Carbon fiber enables new, low-CO2 Skyrora orbital launch vehicle
U.K. private space company is developing and testing orbital launch vehicle Skyrora XL to carry small satellites in Earth’s orbit using eco-friendly fuel, a unified systems design and composites.
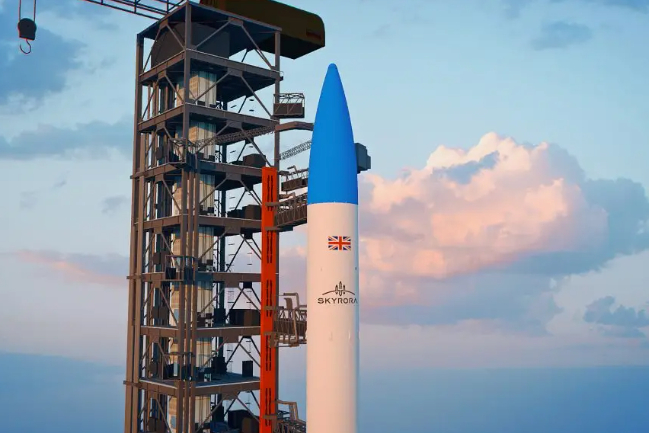
Skyrora XL rendering. Photo Credit, all images: Skyrora Ltd.
Skyrora Ltd. (Edinburgh, U.K.) is a private space company that specializes in the design, manufacturer and deploying of rockets for small satellite manufacturers looking to access space. Its most current orbital launch vehicle, Skyrora XL, is a composites-intensive 22.7-meter three-stage, light class launch vehicle intended to place payloads into sun-synchronous orbit (SSO) between a range of 500-1,000 kilometers in altitude and Polar Orbit between 200-1,000 kilometers in altitude. Over the past few months, Skyrora has bolstered its launch capabilities with a newly opened rocket engine manufacturing facility and completed second stage static fire engine testing for the flagship Skyrora XL rocket.
Skyrora XL’s modular design comprises three stages, a payload adapter and a payload fairing. The payload fairing casing is two halves of a three-layer composite shell with honeycomb filler. Bearing layers are carbon fiber. According to the company, a 10-layer composite shell with foam ribs has also recently been built. When the rocket reaches the required altitude, the halves of the payload fairing are released with the help of push-rod springs installed on the payload fairing casing. The third-stage propellant tanks of the launch vehicle incorporates carbon fiber prepreg overwrapped pressure vessels. Primary parts including interstage bays and the rocket’s high-pressure spheres also comprise composite materials. In addition, Skyrora conducted a 70-kilonewton engine test done with composite overwrap tanks (main body and spherical high pressure).
The rocket’s key design criteria the company notes is the unification of the launch vehicle’s main systems, assemblies and units, enabling a reduction in time and costs for design and testing, and increased reliability. The main combustion engine, Skyforce, is said to be unique in that it runs off of hydrogen peroxide and kerosene. It is used for the first and second stages. The LEO engine, also running off of hydrogen peroxide and kerosene, is a pressure-fed rocket engine, designed to power the third stage of Skyrora XL. Design of the thrust chamber is adapted for 3D printing, the company notes. Moreover, the premium kerosene fuel used — called Ecosene — is produced through a low-temperature catalytic pyrolysis process which is said to be more eco-friendly (avoiding dioxines and furanes formation, and reducing CO2 emissions by 70% compared to classic methods of fuel production) and uses polypropylene (PP), polyester (PE) and polystyrene (PS) plastic waste for its production; metallized packaging such as snacks or chips, as well as plastic that has been impacted by UV rays or salt water (for example, ocean water) and previously recycled plastic are additional components that can be used. While Ecosene will be used in launches, it is not currently in use, the company says, as it is still in the R&D stage.
An even more unique aspect of Skyrora XL — but a separate concept from the third-stage and 70-kilonewton engine mentioned above — is its “Space Tug” capabilities. Originally reported in Jan. 2021 by Techcrunch, the Skyrora team performed a third-stage static fire engine test at its Fife, Scotland, testing facility. An important discovery was that the third-stage engine can be reignited (not the whole vehicle) several times in orbit. This makes it able to perform a number of maneuvers in space, including the extraction of space junk or maintenance if satellites are already in orbit. The space tug is still in R&D stages.
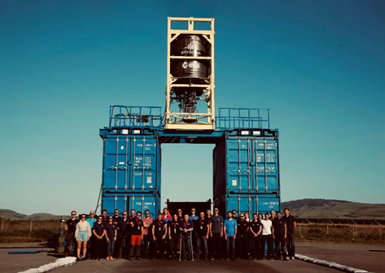
Second stage static fire test.
