Regent appoints composites builder for seaglider demonstrator
The seaglider technology demonstrator will be able to float, foil or fly along coastal routes with the help of its composite superstructure developed by Moore Brothers Company.
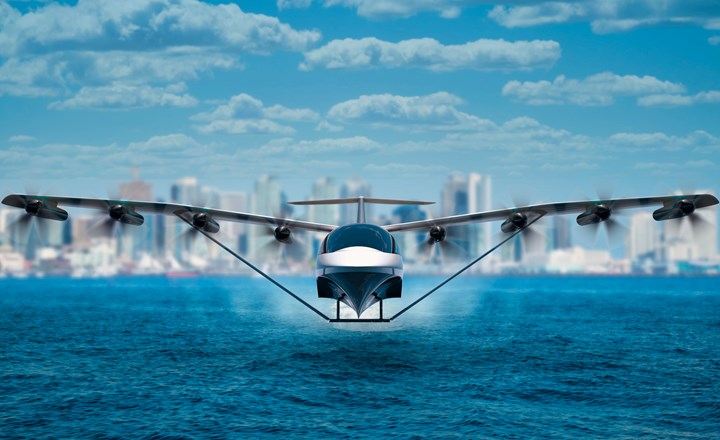
Regent’s seaglider vehicle demonstrator. Photo Credit, all images: Regent
Regent (Boston, Mass., U.S.) has announced that it will be building its composites-intensive seaglider technology demonstrator in collaboration with the Moore Brothers Co. (Bristol, R.I., U.S.), a composite manufacturing, research and development firm. Specifically, the Moore Brothers will be the main partner in creating the necessary components for the prototype’s 65-foot carbon fiber composite wing and hull. Regent, a venture-backed aerospace company, develops and manufactures all-electric, passenger-carrying, wing-in-ground-effect vehicles to service coastal routes. The company plans to test its technology demonstrator in the coming months ahead of the vehicle entering commercial service by 2025.
“Regent’s seaglider technology demonstrator could not come together without the expertise of Moore Brothers. They are not built in isolation, but built on the backs of strong partnerships. As we continue to grow and move towards our 2025 commercial service goal, we look forward to partnering with even more incredible firms. We couldn’t image a better partner to kick off our technology demonstrator composite work than Moore Brothers,” says Billy Thalheimer, CEO of Regent. “Our technology demonstrator is built to fully perform end-to-end capabilities of float, foil and fly. We are excited to announce more details of the technology demonstrator vehicle in the coming months.”
The Moore Brothers team brings extensive composite structure manufacturing experience in both the marine and aerospace industries. The company is said to specialize in using cutting-edge materials and innovative construction techniques to create strong, lightweight and high-performance components. Regarding the seaglider demonstrator, the company can confirm that the entire vehicle superstructure is autoclave-cured prepreg with a mix of Nomex and foam core materials. The combination of processes and material systems for the passenger-carrying vehicle version is still yet to be determined.
“Moore Brothers has thoroughly enjoyed working with Regent in the development of their technology demonstrator seaglider,” notes Oliver Moore, director at Moore Brothers. “Our engineering and production processes pair seamlessly with the Regent approach, as we both believe quality, safety and on-time delivery are key to success. We look forward to continuing to collaborate to bring more seagliders to market in the coming years.”
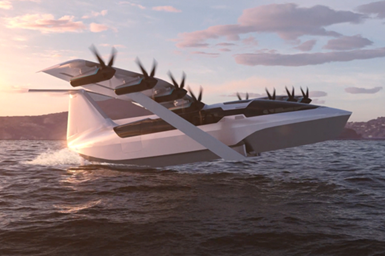
The seaglider can either float, foil or fly.
The Regent seaglider is an all-electric flying vessel that is reported to combine the speed, comfort and navigation systems of an aircraft with the convenience, maneuverability and affordability of a boat. Regulated and certified by maritime authorities, the seaglider will transport commercial passengers and critical cargo up to 180 miles at nearly 180 miles per hour with existing battery technology.
Leveraging existing dock infrastructure, Regent’s commercial seaglider will float, foil or fly. From the dock and while in the no-wake zone, the vehicle will float on its hull. Upon reaching 20 miles per hour, it will rise up on its retractable hydrofoil. By the time it reaches open water, the vehicle will smoothly transition onto its wing, retracts the foil and accelerates to a comfortable 180-mile-per-hour cruise speed, all while staying within a wingspan of the water’s surface. Flight safety at these altitudes is achieved using a multiple-redundant, state-of-the-art navigation and control system, Regent says. Similar to a hovercraft, seagliders fly on a dynamic air cushion created by the pressurized air between the wings and the water. The aerodynamic advantage of this so-called “ground effect,” includes significant operational efficiencies, increased payload capability and greater range.
Related Content
ASCEND program update: Designing next-gen, high-rate auto and aerospace composites
GKN Aerospace, McLaren Automotive and U.K.-based partners share goals and progress aiming at high-rate, Industry 4.0-enabled, sustainable materials and processes.
Read MoreThe lessons behind OceanGate
Carbon fiber composites faced much criticism in the wake of the OceanGate submersible accident. CW’s publisher Jeff Sloan explains that it’s not that simple.
Read MoreCryo-compressed hydrogen, the best solution for storage and refueling stations?
Cryomotive’s CRYOGAS solution claims the highest storage density, lowest refueling cost and widest operating range without H2 losses while using one-fifth the carbon fiber required in compressed gas tanks.
Read MoreThe potential for thermoplastic composite nacelles
Collins Aerospace draws on global team, decades of experience to demonstrate large, curved AFP and welded structures for the next generation of aircraft.
Read MoreRead Next
“Structured air” TPS safeguards composite structures
Powered by an 85% air/15% pure polyimide aerogel, Blueshift’s novel material system protects structures during transient thermal events from -200°C to beyond 2400°C for rockets, battery boxes and more.
Read MorePlant tour: Daher Shap’in TechCenter and composites production plant, Saint-Aignan-de-Grandlieu, France
Co-located R&D and production advance OOA thermosets, thermoplastics, welding, recycling and digital technologies for faster processing and certification of lighter, more sustainable composites.
Read MoreDeveloping bonded composite repair for ships, offshore units
Bureau Veritas and industry partners issue guidelines and pave the way for certification via StrengthBond Offshore project.
Read More