JEC World 2017: Show report, part 1
JEC World 2017 was, by almost any measure, the biggest and busiest JEC event yet, and exhibitors came with much to show the world of composites about innovation in materials, equipment and technology.
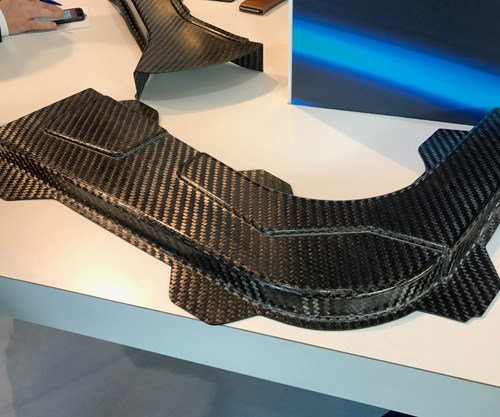
Solvay's new SolvaLite 730 thermoset prepreg resin system, developed for automotive applications, features a 60-second cycle time and 6 months outlife at room temperature.
JEC World 2017 (March 14-16, Paris, France) was, by almost any measure, the biggest and busiest JEC event yet, and exhibitors came with much to show the world of composites about innovation in materials, equipment and technology. CompositesWorld was there for all three days, and senior editors Sara Black and Ginger Gardiner, along with myself, tried to capture as much as we could about what was new, interesting and noteworthy. Below is my coverage, and you can find Sara’s and Ginger’s here:
The automotive end market, in many ways, dominated the show. Material and equipment suppliers are working hard to make it difficult for automotive OEMs to overlook the capabilities of composite materials. Faster-curing resins and optimized manufacturing processes introduced at the show are clearly designed to meet the automotive industry’s high-volume, high-repeatability needs.
Solvay Composite Materials
Solvay Composite Materials (Tempe, AZ, US) introduced SolvaLite 730, a new thermoset prepreg comprised of what the company says is novel chemistry (i.e., not based on an existing resin matrix). Designed for high-volume applications, SolvaLite 730 offers low tack, a 3-minute cure at 150°C, a 1-minute cure at 170°C, and storage stability at room temperature for up to six months. The company is targeting compression molding with this material, as reflected in the sample parts at Solvay’s booth. The resin also offers low enthalpy, a Tg of 130°C, demoldability at 170°C and a reduced total cost of ownership thanks to longer tool life, ease of storage and reduced scrap rates. Carbon fiber formats being offered initially are UD fabrics of 150 or 300 gsm, made with 5k high-strength carbon fiber. Solvay is also offering a 380-gsm 2x2 twill, made with 12k high-strength carbon fiber.
Dow Automotive
Similarly, Dow Automotive (Auburn Hills, MI, US) introduced Vorafuse Epoxy P6300, a prepreg offered in conjunction with carbon fiber supplier DowAksa (Marietta, GA, US). It is also targeted toward compression molding for automotive manufacture, offers a 2-minute cure and is room-temperature stable for up to 30 days. This material was originally developed for the Ford GT. Also on the Dow Automotive stand was an Aston Martin automotive trunk frame structure (see photos) manufactured by Faurecia via RTM using Dow’s Voraforce 5300 epoxy and chopped carbon fiber matt. Dow officials said the part has a post-injection cure time of 90 seconds.

This 700g roof for the Roding Roadster was manufactured with KraussMaffei's thermoplastic RTM process, in which caprolactam is in-mold polymerized to create PA6.
KraussMaffei
KraussMaffei (Munich, Germany) introduced its thermoplastic RTM process, in which caprolactam is in-mold polymerized to create polyamide 6 (PA6). The part on display (see photo) was a 700g Roding Roadster roof, made via injection overmolding of a GF/CF preform with a cycle time of about 4 minutes. The black and white striping on the part was intentional, to show the multi-fiber capability of the process. KrassMaffei also emphasized its FiberForm process, in which GF/PA organo sheet is injection overmolded with GF/PA. The part on display was a Daimler AG seat shell (see photo). Advancing pultrusion technology is also a goal of KraussMaffei. The company announced the launch of a new high-speed pultrusion system that features a closed mixing section and fast-reacting polyurethane and epoxy resins developed in cooperation with Huntsman, Covestro and Evonik. The machine, which can make curved pultrusions, will offer take-off speeds of 0.5 m/min, with a near-term goal of 1 m/min.

