Composites help Bell V-280 toward Future Vertical Lift
Bell’s design for future military helicopter uses hybrid metal-composite construction and Large Cell Carbon Core technology for unitized wing.
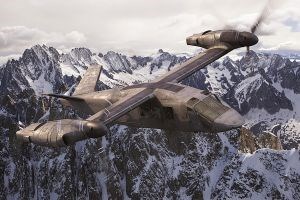
The Bell V-280 Valor is named for its 280-knot cruise speed. SOURCE: Bell Helicopter
- V-280’s top speed of 300 knots beats current “fastest military helicopter” title-holder, Eurocopter’s X3 (255 knots).
Adhesively bonded, composite wing, “made in one large piece” using Large Cell Carbon Core technology, reportedly cuts costs by over 30% vs. a V-22 wing scaled down to similar size. - Composite hub yoke machined from composite broadgoods layed up in open-face tooling reduces cost by 50% compared to using closed tooling.
- V-280 will use reported first all-carbon tiltrotor main blades, built by Eagle Technologies, LLC.
The Joint Multi-Role (JMR) Technology Demonstrator (TD) will mature technologies
and help refine requirements for the Future Vertical Lift (FVL) program.
SOURCE: Bell Helicopter V-280 Valor brochure.
Future Vertical Lift
The Future Vertical Lift (FVL) program aims to develop new, faster and more agile vertical takeoff and landing (VTOL) aircraft for all of the US armed services in four different sizes: light, medium, heavy and ultra. In consideration since 2004, FVL is a path toward replacements for the Army’s UH-60 Black Hawk, AH-64 Apache, CH-47 Chinook and OH-58 Kiowa helicopters, and the Navy’s MH-60 Seahawk. However, similar to the original aims of the F-35 Lighting II Joint Strike Fighter, the multiple platforms envisioned in the FVL family are being designed not to simply replace older helicopters – but also to take on missions that were previously impossible thanks to the expected range, speed and integration of high-tech systems.
The precursor for the FVL is the Joint Multi-Role (JMR) Technology Demonstrator (TD) phase. In June 2013, Bell Helicopter (Fort Worth, TX, US) announced that the V-280 Valor design it is co-developing with Lockheed Martin (Bethesda, MD, US) had been selected by the US Army for the JMR-TD.
280-knot Cruise
The V-280 takes its name from its 280-knot (320 mph; 520 km/h) cruise speed. Bell, which currently produces the V-22 Osprey tiltrotor aircraft for the US Marine Corps and US Air Force, describes the V-280 as a third-generation tiltrotor that incorporates lessons learned from its 55 years of designing and building such aircraft. Touted as offering twice the speed and range as current helicopters, the V-280 has a reported top speed of 300 knots (350 mph; 560 km/h), a range of 2,100 nautical miles (2,400 mi; 3,900 km) and a combat range of 500 to 800 nautical miles (580 to 920 mi; 930 to 1,480 km). It will have a crew of 4 and carry up to 14 troops.
Unlike the V-22, which is credited with completing nearly 200,000 flight hours, the V-280’s engines do not rotate. Instead, the engines remain in place while the rotors and driveshafts tilt. A driveshaft runs through the straight wing — the V-22 has a swept wing — allowing both prop rotors to be driven by a single engine in the event of engine loss.
The V-280 wing, hub and rotor blades use specific composite
materials and processes to achieve weight and cost savings.
SOURCE: Bell Helicopter presentation to Society of Experimetal Test Pilots, Oct 2014.
Weight- and Cost-cutting Composites
Another key difference is the emphasis on reducing the V-280’s weight vs. the V-22, which will in turn reduce its cost, by using carbon fiber-reinforced composites in the wing, fuselage and tail. For example, wing skins and ribs are reportedly adhesively bonded together, reducing costs by over 30% vs. a scaled V-22 wing.
The composite components are also reported to be more unitized, enabling fewer, larger and lighter parts, made possible by Large Cell Carbon Core technology which is described as stiff and lightweight carbon fiber honeycomb sandwich construction.
Bell reportedly expects the V-280 to cost roughly the same as an AH-64E or MH-60M. It will position itself opposite the Osprey — which has a higher disk loading and lower hover efficiency than a helicopter — and instead use a lower disk loading and longer wing for greater hover and cruise efficiency. Disk loading (disc loading) is calculated by dividing the total helicopter weight by its disk area, i.e., the area swept by its rotor blades. A higher disk loading means more power is needed to maintain rotor speed, whereas a lower disk loading indicates better lift thrust efficiency. In other words, the V-280 should deliver more operational efficiency without a drastically higher price tag.
