Recycling carbon fiber for structural applications
Research aims to characterize recycled carbon fiber (RCF) for use in aero interiors and also to recycle continuous carbon fiber.
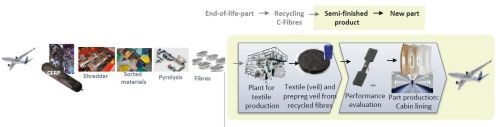
The Composite Technology Center is participating in the REKAS project to close the gap between recycling CFRP and reusing it in secondary structures for aircraft. Their investigations include forming semi-finished products and aviation-adapted production technologies, characterizing material performance and subsequent application in a non-structural aircraft interior part. SOURCE: CTC.
Characterizing reclaimed fibers
Tassilo Witte, a researcher at the Composite Technology Center (CTC, Stade, Germany), has been working with CFK Valley Recycling and CarboNXT GmbH (Wischhafen, Germany) with the goal of developing recycled carbon fiber materials for aircraft applications, specifically demonstration of a full-scale interior sidewall panel. “I think the mechanical performance is still not very well known,” Witte replies when asked why more suppliers of chopped fiber mats and compounds are not using reclaimed fibers. “For example, we are still asking what the precise knockdown factor is,” he continues, “and the exact properties vary with each process type and parameters.”
Commercial RCF suppliers say their products have a specified range of properties. “But that has to be also developed into a set of composite properties,” Witte contends. He describes how CTC is working to do this, starting first with the output of the CFK Valley Recycling process and performing a full battery of mechanical testing (e.g., tensile, compressive, flexural, etc.) on the filament, then the filament bundle, the monolithic laminate, sandwich laminate and finally small- and full-scale components. “So this is the classic test pyramid approach used in aircraft because it characterizes a material so that engineers can then design with it.”
CTC is performing a full battery of mechanical testing — from filament to laminate to full-scale components — in order to develop RCF properties into composite properties which aerospace engineers can use to design aircraft interiors and potentially other secondary structures.
SOURCE: CTC presentation at 2014 CFK Valley Convention, “Recycled carbon fibres and the development of semi-finished products for aircraft interiors.”
Witte has presented some key results from testing to date. Composite laminates made with nonwoven mat/veil and epoxy resin showed that RCF materials surpassed those made with virgin E-glass fibers for most load cases. Tensile modulus for a 20% fiber volume RCF veil laminate was the same as a 50% fiber volume virgin glass fiber laminate (see red and orange circle below).
RCF veils surpass glass fiber fabrics for most load cases and parts made with RCF non-woven veils can directly compete with those made from glass fabrics while offering less mass. SOURCE: CTC presentation at 2014 CFK Valley Convention.
Testing used CarboNXT RCF materials.
Witte concludes that RCF nonwoven parts can directly compete with glass fiber materials while offering significant weight savings. However, testing of RCF combined with thermoset resins also showed significant fiber pull-outs, implying reduced fiber-matrix coupling. Thus, Witte cautions that proper surface treatment of RCF materials is essential for thermoset applications. Testing of the CarboNXT RCF with thermoplastic matrices, however, showed superior adhesion. Tim Rademacker, managing director at CFK Valley Recycling and CarboNXT explains that pyrolysis burns off fiber sizings, so these must be re-applied before re-use, and that his products can be made with sizings tailored for either thermoset or specific thermoplastic matrix resins for increased fiber-to-resin bonding.
Another key finding is that maximum fiber volume (vf), for now, is limited to 30% or 35%. “There is a limit to the fiber volume possible for each fiber length,” says Witte. “In pressing flat laminates, if you compact above that [trying to add more fiber] you actually shorten the average fiber length, because they crush and fragment each other.” He does not see this as an obstacle necessarily, because 40% vf is typical of aircraft interiors materials today, noting this is typically S2 glass, not carbon fiber. He continues, “Materials with 35% vf using chopped CF have even better properties. Materials with a high vf, such as 60%, are used only for aircraft fuselage and wing structures, for example.”
CTC is on schedule to produce a full-scale aircraft interior sidewall panel in 2016 using RCF materials. SOURCE: CTC.
