Porsche races to the future with electric motors, natural fiber composites
The Mission R concept is Porsche’s vision for sustainable, all-electric customer motorsports, including a CFRP exoskeleton and natural fiber-reinforced components.
Share
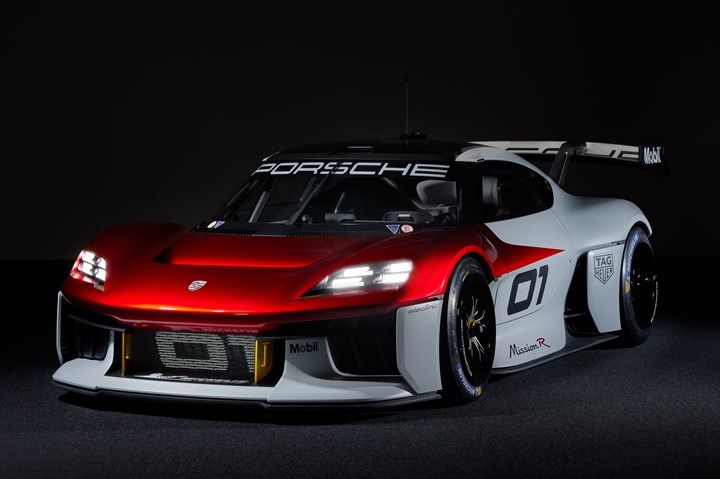
The Porsche Mission R concept: An environmentally appropriate race car. The exterior panels are based on flax fiber-reinforced plastics. And the electric vehicle has a top speed of more than 186 mph. Photo Credit, all images: Porsche
Motor racing isn’t exactly the most environmental of activities, given that there are cars and trucks speeding along tracks burning fuel in abundance. As automotive OEMs work to burnish their “green” credentials, the justification of motorsports becomes more difficult.
That is, unless the “motor” isn’t a 2.4-liter direct-injection twin-turbo V6 but electric motors like the Porsche Mission R, which has a 320 kilowatt (kW) motor on the front axle and the 480 kW motor on the rear axle and can go from 0 to 62 miles per hour in 2.5 seconds).
The Mission R is a concept. For now.
When introducing the car at the IAA MOBILITY show in Munich, Germany, Chairman of the Executive Board of Porsche AG Oliver Blume said, “The concept study is our vision of all-electric customer motorsports. The Mission R embodies everything that makes Porsche strong: performance, design and sustainability.”
Michael Mauer, head of Style Porsche, added, “the car is packed to the gills with signs that hint of a future production model, and that, of course, means pure racing!”
But it isn’t just about being an electric car. Porsche plans to be carbon-neutral by 2030, so the Mission E execution is part of its decarbonization approach.
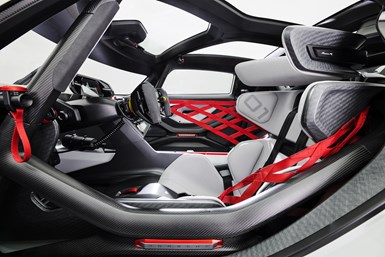
You can see part of the carbon fiber “exoskeleton,” the cage that is the primary structure of the vehicle. The seat shell is produced with natural fiber-reinforced plastic.
To reduce mass while ensuring driver safety, Porsche engineers developed what they call an “exoskeleton,” a carbon fiber-reinforced plastic (CFRP) cage structure. There are six polycarbonate segments around the CFRP cage so that it can be viewed from the exterior and that provide greater visibility for the driver.
A real green play is the use of natural fiber-reinforced plastic (NFRP) for the doors, front and rear wings, sills, side panels and center section. Beyond the exterior, the NFRP is also being used to produce the seat shell.
The fibers being used are flax, which is obtained through a collaboration between the automaker, Federal Ministry of Food and Agriculture (BMEL), the Fraunhofer Institute for Wood Research (Fraunhofer WKI) and material supplier Bcomp (Fribourg, Switzerland). According to Porsche, while the flax is obtained through farming, there is no “conflict with the cultivation of food crops.”
Further, one of the benefits for the ecological checklist is that the production of the fibers occurs with 85% less CO2 than is the case when producing carbon fibers.
Even the tires of Mission R, which were specifically developed for the vehicle by Michelin (Clermont-Ferrand, France), are made entirely with bio-based and renewable materials.
Michael Steiner, member of the Executive Board for Research and Development at Porsche AG notes, “Motorsports of the future will be more electric, more digital and more connected. And it must become more sustainable.”
Yes, they’re going to build it — or something much like it — sooner or later. How could they not?
Related Content
ASCEND program update: Designing next-gen, high-rate auto and aerospace composites
GKN Aerospace, McLaren Automotive and U.K.-based partners share goals and progress aiming at high-rate, Industry 4.0-enabled, sustainable materials and processes.
Read MoreInfinite Composites: Type V tanks for space, hydrogen, automotive and more
After a decade of proving its linerless, weight-saving composite tanks with NASA and more than 30 aerospace companies, this CryoSphere pioneer is scaling for growth in commercial space and sustainable transportation on Earth.
Read MoreWelding is not bonding
Discussion of the issues in our understanding of thermoplastic composite welded structures and certification of the latest materials and welding technologies for future airframes.
Read MoreBio-based acrylonitrile for carbon fiber manufacture
The quest for a sustainable source of acrylonitrile for carbon fiber manufacture has made the leap from the lab to the market.
Read MoreRead Next
Plant tour: Daher Shap’in TechCenter and composites production plant, Saint-Aignan-de-Grandlieu, France
Co-located R&D and production advance OOA thermosets, thermoplastics, welding, recycling and digital technologies for faster processing and certification of lighter, more sustainable composites.
Read MoreVIDEO: High-volume processing for fiberglass components
Cannon Ergos, a company specializing in high-ton presses and equipment for composites fabrication and plastics processing, displayed automotive and industrial components at CAMX 2024.
Read MoreAll-recycled, needle-punched nonwoven CFRP slashes carbon footprint of Formula 2 seat
Dallara and Tenowo collaborate to produce a race-ready Formula 2 seat using recycled carbon fiber, reducing CO2 emissions by 97.5% compared to virgin materials.
Read More