DIAB commits to circular business model
Diab uses recycled raw materials to make core materials; Diab customers can use such products with recycled content to help lower their carbon footprint and Diab assists in reusing its products at end of life.
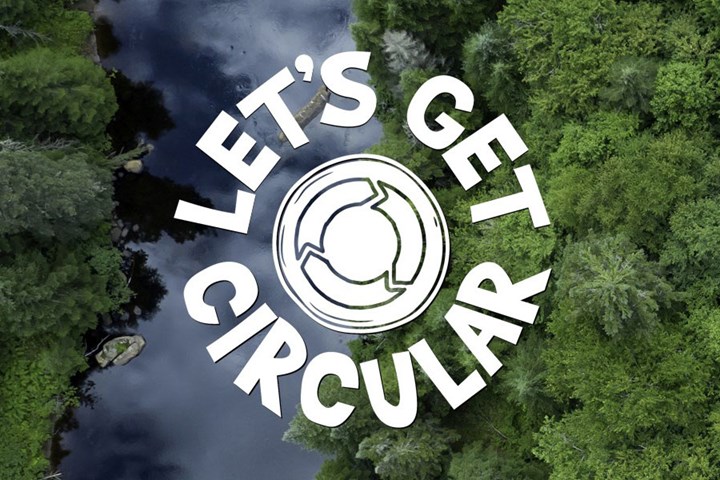
Photo Credit: Diab
- In a circular economy, companies recycle by-products as a resource to manufacture new materials and products, creating significant gains both for companies and the environment.
- The circular business model turns this thinking into a sustainable and profitable process realizing economic gains via greater resource efficiency for suppliers, manufacturers and end customers.
Diab (Helsingborg, Sweden) has supplied polymer foam core and balsa wood core materials into composites applications for decades, including services such as kitting, design assistance and resin infusion training. Instead of a linear model where materials travel through the system in one direction, Diab’s business model will be circular both in sales and sourcing. For example, by reusing post-industry and post-consumer plastic waste from its own processes and its customers' processes, Diab aims to reduce the carbon footprint and the cost of handling by-products for its facilities and those of its customers worldwide.
Diab reports its effort to reduce its own carbon footprint goes beyond managing sustainability performance. The company also works with its supply chain (Scope 3) because supporting its suppliers lowers their emissions which then benefits Diab’s products, and in turn, benefits Diab’s customers' applications. It’s a chain effect that works in both directions.
Diab notes this will also be financially beneficial when global carbon trading eventually gets implemented. With buying credits estimated to have a global price of 50-100 Euro/ton, companies must start today to transform into low-carbon business models. Diab will be a partner in this transition by committing to a circular business model, contributing to lowering the carbon footprint for its suppliers and customers. This includes:
1. Diab makes products with recycled raw materials, which lowers its carbon footprint in line with the science-based targets and, thereby, its customers’ carbon footprint. Diab has high sustainability goals, uses renewable energy in its plants and isresearching bio-based raw material alternatives.
2. Diab customers can use a recycled product in their application, lowering their carbon footprint. The low weight also contributes to a lower footprint during the application’s life cycle. Diab materials also have a long life span, making them beneficial in the life cycle assessment.
3. Diab products can easily be recycled or reused because Diab is transparent and provides clear information about the included materials. That makes it possible to reuse foam from one application at the end of life to produce new foam or use it in other products.
Related Content
-
Manufacturing the MFFD thermoplastic composite fuselage
Demonstrator’s upper, lower shells and assembly prove materials and new processes for lighter, cheaper and more sustainable high-rate future aircraft.
-
Recycling end-of-life composite parts: New methods, markets
From infrastructure solutions to consumer products, Polish recycler Anmet and Netherlands-based researchers are developing new methods for repurposing wind turbine blades and other composite parts.
-
Plant tour: Joby Aviation, Marina, Calif., U.S.
As the advanced air mobility market begins to take shape, market leader Joby Aviation works to industrialize composites manufacturing for its first-generation, composites-intensive, all-electric air taxi.