This automotive seat shell in the KraussMaffei stand was molded with the company's new FiberForm process, which combines compression molding of CF/PA organo sheet with injection overmolding, also of CF/PA. The organo sheet provides specific mechanical strength where needed.
Hexion
Hexion (Columbus, OH, US) introduced, for automotive use, an epoxy-based SMC that is said to be styrene- and VOC-free. It’s being positioned as a drop-in replacement for existing SMCs, offers low viscosity and has a cycle time of 3-5 minutes. The new offering, EPIKOTE resin TRAC 06605/EPIKURE curing agent TRAC 06608, can be used to produce lightweight semi-structural and structural automotive composite parts, such as floors, electrical vehicle battery enclosures, spare wheel tubs, seat structures, hood inners and more. The resin emits fewer volatile organic compounds (VOCs) according to VDA 278 than either standard- or low-VOC vinyl esters, with emissions reportedly well below international exposure limits. The VDA 278 recommendation governs organic emissions for molded compounds in automobiles.

This demonstrator automotive seat frame was fabricated with Hexion's new carbon fiber SMC.
Also new from Hexion is a phenolic resin with an ultra-low free formaldehyde (ULEF) content of less than 0.1%. Cellobond J2027-X01 contains one-tenth the free formaldehyde of previous systems. This results in reduced emissions during composite manufacturing, particularly during open-mold processes such as hand lay-up. Finally, Hexion reported FastRTM, a project of an industry consortium supported by IRT M2P, focused on enabling composite mass production, used a specialty epoxy resin system from Hexion in a new production platform that won the 2017 JEC Innovation Award in the Process category. FastRTM’s fully automated manufacturing platform demonstrates that reactive compression resin transfer molding (C-RTM) can be used to mass-produce net-shape structural composite parts. The FastRTM project used Hexion’s latest E-Coat-compatible fast-cure epoxy system, EPIKOTE resin TRAC 06170/EPIKURE curing agent TRAC 06170, to produce the net shape parts via the C-RTM process in a 2-minute cycle.

This Dymag carbon fiber wheel on the Huntsman stand was one of many either all-carbon fiber or hybrid carbon fiber/aluminum wheels on exhibit at JEC.
Huntsman Advanced Materials
Huntsman Advanced Materials (Switzerland) GmbH (Basel, Switzerland) announced at the show that it is releasing the results of its latest survey into the use of composites in the automotive industry, which gauges customer needs and attitudes towards lightweighting materials and technologies. Huntsman conducted in-depth interviews with more than 160 respondents, including automotive suppliers, original equipment manufacturers (OEMs) and engineers, to identify industry trends. Although the company is not yet releasing results details, the company did say that that survey showed CO2 emissions and fuel efficiency regulations are key drivers for the use of lighter weight materials, but affordability and the long-term availability of carbon fiber are stopping more manufacturers from using composites in mass production. According to respondents, fiber-reinforced composites will become more widely adopted by the premium and sports automotive sector over the next 10 years and will likely reach mainstream car segments in the longer term.
Hexcel
Hexcel (Stamford, CT, US) hosted its annual press conference on the opening morning of the show and CEO and president Nick Stanage reported 2016 sales revenue of more than US$2 billion, split among the US (42%), Europe (41%) and Asia (17%). The company’s business continues to be dominated by commercial aerospace (71%), followed by industrial (13%) and space and defense (16%). The company is coming off a US$300 million capital investment campaign and will now, says Stanage, look to rebuild more than US$100 million in cash in 2017. He says Hexcel will continue to emphasize a strategy of sole-source positioning in markets with high barriers to entry, and the company has taken minority interests in several niche companies, including Formax, Luminati, Oxford Performance Materials and Carbon Conversions.
Thierry Meriot, Hexcel’s president aerospace, Europe/Middle East/Asia, reported on the company’s carbon fiber supply chain for the Airbus A350 XWB and noted that Hexcel delivered material for 45 A350 XWB deliveries in 2016, and the company is gearing up for an aircraft build rate of 10/month by the end of 2018. He said the Hexcel material ship set value per A350 XWB is about US$5 million. In addition, he reported that Airbus and Hexcel signed a two-year contract extension for the A350 XWB and other Airbus legacy aircraft, taking the contract to 2030 and representing additional sales of US$15 billion.
On the automotive said, Tim Swords, president industrial, reported that Hexcel’s M77 carbon fiber prepreg stacks have been used to fabricate, to-date, 200,000 B-pillars for the BMW 7-Series. For wind, Hexcel emphasized its Polyspeed pultruded carbon fiber/polyurethane profiles for wind blade spar caps (see photo). In Europe, Hexcel research and development will be done primarily by the company’s new Innovation Centre in Duxford, UK, and (opening in 2018) the Innovative Manufacturing Technologies Centre in Les Avenieres, France.