Partners and Composites
The Bell V280 team has 11 investing partners including Lockheed Martin. The roles of those responsible for the primary components and composites technology are outlined below.
Bell Helicopter’s major components include the carbon-fiber composite wing, prop rotor gearbox and composite yoke for the rotor hub. The wing is reportedly produced in one large piece and is the first use of Large Cell Carbon Core composites, described by Bell’s V280 program director Keith Flail as a sandwich of carbon-fiber skins and honeycomb, achieving simplicity and light weight. He says that two test wing boxes were built to validate manufacturing processes, strength and stiffness. This construction will also reportedly allow immediate detection of damage to the wing.
The hub yoke is said to be layed up from composite broadgoods in open-face tooling and machined around the edges for a 50% cost reduction compared to using closed tooling, according to Flail. He notes that the V-280 will also use the first all-carbon tiltrotor blade for improved reliability, lower cost and greater aerodynamic performance.
Eagle Technologies produces the V-280's all-carbon rotor blades
and also built this S-97 mockup for Sikorsky in just 16 weeks starting in Dec 2008.
SOURCE: Eagle Technologies
and the Vertiflite magazine article "The Eagle Flies" by Robert Moorman.
Eagle Technologies, LLC (Newport News, VA, US) will manufacture the all-carbon fiber composite tiltrotor blades. Eagle has produced the advanced composite main rotor blades for the Sikorsky X2 and S-97 Raider helicopter prototypes and the propeller blades for the Boeing Phantom Eye high altitude long endurance (HALE) unmanned aerial system (UAS), as well as a variety of composite parts for Sikorsky, Boeing, Northrop Grumman and Lockheed Martin, among others.
GKN (Redditch, UK) is using a combination of metals and composites to produce the V-tail structure and ruddervators, which are designed to provide advanced maneuverability and control to the airframe. The first V-tail is scheduled to be mated to the fuselage in early 2016. The company also produces the CH-53K helicopter aft transition unit, a complex fuselage section comprising over 1,000 parts and measuring 6m long by 3m wide and 3m high. It features an advanced hybrid composite aluminum and titanium structure covered with external composite skins, with composites making up ≈50% of its weight.
AGC Composites and Aerostructures (Oklahoma City, OK, US) is manufacturing the over wing fairing. According to Rick Armstrong, AGC president and CEO, the fairing’s development was a collaborative effort between the company’s US facilities. These include the Hayden, Idaho site that was previously Unitech Composites (acquired by AGC in 2007), and the AGC Aerospace and Defense headquarters in Oklahoma City, Oklahoma. Owned by The Edgewater Funds and Acorn Growth Companies, AGC produces custom, weight-saving composite structures for legacy weapon systems, composite details and assemblies for aircraft currently in production, precision exotic metal assemblies for aircraft engines, and aircraft structural fusion welding (ASFW) on alloy metal parts for aftermarket spare programs. The group also has facilities in Derby, Portland and Yeovil, UK.
Spirit AeroSystems designs and builds the composite cabin and cockpit for the V-280.
Phil Anderson, senior VP of defense and contracts at Spirit AeroSystems, says the company's automated fiber placement machines deliver cost-effective, large carbon fiber parts.
SOURCE: (top) Spirit AeroSystems, (bottom) The Wichita Eagle.
Spirit AeroSystems (Wichita, KS, US) is building the V-280 composite fuselage. According to Bell V-280 program director Keith Flail, design-to-delivery of the first fuselage took Spirit just 22 months and required minimal tooling. Other high-speed enablers were determinant assembly and laser alignment. Determinant assembly involves designing components that will fit together at predetermined junctions, within tolerance, in order to eliminate manual measurements, adjustments and fixturing. Flail claims there are only three hard shims used in the whole fuselage, which he says features composite skins over metal frames. The first fuselage is now at Bell’s Amarillo, Texas facility undergoing final assembly.
The fuselage is most likely made using automated fiber placement (AFP). “I can supply the prime contractors structure,” explained Phil Anderson, Spirit’s senior VP of defense and contracts in a 2014 article by The Wichita Eagle. Standing in front of the large AFP system in Spirit’s R&D facility, he added, “This machine can deliver with a very affordable price probably better than what they can do themselves.” Formerly Spirit’s CFO, Anderson assumed his current position in 2013 and was tasked with increasing the company’s defense work. The company also builds major structural cockpit and cabin components for Sikorsky’s CH-53K helicopter fuselage using composites.
