Rock West Composites expands filament winding facility
Rock West Composites expands its operation with the acquisition of new winders and ovens, establishes filament winding center of excellence.
Share
Read Next

Source | Rock West Composites
Rock West Composites (RWC, Salt Lake City, Utah) recently celebrated the full operational capacity of its new, dedicated filament winding facility. The company expanded into a third manufacturing bay at its Salt Lake City facility, adding 20,000 square feet of space for staff and new equipment. As the company’s capability in the filament winding arena has grown, the need to consolidate equipment and expertise in a centralized location became essential in fulfilling customer demand for this product.
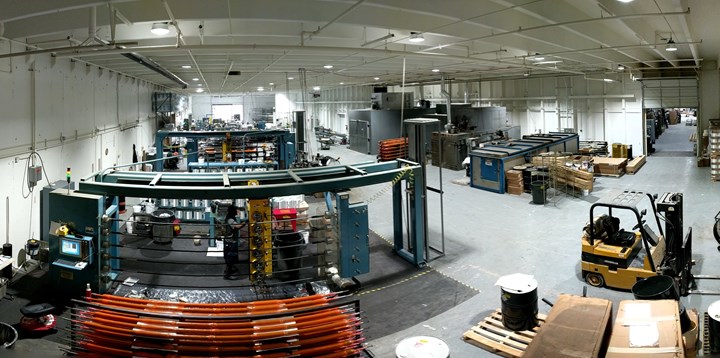
Rock West Composites has expanded its operation with the acquisition of new winders and ovens, and has added 20,000 square feet of space to establish a filament winding center of excellence in a dedicated manufacturing facility. Source | Rock West Composites
RWC has aligned several multi-spindle, wet winding and towpreg, and small to large diameter winders. Capability includes manufacturing tubes in a wide variety of dimensions up to 315 inches long and 30 inches in diameter. The company has also deployed a custom resin mixing and dispensing system for precise resin mix ratios to assure mixing accuracy and consistency. Several ovens to accommodate the increased tube production, a new extended length hydraulic mandrel extractor, and mandrel storage are all closely located within the cell to improve efficiency.
“RWC has extensive experience working with carbon fiber and glass fiber materials. The expansion of our filament winding operation is a natural extension of the work we have been engaged in for years,” says Dave Erickson, general manager of Rock West Composites’ Utah operation. “We are always seeking ways to increase efficiency, reduce cost, improve product quality, and shorten schedule. This center of excellence will enable us to deliver on our promise to make our customers more competitive.”
Related Content
-
Running shoe insoles get a lift with thermoplastic fiberglass tapes
FlexSpring insoles take advantage of unidirectional, continuous fiberglass and thermoplastics to enable next-level performance for the everyday runner.
-
CirculinQ: Glass fiber, recycled plastic turn paving into climate solutions
Durable, modular paving system from recycled composite filters, collects, infiltrates stormwater to reduce flooding and recharge local aquifers.
-
Jeep all-composite roof receivers achieve steel performance at low mass
Ultrashort carbon fiber/PPA replaces steel on rooftop brackets to hold Jeep soft tops, hardtops.