Epsilon Composite’s Carboglulam pultruded spar cap laminate, 300 x 3 mm carbon fiber/epoxy, with high volumetric fiber ratio. This reel of pultruded material was one of many on exhibit by several suppliers at JEC.
Looking ahead, Stanage says Hexcel is focusing on redesign/replacement of the Boeing 737 and Airbus A320, which many aerospace industry observers estimate will be undertaken in the next five years. The question, says Stanage, is where composites will be applied on those planes. With an estimated build rate of 60 units/month, he said, the composites industry will have to do serious work on processing technologies to increase the speed of manufacture. Stanage pointed to preforming, fast-cure resins, low-viscosity resins, increased automation and high-speed ATL/AFP as key enabling technologies in this market.
SABIC
SABIC (Pittsfield, MA, US) has expanded its UDMAX product line with the addition of glass and carbon fiber-reinforced thermoplastic tapes. UDMAX GPE is a glass fiber/polyethylene combination; UDMAX CPA is a carbon fiber/polyamide combination. SABIC also featured its UDMAX GPP 45-70 (glass/polypropylene) tape in a plain-woven 0°/90° format.
RocTool
RocTool (Charlotte, NC, US) attracted much attention to demonstration of its Induction Dual Heating (IDH) automated manufacturing cell. At JEC, the cell was used to simultaneously compression mold and overmold a 14-inch-long, 1-mm-thick computer cover in 1-minute cycles. In the process, thermoplastic sheets were placed directly in the mold — without preheating — and then formed and overmolded in one step. A video of the RocTool IDH system can be viewed here above.

Boikon's thermoplastic tape placement machine features an end-effector developed by Fokker Aerostructures.
Boikon
Boikon (Leek, The Netherlands) demonstrated at the show its thermoplastic tape placement technology, which lay down SABIC’s UDMAX GPP 45-70 carbon fiber/PP tapes in a variety of shapes (see photo). The unit uses a placement head developed in cooperation with Fokker Aerostructures (Hoogeveen, The Netherlands) and provides continuous ultrasonic tacking to adhere tape layers together. Jeroen Oosterhof, director of Boikon, says stackups, after they are laid up, are typically consolidated via compression molding and offer void content of <1%.
3M Advanced Composite Resins
3M Advanced Composite Resins (St. Paul, MN, US) emphasized four of its resin systems. The 2-Series, for RTM, is an aerospace primary structure material. 3-Series is a nanosilica-reinforced prepreg for sporting goods. 4-Series, also nanosilica-reinforced, is a low-viscosity material for pressure vessels. 8-Series is a nanocalcite-reinforced material for industrial, medical and sporting goods applications. Each series is formulated from one of several base resins, including epoxy, BMI and phenolic. Dave Sewell, global business manager, said 3M is focusing exclusively on high-performance applications and is featuring use of nano-fillers to help improve mechanical properties, reduce exotherm and reduce shrinkage.

Metycore FS from Metyx a cored glass fiber for RTM of products for railway applications.
Metyx Composites
Metyx Composites (Istanbul, Turkey) introduced at JEC a new woven carbon fiber material that features a specialized coating to prevent weft and warp distortion. Polyamide or other thermoplastics are offered as the base material. Also new was Metycore FS (fire shield, see photo), a “cored” glass fiber for RTM of products for railway applications. This material is halogen-free and meets EN 45545 requirements.

Dyneema Carbon from DSM Dyneema features woven carbon and Dyneema UHMWPE fibers in various ratios to meet specific mechanical requirements in the finished product.
DSM Dyneema
DSM Dyneema (Geleen, The Netherlands) introduced Dyneema Carbon, a line of products that combine Dyneema ultrahigh molecular weight polyethylene (UHMWPE) with carbon fiber. The resulting material, says the company, significantly improves the performance of pure carbon composites in terms of weight, impact resistance, ductility and vibrational dampening. These hybrid fabrics can be customized to contain different amounts of Dyneema, which makes it possible to adjust the balance of impact strength, vibration dampening and weight. Also new was Dyneema Composite Fabrics (from the 2015 acquisition of Cubic Tech), flexible composite fabrics that the company says dramatically increase tear, puncture and abrasion performance dramatically compared with 500D nylon, while cutting weight and reducing bulk.
Virtek
Virtek (Waterloo, ON, Canada) launched at JEC its Iris 3D laser projector, featuring the company’s Vision Positioning System (VPS). VPS is a technology designed to greatly simplify mold setup for laser projection. It uses mold-mounted targets that are easily and quickly acquired by the VPS to determine mold location, even if the mold moves or drifts. Indeed, demonstrations in the Virtek stand at the show proved that the VPS can, in seconds, capture a mold location with no human intervention requirement. Virtek also announced that major components of Iris will be field-replaceable by the user, which means that customers can avoid sending units to Virtek for repair and, in the process, increase projector uptime.
Olin Epoxy
Olin Epoxy (Zug, Switzerland) launched its Lightstone epoxy resin system, designed for prepreg, pultrusion or infusion to manufacture parts for construction, transportation and pressure vessel applications. Olin officials said the material offers good fire-retardant properties, damage tolerance and toughness. The company is evaluating application of this epoxy in some aerospace parts as well.

