Kingfa supplies UD tapes for Ford door modules
Working closely with Brose Fahrzeugteile, Guangzhou-based CF supplier uses one-shot process to cut weight 35%.
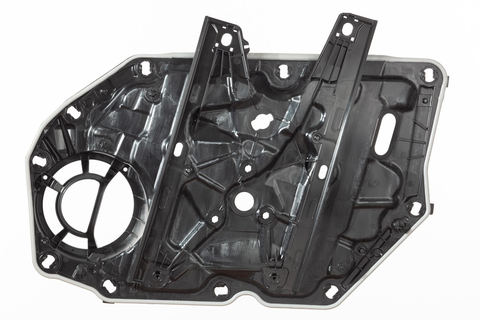
Door module carrier for the Ford Focus. Source | Kingfa
Kingfa Sci. & Tech. Co. Ltd. and its subsidiary Guangzhou Kingfa Carbon Fiber Materials Development Co. Ltd. (Guangzhou, China) have announced that they are supplying continuous fiber-reinforced materials for the mass production of lightweight door modules in the new Ford Focus.
In the development of a new continuous fiber-reinforced material called KingPly, Kingfa worked closely with the German system supplier Brose Fahrzeugteile (Coburg, Germany). Brose designed the carrier of the lightweight door module with the goal of significantly reducing weight without sacrificing performance. Brose also further increased functional integration. In this case, a weight saving of about 35% was achieved, compared with a carrier made of injection molded material using current technology. In the four-door Ford Focus, this means a reduction in vehicle weight by more than 1 kilogram compared to a door module carrier made of PP-LGF 30.
The material’s thin single layers of unidirectional (UD) tapes, under the brand name KingStrong, can be used to produce customer-specific semi-finished products in the form of plates called KingPly, which are tailored exactly to the application and requirements. In the case of the door module, a very thin but high strength multilayer material was developed, consisting of a polypropylene (PP) matrix with continuous glass fiber reinforcement. The material is said to give the component rigidity and strength.
“The semi-finished products, tailor-made with UD tape assemblies, now enable more efficient components that are even more capable of implementing the concept of lightweight design than the previously known materials of this type based on fabric,” says Martin Klocke, vice general manager automotive business of Kingfa Sci. & Tech. (Europe) GmbH, the European subsidiary based in Wiesbaden, Germany.
“With our newly developed materials, we have demonstrated the innovative strength of Kingfa and hope to be able to support our customers even better than before in their lightweight construction projects,” says Peng Xiao, general manager at Guangzhou Kingfa Carbon Fiber Materials Development.
According to Xiao, Kingfa has been investing in its production facilities over the past several years and is now prepared for large-volume production runs.
Kingfa believes its composite and injection molding materials can provide a solution for many cost-effective lightweight automotive applications.
Kingfa’s portfolio currently consists of UD tapes, chopped glass layers and organic sheets, which are predominantly based on glass fibers and thermoplastic matrices. For KingPly Organo Sheets, PP and PA6 are mainly used in automotive applications, while KingStron PP, PA6, ABS and HDPE UD tapes also offer opportunities outside the automotive sector. In particular, Kingfa sites its mix of organosheets with UD tapes as local reinforcements as a potential future solution for recyclable, affordable lightweight construction.
Related Content
-
Thermoset-thermoplastic joining, natural fibers enable sustainability-focused brake cover
Award-winning motorcycle brake disc cover showcases potential for KTM Technologies’ Conexus joining technology and flax fiber composites.
-
ASCEND program update: Designing next-gen, high-rate auto and aerospace composites
GKN Aerospace, McLaren Automotive and U.K.-based partners share goals and progress aiming at high-rate, Industry 4.0-enabled, sustainable materials and processes.
-
Cryo-compressed hydrogen, the best solution for storage and refueling stations?
Cryomotive’s CRYOGAS solution claims the highest storage density, lowest refueling cost and widest operating range without H2 losses while using one-fifth the carbon fiber required in compressed gas tanks.