In July 2022 the company opened a new manufacturing and production facility, said to be the largest of its kind in the U.K. After opening its engine test facility in Midlothian, this new facility in Cumbernauld will enable the company to concentrate its launch development practices in custom-built domestic facilities, making it capable of conducting full-stage structural and pressure testing and full-stage functional and cold flow testing. The Skyrora Vehicle Assembly Building consists of 55,000 square feet of factory floor and office space, along with a 67,000-squaer-foot yard large enough to contain the entire Skylark L launch complex and future Skyrora XL launch facilities for rehearsals, integration works and launch preparation. The facility also has capacity to build 16 Skyrora XL vehicles once mass production begins, with the production of two rockets already commenced, the company reports.
“This purpose-built manufacturing and assembly site, combined with the Midlothian testing facility, allows Skyrora to take direct charge of the development cycle in-house,” Dr. Jack James Marlow, Skyrora’s head of engineering, says. “As a business, we now have a full set of domestic facilities to allow for close control of the quality and rapid development and testing of Skyrora XL ahead of its demo launch. The site will also allow us to further optimize manufacturing processes developed by our colleagues in Ukraine and scale-up launch vehicle production in the long term, enabling further expansion and growth in the future.”
Skyrora’s readiness to enter mass production correlates with its endeavors to become the first British company to launch a rocket from U.K. soil with Skyrora XL. By 2030, Skyrora aims to conduct 16 launches per year from the launch complex in the Shetland Islands alone.
Following these developments, the company successfully completed static fire test of the second stage of the flagship orbital rocket (see video above), hosted by Discover Space UK at Machrihanish Airbase, moving Skyrora closer to entering commercial operations. The test involves hot firing the second stage engine to prove the vehicle’s operational capability for its intended payloads and ensuring its performance meets all design requirements.
Skyrora says it was successfully completed with all systems nominal through the 20-second burn, and the single 70-kilonewton liquid engine — Skyforce —operated within design margins, achieving the expected thrust.
The second stage was assembled at Skyrora’s recently unveiled Cumbernauld manufacturing facility. Part of the three-stage launch vehicle, the second stage of Skyrora XL will start its engine at an altitude of approximately 62 kilometers before the third stage is fired at around 190 kilometers to achieve orbital velocity of 28,000 kilometers per house. Skyrora previously tested the third stage of its XL launch vehicle in Dec. 2020. The first stage of Skyrora XL is currently in construction, with hot fire tests due to take place in mid-2023.
“The static fire test looks, sounds and feels a lot like a rocket launch, but without lifting off!” Lee Rosen, Skyrora COO Col (USAF, Ret) and former SpaceX VP, says. “This successful test was a definitive demonstration of our mobility and flexibility. Our Skyrora team went from clean tarmac to a full static fire test in just 2.5 days, bringing all the necessary equipment from our factory in Cumbernauld and test site near Gorebridge.”
Related Content
Improving carbon fiber SMC simulation for aerospace parts
Simutence and Engenuity demonstrate a virtual process chain enabling evaluation of process-induced fiber orientations for improved structural simulation and failure load prediction of a composite wing rib.
Read MoreASCEND program update: Designing next-gen, high-rate auto and aerospace composites
GKN Aerospace, McLaren Automotive and U.K.-based partners share goals and progress aiming at high-rate, Industry 4.0-enabled, sustainable materials and processes.
Read MoreJeep all-composite roof receivers achieve steel performance at low mass
Ultrashort carbon fiber/PPA replaces steel on rooftop brackets to hold Jeep soft tops, hardtops.
Read MoreAurora reveals latest SPRINT X-Plane design concept
An Aurora and Boeing team advances its high-speed, vertical lift concept to the preliminary design phase, which features three lift fans, a more refined composite exterior and an uncrewed cockpit.
Read MoreRead Next
VIDEO: High-volume processing for fiberglass components
Cannon Ergos, a company specializing in high-ton presses and equipment for composites fabrication and plastics processing, displayed automotive and industrial components at CAMX 2024.
Read MorePlant tour: Daher Shap’in TechCenter and composites production plant, Saint-Aignan-de-Grandlieu, France
Co-located R&D and production advance OOA thermosets, thermoplastics, welding, recycling and digital technologies for faster processing and certification of lighter, more sustainable composites.
Read MoreDeveloping bonded composite repair for ships, offshore units
Bureau Veritas and industry partners issue guidelines and pave the way for certification via StrengthBond Offshore project.
Read More