Lastly, Witte relates that first trials of nonwoven RCF laminates made using resin transfer molding (RTM) have shown little variation in overall performance, even though the fiber origins vary. Progress is on track to build and test full-scale sidewalls by 2016. “There is now a realistic opportunity to put our material into an aircraft interior application,” says Rademacker, “But if you had asked anyone three years ago, they would have said no way recycled carbon fiber would be used in aircraft.”
Reclaiming continuous carbon fiber
Tassilo Witte is not just working with chopped fiber, but has also received a patent for reclaiming continuous fiber from a wound composite structure, inspired by the opportunity to recycle millions of composite tanks. Market research firm Lucintel (Irving, TX, US) estimates that 374,000 composite compressed natural gas (CNG) tanks are produced annually for the global automotive industry and forecasts a compound annual growth rate (CAGR) of 10.4% to reach 613,000 units/yr by 2019.
“A filament wound pressure tank is one of the few composite parts where the continuous fiber is reachable and apparent,” explains Witte. In his method, the whole composite vessel is pyrolized in a chamber, with the fiber stabilized by the metal liner inside. “The vessel is then removed and the reinforcement is unwound, producing a continuous fiber more or less the same as before resin impregnation, winding and molding — with 90% of the properties vs. virgin fiber,” says Witte. He sees an even larger opportunity if the auto industry decides to use hydrogen fuel, and thus many more composite tanks.
The solvolysis process being developed by Dr. Heinrich Zeininger at Siemens Corporate Technology (Hamburg, Germany) also seeks to keep recycled carbon fibers continuous. The patent pending process heats the CFRP component under pressure to 200°C, converting the resin into low molecular-weight soluble alcohols with the help of water. Reportedly, no environmentally damaging solvents are used, and like pyrolysis, the process requires much less energy vs. manufacturing new fibers. Zeininger reports that woven fabric can be recovered with weave and fiber intact. Zeininger developed this process as part of the MAI Carbon Recycling initiative, with Germany-based partners including Audi (Ingolstadt), BMW (Munich), SGL Carbon (Wiesbaden), Voith Composites (Garching bei München) and technical papers producer Neenah-Gessner (Bruckmühl). In Siemens’ Pictures of the Future magazine, Zeininger explains that recycling is always a necessary part of new product development and, “Carbon fiber-reinforced materials will be used more and more by Siemens, for example, in motors and rotor blades.” He says the next challenge will be to integrate the reclaimed fabrics into new components.
Siemens is not the first, nor the only group to pursue solvolysis in recycling CFRP. Soraia Pimenta and Silvestre Pinho, researcers at Imperial College London, in the U.K., completed a thorough literature review on CFRP recycling operations, which was published by Elsevier in the journal Waste Management, 2011, pp. 378-392. This information has been updated and included in Ch. 19 of Elsevier’s award-winning Handbook of Recycling. The solvolysis processes reviewed include those using supercritical fluids (SCFs). An SCF is a substance at a temperature and pressure above its critical point, where distinct liquid and gas phases do not exist. Thus, it can penetrate porous solids like a gas, and dissolve organic materials like a liquid solvent. SCFs used to recycle CFRP include water, methanol, ethanol, acetone and propanol. Solvolysis using SCFs is recognized for producing RCFs with almost no degradation in mechanical properties (see bars for “Chemical” recycling process below) and the recovery of regenerable epoxy prepolymer compounds from the matrix.
![]() ![]() |
Modulus, E, and Strength, X, of recycled carbon fiber (rCF, green) vs. virgin carbon fiber (vCF, black) for various recycling processes where “FBP” stands for Fluidized Bed Process and “Chemical” represents solvolysis-type processes. SOURCE: Elsevier, Handbook of Recycling: State-of-the-art for Practitioners, Analysts, and Scientists by Ernst Worrell, Markus Reuter
Though much solvolysis development has been in Europe, Japan is also pursuing this technology. Hitachi Chemical (Tokyo, Japan), in its Technical Report No. 56 from March 2014, presents a table of CFRP chemical recycling technologies in Japan (see below) and then details its own non-SCF development, which uses tricalcium phospate as a catalyst and benzyl alcohol as the solvent — both are reportedly approved food ingredients and safe for human contact — at ordinary pressure and 200°C.