Tuball Paper is OCSiAl's single-wall carbon nanotube sheet product.
OCSiAl Group
OCSiAl Group (Leudelange, Luxembourg) emphasized its line of single-wall carbon nanotube (SWCNT) concentrates, masterbatches and tapes. The company’s Matrix concentrates are offered with a variety of base resins, including epoxy, polyurethane, vinyl ester. Tuball Comp_E masterbatches are offered with epoxy, bis A, bis F and polyethelyne. Tuball Paper is OCSiAl’s line of SWCNTs offered in sheet format (see photo). OCSiAl says its SWCNT manufacturing capacity is 10 MT/year and the company plans to increase that to 60 MT/year by 2018.
Riba Composites
Riba Composites (Faenza, Italy) reported that it is continuing work with Fraunhofer ICT to develop an affordable carbon fiber wheel for the transportation market. Andrea Bedeschi, general manager at Riba, said the wheel is 22 inches in diameter, is designed for an SUV and has more than seven spokes (Bedeschi would not reveal the exact number). The wheel is being manufactured via HP-RTM, is comprised of carbon fiber/epoxy and should be ready for testing/validation by fall 2017. Bedeschi said one of the broader challenges of developing a carbon fiber wheel is meeting the OEM’s need for custom spoke design, while maintaining all strength and stiffness requirements.
There were, at JEC, an unusually large number of all-carbon fiber and carbon fiber/aluminum wheels on display in a variety of stands. Indeed, in addition to Riba, there are three European companies working on or taking to market now a carbon fiber wheel: Dymag, Mubea Carbo Tech, Carbures and ThyssenKrupp.
Miscellaneous notes
Release agents and additives supplier Poliya (Istanbul, Turkey) said it is expanding in to Latin America and hopes to establish a presence in the US.
Injection molding machinery supplier Engel (St. Valentin, Austria) said its in-situ caprolactam polymerization process is still in development and being trialed.
DUNA-USA (Baytown, TX, US) introduced Corintho 800, a high-density (50 lb/ft3), highly conductive polyurethane tooling board with a CTE comparable to aluminum (see photo).
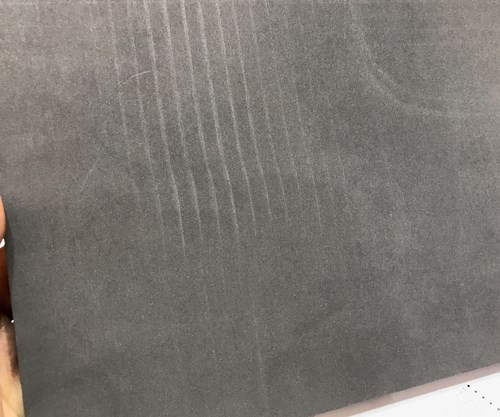
DUNA-USA's Corintho 800 high-density polyurethane tooling board.
Related Content
Post Cure: Natural mineral fiber biocomposite via AFP enhances implant integration
Arctic Biomaterials produces high-quality composite biomaterials incorporating a natural mineral fiber that is useful in medical and healthcare-related fields.
Read MoreSCABAEGO project develops bioactive composite that supports healing of broken bones
Fraunhofer IFAM researchers and partners combine biodegradable polymer polycaprolactone and bioactive glass to 3D print custom-fit structures for bone fracture sites.
Read MoreEvonik showcases chopped carbon fiber-reinforced PEEK filament
Vestakeep is available at two levels of carbon fiber content and appropriate for long-term surgical implants.
Read MoreMulti-material, self-sensing, 3D-printed scoliosis braces
Startup Fited and Brightlands Materials Center have developed a lighter weight, thinner CFRP corrective brace, including pressure sensors made from continuous carbon fibers.
Read MoreRead Next
VIDEO: High-volume processing for fiberglass components
Cannon Ergos, a company specializing in high-ton presses and equipment for composites fabrication and plastics processing, displayed automotive and industrial components at CAMX 2024.
Read MoreDeveloping bonded composite repair for ships, offshore units
Bureau Veritas and industry partners issue guidelines and pave the way for certification via StrengthBond Offshore project.
Read MoreAll-recycled, needle-punched nonwoven CFRP slashes carbon footprint of Formula 2 seat
Dallara and Tenowo collaborate to produce a race-ready Formula 2 seat using recycled carbon fiber, reducing CO2 emissions by 97.5% compared to virgin materials.
Read More