Israel Aerospace Industries (IAI, Tel Aviv, Israel) is supplying hardware which Bell is using to build the nacelles in its Amarillo plant. On the V-280, only the prop rotor gearbox rotates and the engine stays horizontal. Flail says the nacelles were a challenge because, due to design changes, they were the last to mature, yet needed to be the first released for fabrication. Bell’s press release cited IAI’s use of advanced automation technologies enabling cost reduction as key to overall V-280 team performance.
IAI is also supplying the seats, which reportedly use wireless technology to charge troops’ radios. It already supplies crashworthy seats made using advanced composites for the Bell 525 Relentless. IAI also produces such seats for fixed-wing aircraft and ground combat vehicles.
General Electric (Cincinnati, OH, US) is supplying the T64 engine for the demonstrator, which is reportedly through overhaul and acceptance testing at MCAS Cherry Point, North Carolina. The second engine and two additional spares are scheduled to be delivered by 2016.
Lord Corp. (Cary, NC, US) is supplying elastomeric bearings which are key to the increased flapping capability of the V-280’s 35-ft.-dia. prop rotors, an improvement compared to the V-22. Flail says this results in increased low-speed agility, and the light loading on the bearings in airplane mode extends their life.
Toray Composites America (TCA, Tacoma, WA, US) signed an agreement in Sep. 2015 to supply carbon fiber prepreg materials for Bell Helicopter programs. Though initial supply of materials will be used for the Bell 525 Relentless program, it is expected that the V-280 may also use TCA carbon materials.
Competitors and Progress
Though Bell produces the V-22 in partnership with Boeing, for the JMR-TD the two companies are competitors, Boeing having teamed with Sikorsky to produce the SB-1 Defiant. Of course, all of this becomes more interesting with Lockheed Martin’s acquisition of Sikorsky now complete. As Bell’s partner for the V-280, it would appear Lockheed Martin’s chances of winning the FVL are pretty good. AVX Aircraft and Karem Aircraft are also among the 4 teams awarded technology investment agreement deals by the Army, aiming toward flying technology demonstrators beginning in 2017.
The V-280 was officially unveiled at the 2013 Army Aviation Association of America's Annual Professional Forum and Exposition in Fort Worth, Texas, with a projected first flight in 2017. Bell Helicopter’s CEO John Garrison has said that his team is on schedule, and hitting its affordability and sustainability targets.
Stay tuned for a follow-up blog with more details on the Large Cell Carbon Core technology.
Related Content
Combining multifunctional thermoplastic composites, additive manufacturing for next-gen airframe structures
The DOMMINIO project combines AFP with 3D printed gyroid cores, embedded SHM sensors and smart materials for induction-driven disassembly of parts at end of life.
Read MorePEEK vs. PEKK vs. PAEK and continuous compression molding
Suppliers of thermoplastics and carbon fiber chime in regarding PEEK vs. PEKK, and now PAEK, as well as in-situ consolidation — the supply chain for thermoplastic tape composites continues to evolve.
Read MorePlant tour: Joby Aviation, Marina, Calif., U.S.
As the advanced air mobility market begins to take shape, market leader Joby Aviation works to industrialize composites manufacturing for its first-generation, composites-intensive, all-electric air taxi.
Read MoreTU Munich develops cuboidal conformable tanks using carbon fiber composites for increased hydrogen storage
Flat tank enabling standard platform for BEV and FCEV uses thermoplastic and thermoset composites, overwrapped skeleton design in pursuit of 25% more H2 storage.
Read MoreRead Next
All-recycled, needle-punched nonwoven CFRP slashes carbon footprint of Formula 2 seat
Dallara and Tenowo collaborate to produce a race-ready Formula 2 seat using recycled carbon fiber, reducing CO2 emissions by 97.5% compared to virgin materials.
Read MoreDeveloping bonded composite repair for ships, offshore units
Bureau Veritas and industry partners issue guidelines and pave the way for certification via StrengthBond Offshore project.
Read MoreVIDEO: High-volume processing for fiberglass components
Cannon Ergos, a company specializing in high-ton presses and equipment for composites fabrication and plastics processing, displayed automotive and industrial components at CAMX 2024.
Read More