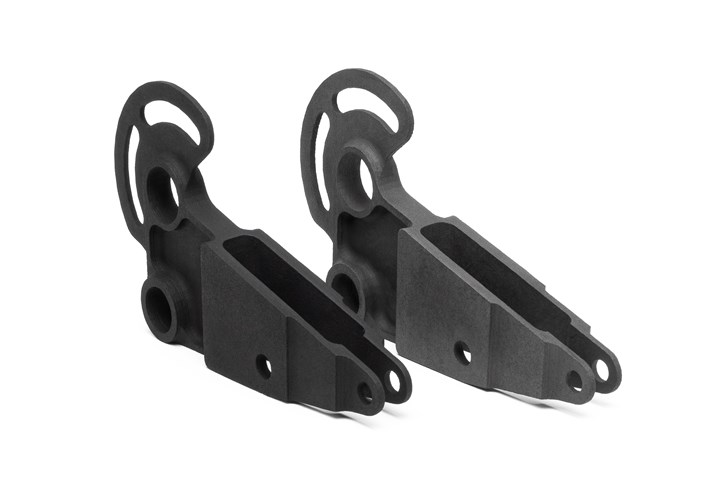
Carbon fiber Nylon (left) and carbon fiber PEEK (right). Photo Credit: Impossible Objects.
Impossible Objects (Northbrook, Ill., U.S.) is presenting its latest 3D printing advancement at RAPID + TCT 2021 this week in booth #E8237 to help manufacturers produce high-performance products: polyetheretherketone (PEEK) 3D-printed products at radically lower costs.
Impossible Objects, which developed the composite-based additive manufacturing (CBAM) process, has now radically reduced the cost of PEEK products, making them available at the price of conventional PA12 prices —due to a lower PEEK cost source and less material use during 3D printing — and saving up to 80% from product costs, says Robert Swartz, chairman and founder of Impossible Objects. In addition, he says, the products are said to be much stronger and show significantly better temperature performance than PA12 products produced by laser sintering or HP Multi Jet Fusion.
PEEK is a semi-crystalline, high-performance engineering thermoplastic known for its high-temperature performance, strength and chemical resistance that competes with metals in performance.
“PEEK is the absolute gold-standard material in today’s composite manufacturing, thanks to its incredible temperature performance and chemical resistance and strength, but its high cost keeps it out of reach for the majority of manufacturers,” Swartz says. “Our methods have reduced the cost of the material so much that PEEK is comparable to more common composite materials.”
At the same time, PEEK products are said to be superior for numerous applications, compared to PA12, as shown in tests comparing PEEK products from Impossible Objects’ CBAM process to PA12 products developed by HP’s Multi Jet Fusion process. PEEK products in these studies showed a tensile strength of 132 Mpa, compared to 50 Mpa for PA12, and a melting point of 343°C, compared to 210°C for PA12.
Impossible Object’s CBAM process also has several advantages compared to HP’s Multi Jet Fusion and laser sintering, including using fiberglass, a lower cost substrate; using about half of the polymer; and processing 10 times faster than the speed of fused deposition modeling (FDM).
“As a result of using less material in the process than our competitors, we are able to reduce our final costs for customers, no matter what polymer we use,” Swartz says. “Thanks to our lower cost sources for PEEK, we are able to provide PEEK at prices comparable to conventional polymers like PA12.”
Swartz notes that currently, the industries that often make use of PEEK are aerospace, automotive and aviation — many other industries and companies would benefit, except for the higher price tag. Lowering material cost, therefore, is important for broadening adoption of additive manufacturing (AM), and research has shown that costs of materials used in 3D printing can be higher than traditional manufacturing materials by up to a factor of eight on a per-weight basis.
“Our CBAM process has revolutionized 3D printing, offering faster speeds, better material properties and wider material selection,” Swartz adds. “Allowing more of our customers to use PEEK is another way that we are building on the promise of additive manufacturing to drive widespread innovation across sectors and industries.”
Impossible Objects’ proprietary CBAM technology can produce parts up to ten times faster than conventional fused deposition modeling (FDM) 3D printing. By combining high-performance polymers like nylon and PEEK with carbon fiber and fiberglass nonwoven materials, parts printed with Impossible Objects machines are reported to be stronger, lighter, have better dimensional accuracy and have better temperature performance than what’s possible with conventional 3D printing methods. The CBAM process can use a great variety of materials including carbon fiber and fiberglass paired with PEEK, PA6, PA12, elastomerics and most other thermoplastics.
Related Content
Plant tour: Albany Engineered Composites, Rochester, N.H., U.S.
Efficient, high-quality, well-controlled composites manufacturing at volume is the mantra for this 3D weaving specialist.
Read MorePlant tour: Spirit AeroSystems, Belfast, Northern Ireland, U.K.
Purpose-built facility employs resin transfer infusion (RTI) and assembly technology to manufacture today’s composite A220 wings, and prepares for future new programs and production ramp-ups.
Read MoreCombining multifunctional thermoplastic composites, additive manufacturing for next-gen airframe structures
The DOMMINIO project combines AFP with 3D printed gyroid cores, embedded SHM sensors and smart materials for induction-driven disassembly of parts at end of life.
Read MorePEEK vs. PEKK vs. PAEK and continuous compression molding
Suppliers of thermoplastics and carbon fiber chime in regarding PEEK vs. PEKK, and now PAEK, as well as in-situ consolidation — the supply chain for thermoplastic tape composites continues to evolve.
Read MoreRead Next
Impossible Objects, Ricoh 3D partner to produce high-strength 3D-printed composite parts
New material options for industrial customers across Europe to remove barriers to printing parts for drones, aircraft, automobiles, athletic gear and more.
Read MoreImpossible Objects, Owens Corning to produce new high-performance 3D printing materials
Collaboration will develop tailor-made materials for composite-based AM, bring CBAM process to industrial scale to compete with other high-volume manufacturing methods.
Read More“Structured air” TPS safeguards composite structures
Powered by an 85% air/15% pure polyimide aerogel, Blueshift’s novel material system protects structures during transient thermal events from -200°C to beyond 2400°C for rockets, battery boxes and more.
Read More