Airborne launches Industrialization Partner Model
The model acts as a composite industrialization guide, enabling support from early composite production development up to technological implementation.
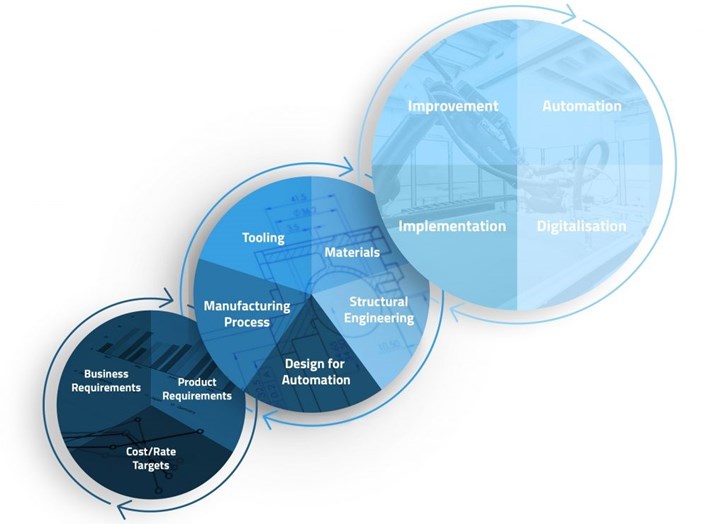
Airborne’s Industrialization Partner Model to be led by Joe Summers, commercial director at Airborne. Photo Credit: Airborne
In response to the need to address climate change and the disruption in most industry supply chains, Airborne (The Hague, Netherlands) has launched its Industrialization Partner Model to support customers from start to end in the composites industrialization journey. Led by newly appointed commercial director Joe Summers, this service guides the way for companies developing new products in composites or composites companies that want to industrialize. Further, the model is said to support from early design concepts, material and process choices, cost evaluation and business case development, up to creating and implementing the right automation and digitalization technologies, enabling full support and control of the customer at every stage.
According to Airborne, the Industrialization Partner Model provides a structured approach, including the evaluation of fundamental questions — product requirements, technical feasibility and full economic predictions of a product through its life — during the early stages of product development. For the development of new composite products, Airborne says it offers design services, prototyping, trade-off studies and design for automation, ensuring that parts are optimized for future high-rate manufacturing and are compatible with automation.
In next stages, says Airborne, for customers who wish to set up industrialized manufacturing, the company offers automation and digitalization system engineering considering different equipment and software options, business case analysis, and if appropriate, the supply of the company’s existing suite of automation solutions or the creation of a bespoke, integrated manufacturing line using third party equipment. The current Airborne suite includes Automated Kitting, Automated Honeycomb Potting, Automated Laminating, Automated Preforming and a platform of digital solutions.
Created out of a fundamental understanding of all aspects of composites, the company notes that its team of structural engineers, materials experts, tooling, processing and manufacturing engineers continuously work on new building blocks within the Industrialization Partner Model to serve clients with new features based on their needs.
Related Content
-
JEC World 2023 highlights: Innovative prepregs, bio-resins, automation, business development
CW’s Jeff Sloan checks in with JEC innovations from Solvay, A&P, Nikkiso, Voith, Hexcel, KraussMaffei, FILL, Web Industries, Sicomin, Bakelite Synthetics, Westlake Epoxy and Reliance Industries.
-
Plant tour: BeSpline/Addcomp, Sherbrooke, QC, Canada
Composites automation specialist increases access to next-gen technologies, including novel AFP systems and unique 3D parts using adaptive molds.
-
How AI is improving composites operations and factory sustainability
Workforce pain points and various logistical challenges are putting operations resilience and flexibility to the test, but Industry 4.0 advancements could be the key to composites manufacturers’ transformation.