Cevotec SAMBA Pro Prepreg system added to FPC technology portfolio
Installation of the automated Fiber Patch Placement system in Fraunhofer IGCV’s Fiber Placement Center serves active technology and application development.
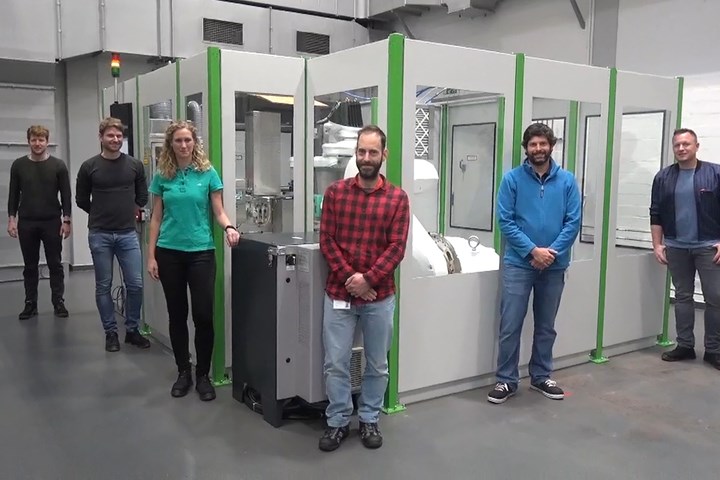
Photo Credit: Cevotec
The Fraunhofer Institute for Casting, Composite and Processing Technology IGCV (Augsburg, Germany) reported that it has taken a SAMBA Pro Prepreg production system from Cevotec GmbH (Munich, Germany) into operation at its Fiber Placement Center (FPC, Meitingen, Germany) of which SGL Carbon (Wiesbaden, Germany), Cevotec and Coriolis Composites (Queven, France) are also partners. The system is at the disposal of all FPC industrial partners as well as all interested companies to develop automated carbon fiber-reinforced polymer (CFRP) production processes on the basis of the Fiber Patch Placement (FPP) technology.
“When Cevotec officially joined the FPC at JEC World 2019, it was clear that a Fiber Patch Placement (FPP) system would be installed in the FPC to provide our partners and customers with a complete portfolio of the latest technologies and developments for the next generation of composite manufacturing,” says Hannah Paulus, head of Fiber Placement Center at SGL Carbon. “The new SAMBA Pro Prepreg System from Cevotec offers many advantages for the production of complex-shaped components with short cycle times.” Cevotec, together with its partner Baumann Automation (Amberg, Germany), have commissioned the SAMBA Pro Prepreg production cell in Meitingen since November 2020. The company reports that it is now ready for operation, and the first application development projects have already been started.
The SAMBA Pro Prepreg system in Meitingen is an advancement of the FPP system presented in 2017 at the JEC World in Paris. “In order to ensure maximum flexibility in terms of geometry and patch edges, a laser cutting unit was also installed in the system,” reports Felix Michl, CTO of Cevotec. “The entire material feed is temperature-controlled, so that the pre-impregnated materials can be processed in a controlled environment.”
The TP80 pick-and-place robot and the TX200 tool manipulator from Stäubli are the proven robots used in the system. “This configuration enables us to ensure a high layup frequency combined with a very high positioning accuracy, allowing for a fully automated layup of complex geometries of medium to small dimensions,” explains Michl. In addition, the vision system— the machine vision quality control system for material quality and placement accuracy — has been fundamentally revised by Cevotec and now offers extended setup options to adapt the system to different materials.
For example, prior to the installation of the system, SGL Carbon also entered into a development partnership with Cevotec. The aim is to develop innovative applications based on SGL TowPreg using the SAMBA systems. “The SGL TowPreg tape harmonizes perfectly with our system,” reports Michl. “We expect very interesting development projects, for example in the green mobility sector, aviation and medical technology.” In general, the SAMBA Pro system covers a wide range of different fiber materials that can be processed automatically for different industries.
“We look forward to developing the FPP technology further with our FPC partners and to opening up new fields of application,” says Thorsten Groene, managing director of Cevotec. “Within the context of the FPC, the production system serves interested industrial companies from various sectors for active technology and application development, together with the researchers of the Fraunhofer Institute.” Further, according to Dr. Renato Bezerra, research associate at Fraunhofer IGCV, Cevotec’s placement machine complements the institute’s portfolio of placement technologies and expands its scope of research and development services.
“The FPP technology can now prove itself in direct competition with different technologies in the FPC,” Michl concludes. “Interested customers can select the optimal technology for their specific application from the technologies available in FPC, which cover the entire spectrum of automated fiber placement. This is real value added for all manufacturers looking for innovative manufacturing solutions”.
Related Content
PEEK vs. PEKK vs. PAEK and continuous compression molding
Suppliers of thermoplastics and carbon fiber chime in regarding PEEK vs. PEKK, and now PAEK, as well as in-situ consolidation — the supply chain for thermoplastic tape composites continues to evolve.
Read MoreThe lessons behind OceanGate
Carbon fiber composites faced much criticism in the wake of the OceanGate submersible accident. CW’s publisher Jeff Sloan explains that it’s not that simple.
Read MoreCryo-compressed hydrogen, the best solution for storage and refueling stations?
Cryomotive’s CRYOGAS solution claims the highest storage density, lowest refueling cost and widest operating range without H2 losses while using one-fifth the carbon fiber required in compressed gas tanks.
Read MorePlant tour: Joby Aviation, Marina, Calif., U.S.
As the advanced air mobility market begins to take shape, market leader Joby Aviation works to industrialize composites manufacturing for its first-generation, composites-intensive, all-electric air taxi.
Read MoreRead Next
Exclusive preview of SAMBA preforming demo
Cevotec unveils its Artist Studio software and automated SAMBA preforming cell at JEC World 2017.
Read MoreCevotec scales up Fiber Patch Placement technology for large aerostructures
The SAMBA Step L automated fiber placement system can place patches of material up to 50 times larger than previous FPP systems.
Read MoreVIDEO: High-volume processing for fiberglass components
Cannon Ergos, a company specializing in high-ton presses and equipment for composites fabrication and plastics processing, displayed automotive and industrial components at CAMX 2024.
Read More