Rock West Composites expands space-grade Strato product line
Rock West Composites is expanding its space-grade Strato product line, including products appropriate for geosynchronous equatorial orbit and deep space applications.
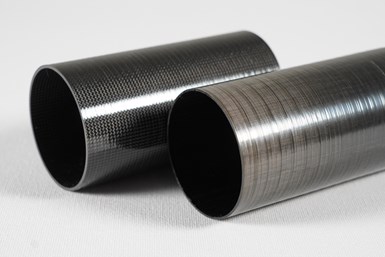
Tubes from the Strato product lineup. Photo Credit: Rock West Composites
Rock West Composites (RWC, San Diego, Calif., U.S.) is expanding its Strato space-grade product line. Originally focused on tubes for lower Earth orbit (LEO) applications, a secondary line includes products appropriate for geosynchronous equatorial orbit (GEO) and deep space use. With this addition, the Strato product portfolio includes plates, sandwich panels and solar array substrates for both orbital types.
The Strato line is designed to provide businesses and government agencies high-quality components commonly needed for spacecraft. RWC says it offers shorter lead times than other providers. These lead times — approximately two to four weeks — are made possible because the company stocks raw materials, such as M55J/PMT-F33 Cyanate Ester and HR40/NB321 epoxy for its ecommerce business. Orders can be placed online.
The entire Strato line is said to meet key requirements for space, with properties that include low outgassing, low to zero coefficient of thermal expansion (CTE), high modulus materials and a wide operational temperature range.
The StratoLeo class is a more cost competitive option for meeting space requirements without the additional high-performance capability typically associated with GEO orbits and deep space flights, according to the company. For cases where performance can’t be compromised, RWC points to the StratoGeo class which is said to use top-of-the-line materials. Additional details about some of the differences between the product classes is available on RWC’s website.
Each order includes a certificate package with dimensional inspection, material certificates, traceability and a certificate of conformance from RWC. All products are serialized and traceable. Additional options for some products include full traveler verification, resin content testing, and short beam shear testing.
“Our goal is to make space quality hardware readily available in a cost effective and efficient manner,” says Jeremy Senne, head of RWC’s space market segment. “Whether it’s a start-up business building cube sats or large prime contractors looking to optimize operations, agile organizations in a rapidly growing industry need high quality solutions quickly. Our hope is to help minimize design and build timelines by standardizing available products.”
Related Content
-
Plant tour: Spirit AeroSystems, Belfast, Northern Ireland, U.K.
Purpose-built facility employs resin transfer infusion (RTI) and assembly technology to manufacture today’s composite A220 wings, and prepares for future new programs and production ramp-ups.
-
Plant tour: Albany Engineered Composites, Rochester, N.H., U.S.
Efficient, high-quality, well-controlled composites manufacturing at volume is the mantra for this 3D weaving specialist.
-
A new era for ceramic matrix composites
CMC is expanding, with new fiber production in Europe, faster processes and higher temperature materials enabling applications for industry, hypersonics and New Space.