ULA selected for Dream Chaser launches
The composites-intensive Dream Chaser will launch aboard ULA’s Vulcan Centaur rockets for cargo resupply and return services to the International Space Station, starting in 2021.
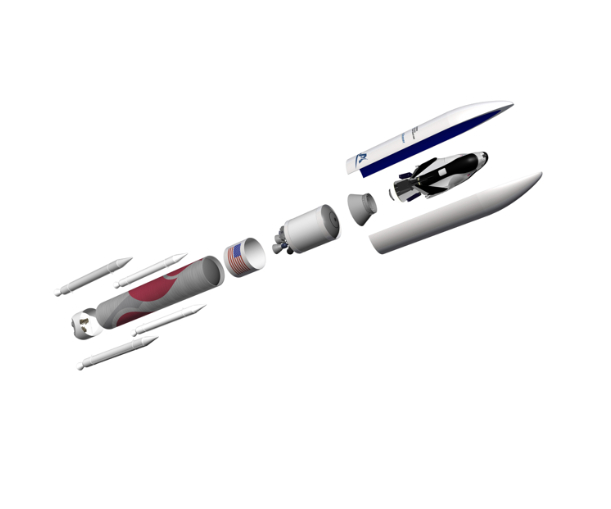
SNC Dream Chaser on ULA Vulcan Centaur rocket. Source | Sierra Nevada Corp.
Sierra Nevada Corp. (SNC, Sparks, Nev., U.S.) has announced that it has selected United Launch Alliance (ULA, Centennial, Colo., U.S.) as the launch vehicle provider for six future NASA missions involving its Dream Chaser spacecraft. The Dream Chaser will launch aboard ULA’s Vulcan Centaur rockets for cargo resupply and return services to the International Space Station, starting in 2021.
Owned and operated by SNC, the composites-intensive Dream Chaser spacecraft is a reusable, multi-mission space utility vehicle. It is capable of transportation services to and from low-Earth orbit and is the only commercial, lifting-body vehicle capable of a runway landing.
“SNC selected ULA because of our strong collaboration on the Dream Chaser program, their proven safety record and on-time performance,” says SNC CEO Fatih Ozmen. “This is bringing America’s spaceplane and America’s rocket together for best-of-breed innovation and exploration.”
Under NASA’s Commercial Resupply Services 2 (CRS-2) contract, the Dream Chaser will deliver more than 12,000 pounds of pressurized and unpressurized cargo to the space station and will remain attached for up to 75 days as an orbiting laboratory.
“This is one of the first contracts for our new Vulcan Centaur rocket, and the first of the six missions will serve as the rocket’s second certification flight,” says Tory Bruno, ULA president and CEO.
Vulcan Centaur is a new class of space launch vehicle with the performance of a heavy launch vehicle in just a single core. Approximately 90% of all of Vulcan Centaur components will be flown first on Atlas V missions in order to gain flight heritage before the next-generation launcher debuts.
Related Content
-
Welding is not bonding
Discussion of the issues in our understanding of thermoplastic composite welded structures and certification of the latest materials and welding technologies for future airframes.
-
Plant tour: Albany Engineered Composites, Rochester, N.H., U.S.
Efficient, high-quality, well-controlled composites manufacturing at volume is the mantra for this 3D weaving specialist.
-
Plant tour: Joby Aviation, Marina, Calif., U.S.
As the advanced air mobility market begins to take shape, market leader Joby Aviation works to industrialize composites manufacturing for its first-generation, composites-intensive, all-electric air taxi.