Solvay-NIAR Manufacturing Innovation Center opens
Partnership is dedicated to enabling increased efficiencies and performance in aviation through advances in composites technologies.
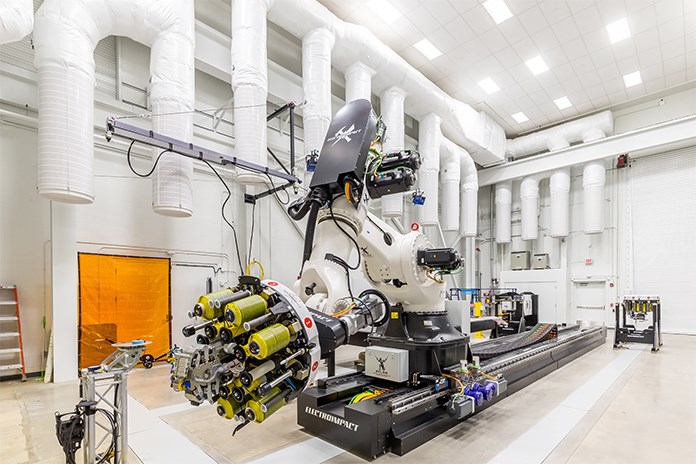
Photo Credit: Solvay, NIAR
On Oct. 5, Solvay (Alpharetta, Ga., U.S.), a global advanced materials company for aerospace, and Wichita State University’s (WSU, Kan., U.S.) National Institute for Aviation Research (NIAR) celebrates the official opening of a joint Manufacturing Innovation Center dedicated to enabling the future of flight through advances in composites technologies. The center is located within NIAR’s Advanced Technologies Lab for Aerospace Systems (ATLAS).
“Our partnership with NIAR through this joint Manufacturing Innovation Center is an important milestone in Solvay’s ambition to help key customers across the U.S. advance the future of aerospace and defense,” Carmelo Lo Faro, president of Solvay’s Materials Segment, says. “Here, we can explore the advantages of new composite material forms with the latest manufacturing technologies to create a lighter, safer and more sustainable aircraft of the future.”
At the Manufacturing Innovation Center, the country’s aviation companies will have access to 150,000 square feet of ITAR (International Traffic in Arms Regulations) compliant development, testing and prototyping facilities as well as the latest in advanced aviation material research.
According to the partners, companies will be able to fabricate entire aircraft structures such as wings and fuselages at a fraction of the cost of making it themselves. Using automated and high-rate processing with smart and agile manufacturing technologies, Solvay and NIAR engineers will work hand-in-hand with customers across the aerospace, defense, space and advanced air mobility (AAM) markets to test ideas and innovative structures in real time. These capabilities are said to help increase the adoption of composites, and enable aviation companies to meet increased performance and efficiency targets.
“ATLAS is the future of aviation manufacturing, and we’re proud to provide a proving ground for some of the world’s most advanced aviation technologies and companies,” John Tomblin, WSU senior vice president for Industry and Defense Programs and NIAR executive director, adds. “Having Solvay’s material expertise on site at this one-of-a-kind facility is a major asset for companies looking to explore what’s possible for future aircraft.”
Related Content
-
Plant tour: Middle River Aerostructure Systems, Baltimore, Md., U.S.
The historic Martin Aircraft factory is advancing digitized automation for more sustainable production of composite aerostructures.
-
Welding is not bonding
Discussion of the issues in our understanding of thermoplastic composite welded structures and certification of the latest materials and welding technologies for future airframes.
-
Composites manufacturing for general aviation aircraft
General aviation, certified and experimental, has increasingly embraced composites over the decades, a path further driven by leveraged innovation in materials and processes and the evolving AAM market.