Fibrolux supports Polish bridge with custom pultruded deck beams
More than 16 kilometers of fiberglass-pultruded profiles double Marshal Jozef Pilsudski Bridge capacity and upgrade its durability.
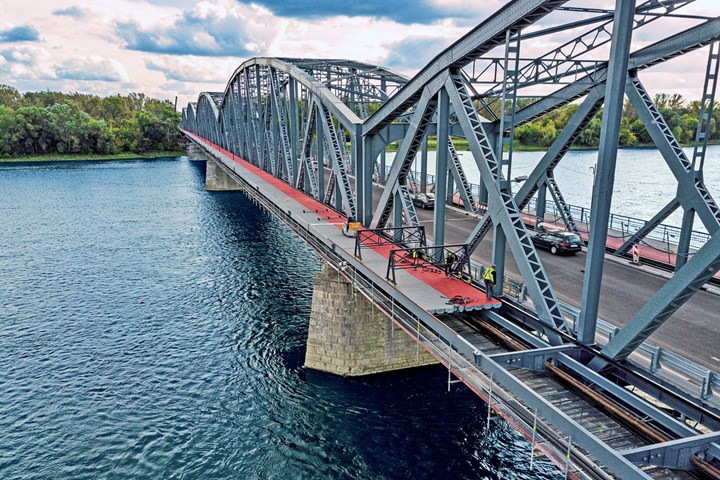
Retrofitted Marshal Jozef Pilsudski Bridge in Torun, Poland. Photo Credit, all images: Fibrolux.
Fibrolux GmbH (Hofheim, Germany), said to be one of the largest developer and manufacturer of pultruded composites in Europe, has completed its largest civil engineering project to date. Fibrolux has supplied more than 16 kilometers of large-scale, custom fiberglass-pultruded profiles to refurbish the 1-kilometer Marshal Jozef Pilsudski Bridge in Torun, Poland, with double-width pedestrian and cycling walkways, of which Fibrolux also delivered a pultruded composite slab solution.
Originally constructed in Münsterwalde, Germany, in 1909 as a road and railway crossing, the main bridge structure was disassembled and moved to Torun in north-central Poland in 1934. The extensive bridge upgrade program Fibrolux was a part of aimed to provide additional capacity and improve safety by moving cyclists away from the road carriageways.
The bridge concept, an interlocking walkway deck panel formed from eight massive triple-cavity pultruded profiles 500 millimeters x 150 millimeters in section, enabled the walkways on each side of the bridge to be expanded from 2 meters to 4.5 meters in width, creating safe space for cyclists. With the existing bridge structure unable to support the weight of wider steel walkways, the lightweight glass fiber composite structure delivered the required capacity upgrade as well as providing a low-maintenance, cost-effective solution for the project engineers.
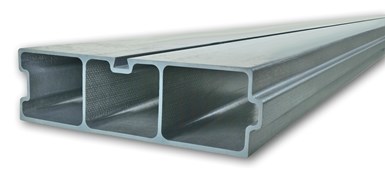
Large-scale, custom fiberglass-pultruded profiles.
Fibrolux says it created a custom die for the super-sized bridge profile before launching production of the 16 kilometers of profiles using a combination of assembled rovings and mats. The pultruded sections were delivered to site cut to length, assembled using custom stainless steel fasteners and then coated with an anti-slip coating, creating panels approximately 4 meters x 10 meters that could be lifted into position using a small crane. The assembly was carried out by the Polish company NTI Sp. z o.o. Nowoczesne Techniki Instalacyjne (Głogów).
Fibrolux will also supply a range of standard fiberglass-pultruded sections that will directly fasten to the composite walkway slabs and will be used to support the rainwater drainage system for the refurbished bridge.
“The Marshal Jozef Pilsudski Bridge project is a fantastic showcase for pultruded composites in civil engineering. Longer than nine football pitches, the new walkways highlight not only the weight saving and durability benefits of composites, but also the cost and time advantages of a large-scale Fibrolux custom profile design,” says Sebastien Mehrtens, business development director, Fibrolux GmbH.
Installation of the first phase of the walkway on one side of the bridge was complete in spring 2021. The second phase, which doubled the bridge’s previous capacity for pedestrians and cyclists, was completed in December 2021.
Related Content
-
Pultrusion: The basics
A primer describing what pultrusion is, its advantages and disadvantages, and typical applications.
-
PulFlex introduces pultruded Flex Connect
Fiberglass T-slot, primarily used for automation, framing and other quick setup systems, competes with aluminum alternatives.
-
Seat frame demonstrates next-generation autocomposites design
Light weight, simplified/cost-effective manufacturing, passenger comfort and safety informed materials and process innovations and won awards for the 2022 Toyota Tundra‘s second-row seat frame.