Teledyne CML Composites invests in thermoplastic processing capability
In conjunction with the NCC, the automated processing cell supports high-performance thermoplastic and compression-molded thermoset parts production for the commercial aerospace and defense markets.
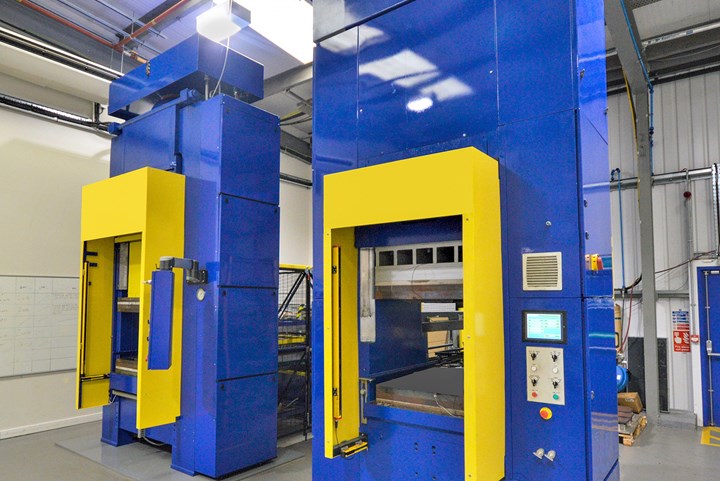
Photo Credit: Business Wire
Advanced composites manufacturer Teledyne CML Composites (Wirral, U.K.) reports that it has has completed a significant investment in a new thermoplastic processing cell developed in conjunction with the National Composites Centre (NCC, Bristol, U.K.).
The processing cell uses two press and oven systems offering infrarer (IR) heating, platen heating and a maximum force of 400 tons. The processing cell is capable of processing multiple aerospace, high-performance-reinforced thermoplastics such as PEEK, PEKK, PPS and PEI.
Further, Teledyne CML Composites says the cell significantly increases capacity in order to support the continued growth of the commercial and defense aerospace composites manufacturer.
“Having identified thermoplastics as a key technology in our long-term growth ambitions, this investment adds an exciting new automated manufacturing capability to our business and places Teledyne CML Composites at the forefront of composites manufacturing technology,” says John Toner, vice president and general manager, Teledyne Aerospace and Defence Electronics UK (TADE UK), and general manager of Teledyne CML Composites.
Not just limited to thermoplastic composites, the new processing cell also gives Teledyne CML Composites the ability to produce compression-molded thermoset parts. This new capability also enables out of autoclave (OOA) production of foam and honeycomb sandwich panels such as those used in aircraft interiors.
“The NCC is pleased to have worked with Teledyne CML Composites on setting up this new capability, which is a real step change in the manufacture of aerospace thermoplastic composites in the U.K.,” notes Sean Cooper, chief engineer for Defence and Space at the NCC. “With manufacturing cycle times measured in minutes rather than hours, thermoplastic composites have great potential for higher rate processing in aerospace applications. They have the ability to be welded together for rapid assembly and are considered more sustainable than thermosets due to increased recovery options at the end of product lifetime.”
Teledyne CML Composites says it continues to enjoy a period of significant growth as a composites manufacturer to commercial aerospace and defense aerospace customers worldwide. For decades, this industry sector has continually expanded as designers develop enhancements to performance, range and payload through weight reduction of new generations of aircraft, whether commercial or military. Teledyne CML Composites’ investment in thermoplastic processing technology underscores the company’s long-term plans to play a key part in this industry sector.
Related Content
-
Cryo-compressed hydrogen, the best solution for storage and refueling stations?
Cryomotive’s CRYOGAS solution claims the highest storage density, lowest refueling cost and widest operating range without H2 losses while using one-fifth the carbon fiber required in compressed gas tanks.
-
A new era for ceramic matrix composites
CMC is expanding, with new fiber production in Europe, faster processes and higher temperature materials enabling applications for industry, hypersonics and New Space.
-
Composites manufacturing for general aviation aircraft
General aviation, certified and experimental, has increasingly embraced composites over the decades, a path further driven by leveraged innovation in materials and processes and the evolving AAM market.