L&L Products launches thermoplastic resin product line
T-Link, from L&L Products, is a thermoplastic resin available in pellet, film, yarn, powder, fiber veil and unidirectional tape formats, targeted toward armor, aerospace and sporting goods applications.
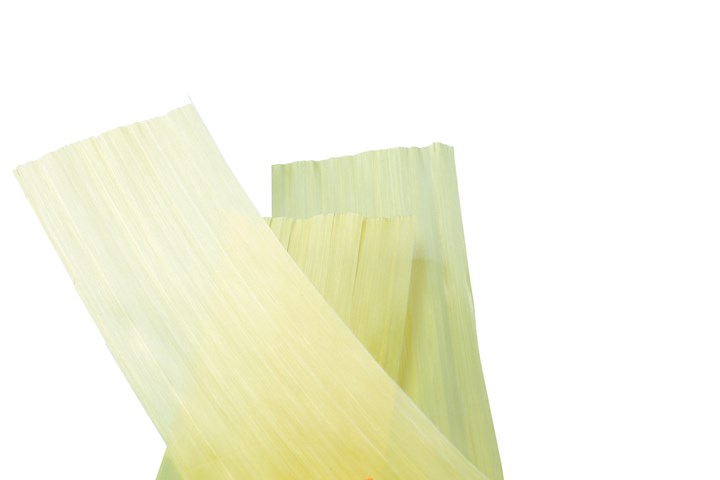
L&L Products T-Link thermoplastic tapes. Photo Credit: L&L Products
L&L Products (Romeo, Mich., U.S.) has launched a new technology line, called T-Link, an advanced engineering thermoplastic resin with reportedly excellent adhesive properties. L&L says the vision driving T-Link was to enable customers to benefit from the adhesion properties of the resin along with the recyclability, repairability and formability of an engineering thermoplastic. The reported result is reduction of process cycle times for high-performing, lighter-weight applications.
Due to its thermoplastic nature, T-Link is said to conform to deep-drawn parts allowing for production of irregularly shaped components. Depending on application needs, L&L offers T-Link in pellet, film, yarn, powder, fiber veil and unidirectional tape formats. The film format of T-Link has been on the market since 2014 and has been applied as a matrix resin solution for several composite applications in the aerospace, armor, and sporting goods industries.
Armor, in particular, is a prime target for T-Link, L&L says. It can be co-processed with ballistic materials such as glass, para-aramids and UHMW-PE to increase performance and rigidity.

“Composite armor manufacturing has been more art and less science when relating to repeatable, close tolerance parts with precise performance. T-Link allows for these improvements because of its range of product solutions such as film, coated yarn, multifilament and monofilament formats. This novel technology will allow for easier material integration, process automation, reduced production cost, and expanded design capabilities,” says Scott Stover, vice president of business development at D H Sutherland (Beaverton, Ore., U.S.), L&L’s distribution partner.
L&L points out that T-Link does not require refrigeration and can help reduce layup and processing time. Further, the resin is transparent, pigmentable and recyclable. It also can be co-molded with dissimilar materials. L&L says composites developed with T-Link deliver a precise coat weight with consistent quality control over the resin content.
Related Content
-
TU Munich develops cuboidal conformable tanks using carbon fiber composites for increased hydrogen storage
Flat tank enabling standard platform for BEV and FCEV uses thermoplastic and thermoset composites, overwrapped skeleton design in pursuit of 25% more H2 storage.
-
The potential for thermoplastic composite nacelles
Collins Aerospace draws on global team, decades of experience to demonstrate large, curved AFP and welded structures for the next generation of aircraft.
-
Plant tour: Albany Engineered Composites, Rochester, N.H., U.S.
Efficient, high-quality, well-controlled composites manufacturing at volume is the mantra for this 3D weaving specialist.