Digital design concepts shape next-generation combat aviation
Design processes that typically take months have been completed in days using BAE Systems' digital twin concept when developing the next-generation Tempest aircraft.
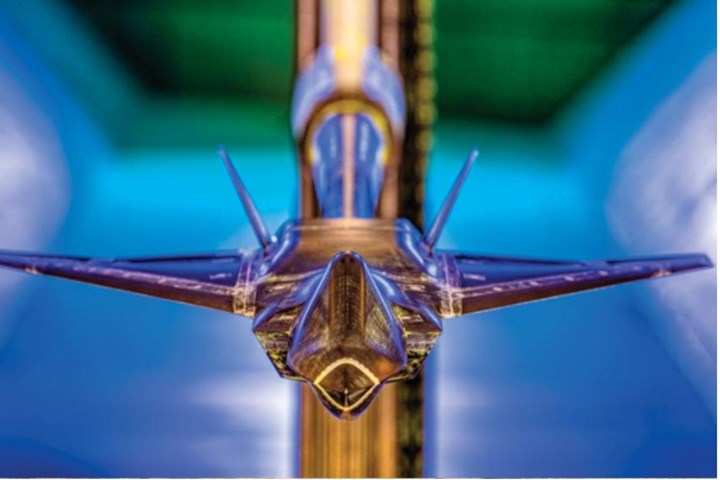
A 1:20 Tempest scale model in the wind tunnel at Warton during testing. Photo Credit: BAE Systems
It was reported in August 2020 that engineers at BAE Systems (Farnborough, U.K.) are exploiting the digital environment to design, test and fly concepts for Tempest, a next-generation combat air system for the U.K.
The company reports that, using digital twin technologies, conceptual shapes for the aircraft have been virtually designed and tested, with high-performance computers able to calculate the aerodynamic performance of different aircraft features and test pilots, taking Tempest to the skies from a ground-based simulator.
Once digitally tested, scale models were 3D printed and put through their paces at BAE Systems' wind tunnel facilities at Warton, Lancashire, to physically test the aerodynamic properties of the design under harsh wind speeds of more than twice the speed of sound. Data from these trials is now being used to refine and shape the final design of the U.K.'s next combat aircraft, which will be in service by 2035.
From initial designs, to manufacture and support, the concept will reportedly create an open and agile workspace for those involved on the program.
"The digital twin concept we have developed will be used to design, test and support every single system and structure for Tempest,” says Paul Wilde, head of Airframe Technologies, Tempest. “By taking an entirely digital approach to the challenge the UK Government has set us, we're transforming the way we work and adding incredible value to the program. We can achieve what traditionally would have taken a number of months in a number of days. As a result, we're working faster for the future and we're using the virtual environment to create endless opportunities for our engineers to experiment without boundaries, and with open minds — key to the future innovation of the program."
The research forms part of a wider U.K.-led effort to define the requirements for a future air combat system. BAE Systems is working closely with Rolls Royce (London), Leonardo (London) and MBDA (Stevenage) as part of Team Tempest to explore more than sixty technology areas in total, experimenting with different ideas ranging from the physical shape of an aircraft to the sophisticated sensors that will become the brains of a future system.
According to the company, this digital twin concept underpins the entire engineering lifecycle for Tempest. From initial designs, to manufacture and support, the concept will reportedly create an open and agile workspace for those involved on the program. It has also been adopted in the development of a Factory of the Future at Warton in Lancashire, which BAE Systems is currently using to demonstrate how the future fighter aircraft could be built. Here, data from intelligent robots, supply chain databases and machines is digitally threaded together to deliver increased efficiency and accuracy in the manufacturing process.
“Designing an aircraft has traditionally been an opportunity which comes up once in someone's career, which causes real challenges of transferring skills and knowledge,” acknowledges Michael Christie, director, Future Combat Air Systems, BAE Systems. “The technologies now available to us mean that we can reduce the design cycle which in itself is good for the affordability of a program, but we can also perform more cycles very quickly until we get it right. The UK Government has set us a significant challenge, but the program has some of the boldest and brightest minds on board who are breaking milestones at an accelerated pace and developing technologies and techniques that will be game-changing for the U.K. defense industry and beyond.”
BAE Systems is using data from the trials, combined with research across the program and together with its Team Tempest partners to contribute towards the development of an Outline Business Case to be considered by the UK Government, which is scheduled to be the next major decision point on commencing the next phase of a Combat Air Acquisition Programme for the U.K.
Related Content
Next-generation airship design enabled by modern composites
LTA Research’s proof-of-concept Pathfinder 1 modernizes a fully rigid airship design with a largely carbon fiber composite frame. R&D has already begun on higher volume, more automated manufacturing for the future.
Read MoreInfinite Composites: Type V tanks for space, hydrogen, automotive and more
After a decade of proving its linerless, weight-saving composite tanks with NASA and more than 30 aerospace companies, this CryoSphere pioneer is scaling for growth in commercial space and sustainable transportation on Earth.
Read MoreManufacturing the MFFD thermoplastic composite fuselage
Demonstrator’s upper, lower shells and assembly prove materials and new processes for lighter, cheaper and more sustainable high-rate future aircraft.
Read MorePlant tour: Joby Aviation, Marina, Calif., U.S.
As the advanced air mobility market begins to take shape, market leader Joby Aviation works to industrialize composites manufacturing for its first-generation, composites-intensive, all-electric air taxi.
Read MoreRead Next
FASTIGUE: Empowering digital twins of large-scale composite structures
A 3D finite element technique to resolve the fidelity-versus-speed dilemma of performing fatigue analysis for large composite structures.
Read MoreDigital thread vs. digital twin
Visualizing the difference between digital representations and data flows and understanding the applications that are changing composites manufacturing and business models.
Read More“Structured air” TPS safeguards composite structures
Powered by an 85% air/15% pure polyimide aerogel, Blueshift’s novel material system protects structures during transient thermal events from -200°C to beyond 2400°C for rockets, battery boxes and more.
Read More