SOURCE: Hitachi Chemical Technical Report No. 56, CFRP Recycling Technology Using Depolymerization under Ordinary Pressure.
Note that pyrolysis occurs at 450°C to 700°C and other Japanese solvolysis methods require 250°C to 700°C. Hitachi demonstrated the process by recycling CFRP badminton and tennis rackets, the latter containing 50% CF by weight. In addition to CF and GF, aluminum frames and wooden grips were also recovered which is not possible with pyrolysis.
Nonwoven fabrics were then produced from the RCF through either a dry method using a carding machine or by a wet method via a paper pressing machine. (Carding disentangles and intermixes fibers to produce a continuous web or sliver suitable for subsequent processing. For example, wool is carded as a first step in making yarn.) In the carding method, several thin CF sheets were layered to form the nonwoven fabric, which was then compression molded, though the resin used was not specified.
Mechanical carding is used by
SGL Automotive Carbon Fibers (Wackersdorf, Germany) to process CF scrap from weaving and preform kitting for the BMW i-series CFRP Life Module production into stitched nonwoven materials (left) which are then molded into the i3’s rear seat structure and roofs for both the i3 and i8 (right). SOURCE: BMW
Hitachi Chemical has also used carding to produce non-woven materials from carbon fiber, but these were recycled from CFRP tennis rackets using a solvolysis process.
SOURCE: Hitachi Chemical Technical Report No. 56.
Resulting laminates were tested for tensile and bending properties and compared to CFRP made from virgin nonwoven mat. Hitachi observed no significant differences between the RCFRP and VCFRP. It did notice reduced properties when RCF content exceede 25% by weight. Hitachi then determined facilities and processing conditions required to treat 1,000, 2,000 and 17,000 rackets/month, including the energy consumption which totaled 91, 78 and 63 MJ/kg respectively. Hitachi summarized that the energy required to recover continuous CF plus epoxy prepolymers from 17,000 rackets/month is less than one-fourth of the 286 MJ/kg it calculated for comparable virgin CF production.
Related Content
3D weaving capabilities achieve complex shapes, reduce weight and cost
JEC World 2024: Bally Ribbon Mills is displaying film-infused 3D woven joints, woven thermal protection systems (TPS) and woven composite 3D structures.
Read More3D-woven composites find success in aerospace, space
CAMX 2024: Bally Ribbon Mills experts are displaying the company’s various joints, thermal protection system (TPS) technologies and other 3D woven composites for mission-critical applications.
Read MorePEEK vs. PEKK vs. PAEK and continuous compression molding
Suppliers of thermoplastics and carbon fiber chime in regarding PEEK vs. PEKK, and now PAEK, as well as in-situ consolidation — the supply chain for thermoplastic tape composites continues to evolve.
Read MoreBraskem demonstrates PP solutions using Weav3D composite lattice technology
Partnership combines Braskem’s polypropylene sheets with Weav3D Rebar for Plastics technology to address new structural, automotive applications requiring high-strength, lightweight material solutions.
Read MoreRead Next
Recycled carbon fiber update: Closing the CFRP lifecycle loop
Commercial production of recycled carbon fiber currently outpaces applications for it, but materials characterization and new technology demonstrations promise to close the gap.
Read MoreRecycled carbon fiber: Comparing cost and properties
Alex Edge, sales and business development manager for recycler ELG Carbon Fibre (Coseley, U.K.), says his company’s recycled carbon fiber (RCF) products can offer from 30 to 40 percent cost savings vs. virgin carbon fiber (VCF). Tim Rademacker, a managing director at competitor CFK Valley Recycling (Stade, Germany) cites savings of 20 to 30 percent.
Read MorePlant tour: Daher Shap’in TechCenter and composites production plant, Saint-Aignan-de-Grandlieu, France
Co-located R&D and production advance OOA thermosets, thermoplastics, welding, recycling and digital technologies for faster processing and certification of lighter, more sustainable composites.
Read More