Scheurer Swiss commissions composite geo-alarm system to detect natural disasters
Carbon fiber-reinforced 3D printed inserts with glass fiber insulation are bonded to carbon tubes with fast-cure epoxy. The alarm system itself is mounted in areas like rock crevices to detect vibration and movement.
Share
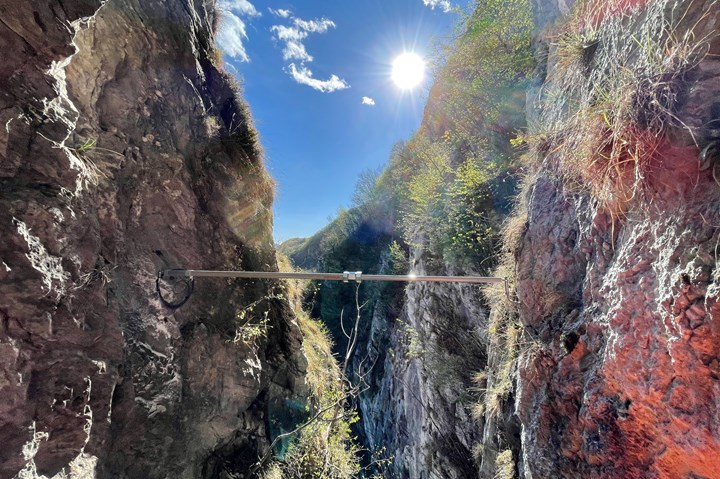
The AarteLink geo-sensor is mounted between two rock crevices to detect vibration and movement. Photo Credit, all images: Scheurer Swiss
Swiss sensor and digitalization professional Aartesys AG (Biel) has commissioned Scheurer Swiss GmbH (Volketswil, Switzerland), a company with more thirty years of experience in lightweight construction for Formula 1, and an unnamed company specializing in the production of round profiles made from carbon and glass fiber, to design and manufacture custom carbon fiber-reinforced thread inserts for its geo-sensor system, AarteLink. The alarm is used for monitoring and alerting individuals early in the event of natural hazards such as rockfalls, avalanches, landslides and floods, all of which are major threats in Switzerland. In particular, the geo-sensor was to be used for Aartesys’ latest protection project on Monte San Salvatore.
Scheurer Swiss notes that when natural hazard events occur, action must be taken quickly. It was of utmost importance then, to develop a geo-sensor system that immediately detects and accurately measures vibrations and movements in all directions, independent of vegetation and weather conditions, while also being simple to install — even in hard-to-reach areas, such as rock crevices. Further, the need for something small, lightweight and easily transportable, yet stable against high-temperature fluctuations common in mountainous regions, and highly precise were central to the solution. Carbon fiber helped meet all of these requirements.
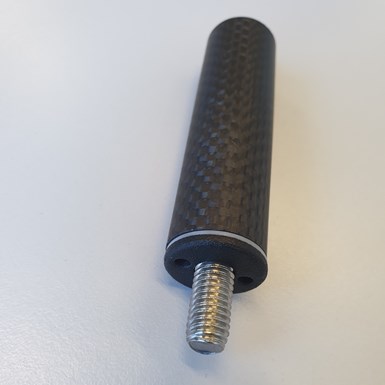
Carbon fiber 3D-printed thread inserts.
The low-maintenance, robust geo-alarm system combines sensor technology, sophisticated electronics and telecommunications technology, according to Scheurer Swiss. The unnamed company supplied the carbon tubes for crack monitoring, which immediately record and precisely measure vibrations as well as changes at critical rock crevices. Scheurer Swiss is responsible for the carbon fiber-reinforced threaded inserts with glass fiber insulation, and an injection bonding system based on fast-curing epoxy, with which the threaded inserts can be fixed in the carbon tubes on both sides within a few minutes and mounted on the rock at a height of several hundred meters.
Further, to manufacture the threaded inserts, Scheurer Swiss incorporated additive manufacturing (AM). “Carbon fiber-reinforced 3D printing meets all the criteria of producing one-of-a-kind items like these custom threaded inserts, which need to be lightweight yet strong, and as cost effective as possible to produce when needed” says Dominik Scheurer, fiber composite and lightweight construction expert at Scheurer Swiss GmbH.
For the present Aartesys project on Monte San Salvatore in Ticino, Switzerland, the supplied carbon tubes are cut to the required length at Scheurer Swiss and fitted with the carbon fiber-reinforced thread inserts before being installed in the rock faces. If required, the carbon measuring tubes can also be cut to length and bonded directly on site. For this purpose, Scheurer Swiss has designed a customized hand tool — a sageblade which serves to help cap the carbon tubes — and prepared a manual tool for professional cutting and gluing.
“With the help of the specially developed and fast-curing injection adhesive, the fitters succeed in gluing the carbon fiber-reinforced threaded inserts into the carbon tubes, which were previously cut to length by hand, even at dizzying heights,” adds Scheurer, engineer and owner of Scheurer Swiss GmbH.
To ensure the final product met all criteria, Aartesys also subjected the stability of the thread inserts and the resistance of the bonding mechanism to a rigorous mechanical stress test. Martin von Känel, CEO of Aartesys AG, notes his satisfaction: “The thread inserts with the epoxy bonding system prove their high reliability and easily withstand a tensile test of up to 400 kilograms. The positive result of our load test clearly shows the expert choice of materials and testifies to successful Swiss engineering.”
Related Content
TU Munich develops cuboidal conformable tanks using carbon fiber composites for increased hydrogen storage
Flat tank enabling standard platform for BEV and FCEV uses thermoplastic and thermoset composites, overwrapped skeleton design in pursuit of 25% more H2 storage.
Read MorePEEK vs. PEKK vs. PAEK and continuous compression molding
Suppliers of thermoplastics and carbon fiber chime in regarding PEEK vs. PEKK, and now PAEK, as well as in-situ consolidation — the supply chain for thermoplastic tape composites continues to evolve.
Read MoreThe lessons behind OceanGate
Carbon fiber composites faced much criticism in the wake of the OceanGate submersible accident. CW’s publisher Jeff Sloan explains that it’s not that simple.
Read MoreCombining multifunctional thermoplastic composites, additive manufacturing for next-gen airframe structures
The DOMMINIO project combines AFP with 3D printed gyroid cores, embedded SHM sensors and smart materials for induction-driven disassembly of parts at end of life.
Read MoreRead Next
All-recycled, needle-punched nonwoven CFRP slashes carbon footprint of Formula 2 seat
Dallara and Tenowo collaborate to produce a race-ready Formula 2 seat using recycled carbon fiber, reducing CO2 emissions by 97.5% compared to virgin materials.
Read MoreVIDEO: High-volume processing for fiberglass components
Cannon Ergos, a company specializing in high-ton presses and equipment for composites fabrication and plastics processing, displayed automotive and industrial components at CAMX 2024.
Read MorePlant tour: Daher Shap’in TechCenter and composites production plant, Saint-Aignan-de-Grandlieu, France
Co-located R&D and production advance OOA thermosets, thermoplastics, welding, recycling and digital technologies for faster processing and certification of lighter, more sustainable composites.
Read More