Keyland Polymer, polySpectra combine photopolymers, powder coatings to advance 3D printing
UVMax powder coatings provide a spectrum of surface color and texture possibilities, while COR Alpha photopolymers have been refined for durability.
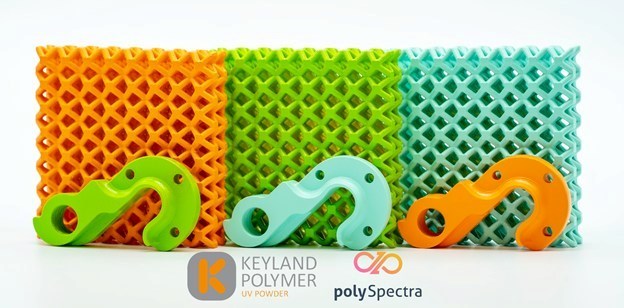
COR Alpha 3D-printed parts using UVMax powder coatings. Photo Credit: Keyland Polymers, polySpectra
Keyland Polymer (Cleveland, Ohio, U.S.) and polySpectra (Berkeley, Calif., U.S.), a producer of functional photopolymer resins for additive manufacturing (AM), have formed a strategic partnership to provide UVMax powder coatings — targeted at a composites fabrication environment — to COR Alpha 3D-printed parts. COR Alpha is a photopolymer that is rugged under pressure and stands up to solvents. This collaboration is said to unlock a new modular approach to AM, enabling the direct digital fabrication of end-use polymer components for a wide variety of applications.
According to both companies, the surface color and texture of the UVMax coating can be tailored to make COR Alpha 3D-printed parts indistinguishable from traditionally manufactured polymer products. COR engineering-grade photopolymers have been refined to offer best-in-class thermomechanical performance and durability, whether for consumer products, to medical devices to satellite parts. COR Alpha’s high thermal stability of COR Alpha also enables thorough and complete coating without the concern of warping or degrading the material.
Alternately, UVMax coating provides a spectrum of color possibilities, providing an excellent finish for lightweighting applications, transportation, building materials, consumer and industrial products. Keyland says it can develop a wide range of powders to match any supplied color standard. UV powder is an environmentally friendly coating, containing no solvents, VOCs or HAPs. It is safe to use and can be reclaimed and recycled.
Related Content
-
Large-format 3D printing enables toolless, rapid production for AUVs
Dive Technologies started by 3D printing prototypes of its composite autonomous underwater vehicles, but AM became the solution for customizable, toolless production.
-
TU Munich develops cuboidal conformable tanks using carbon fiber composites for increased hydrogen storage
Flat tank enabling standard platform for BEV and FCEV uses thermoplastic and thermoset composites, overwrapped skeleton design in pursuit of 25% more H2 storage.
-
Plant tour: Albany Engineered Composites, Rochester, N.H., U.S.
Efficient, high-quality, well-controlled composites manufacturing at volume is the mantra for this 3D weaving specialist.