Lanxess expands Tepex flowcore composite range
Focusing on lightweight components for cars, sports equipment and consumer goods, the long fiber-reinforced thermoplastic enhances ductility, recylability and processability.
Share
Read Next
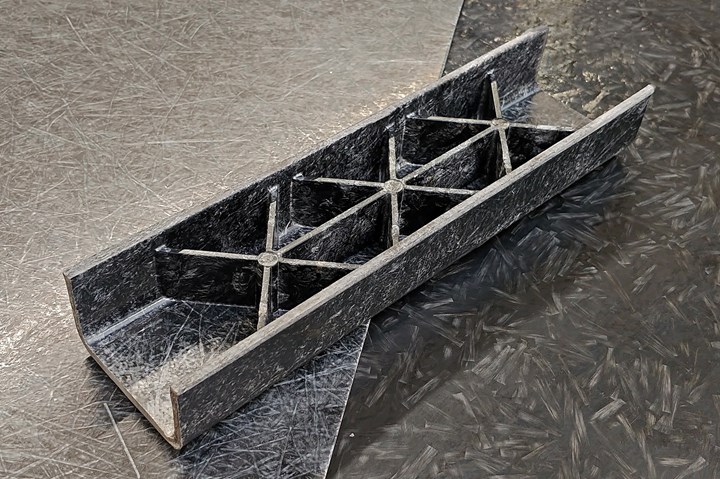
No additional injection-molded material was used to produce the ribbing on the demonstrator model. It is made entirely from compression-molded Tepex flowcore. Photo Credit: Lanxess
Lanxess (Cologne, Germany) reports that it has expanded and optimized its Tepex flowcore thermoplastic composite range for compression molding. The new composites are designed as alternatives to thermoset sheet molding compounds (SMCs), offering similar mechanical performance but with enhanced ductility, recylability and processability.
“We are primarily targeting Tepex flowcore at large underbody paneling components and load compartment wells for cars, but also at components such as large casings and battery covers,” says Sabrina Anders, project manager for Tepex flowcore at Lanxess High Performance Materials (HPM) business unit. Tepex flowcore has already proven its worth in series production, says the company, such as in a bumper beam for a mid-size sedan from a Japanese car manufacturer.
The novel, plate-shaped composites are offered with a matrix based on polypropylene (PP), polyamide 6 (PA6), polyamide 12 (PA12), thermoplastic polyurethane or flame-retardant polycarbonate. The matrix is reinforced with long fibers rather than the continuous fibers found in Tepex dynalite. The fibers are up to 50 millimeters in length and are distributed throughout the matrix as cut fibers of constant lengths. Tepex flowcore is offered with either glass or carbon fiber reinforcement.
In suitable processing conditions, Lanxess claims components made from the lightweight materials can exhibit almost the same flexural stiffness as their Tepex dynalite range equivalents, and have much higher strengths than injection-molded materials, which are usually reinforced with short fibers. Depending on processing method and component design, the fibers can be arranged in one preferred direction or at complete random. “The components can be designed such that they exhibit mechanical properties quasi-isotropically; in other words, almost identically in all directions,” explains Anders.
Moreover, Tepex flowcore is said to be more versatile in terms of processability. For example, they can be compression molded with standard tools for long fiber- or glass mat-reinforced thermoplastics (LFTs and GMTs). They can also be used with existing SMC systems and tools.
“They have such good flow characteristics that delicate areas of components, such as ribbed structures, can be reproduced with great precision, and walls can be made very thin,” says Anders. Tepex flowcore and Tepex dynalite can also be used together in compression molding processes, demonstrating optimized adhesion between each other due to their identical polymer matrix. “This opens up the opportunity to use Tepex dynalite to reinforce specific component areas under particularly heavy stress and, at the same time, to integrate features such as guides and mounts in a cost-saving way with Tepex flowcore. Another benefit is that the processor obtains all these composite semi-finished products from one place rather than having to combine materials from different manufacturers.”
The new composites — much like Tepex dynalite — are also said to be well suited to the hybrid molding process. This involves forming in an injection molding tool and given features by means of injection molding in a single process. The production of the bumper support for the Japanese sedan went one step further. That structural component was made from Tepex flowcore and Tepex dynalite, overmolded and functionalized with a PA6 compound from the Durethan brand.
Related Content
JEC World 2023 highlights: Innovative prepregs, bio-resins, automation, business development
CW’s Jeff Sloan checks in with JEC innovations from Solvay, A&P, Nikkiso, Voith, Hexcel, KraussMaffei, FILL, Web Industries, Sicomin, Bakelite Synthetics, Westlake Epoxy and Reliance Industries.
Read MoreActive core molding: A new way to make composite parts
Koridion expandable material is combined with induction-heated molds to make high-quality, complex-shaped parts in minutes with 40% less material and 90% less energy, unlocking new possibilities in design and production.
Read MoreJEC World 2023 highlights: Recycling, biocomposites, smaller equipment and expanding brands
CW senior technical editor Ginger Gardiner addresses some of this year’s hot topics, ranging from novel biocomposites and recycling technology solutions from myriad startups to upgraded, but equally sustainable, equipment from well-established companies.
Read MoreHybrid process marries continuous, discontinuous composites design
9T Labs and Purdue applied Additive Fusion Technology to engineer a performance- and cost-competitive aircraft bin pin bracket made from compression-molded continuous and discontinuous CFRTP.
Read MoreRead Next
Tepex composite opens up new opportunities for electric skateboards
The continuous fiber-reinforced thermoplastic is used for a trough-shaped skateboard deck application, notable for its high torsional and bending strength, light weight and moisture protection.
Read MorePlant tour: Daher Shap’in TechCenter and composites production plant, Saint-Aignan-de-Grandlieu, France
Co-located R&D and production advance OOA thermosets, thermoplastics, welding, recycling and digital technologies for faster processing and certification of lighter, more sustainable composites.
Read MoreAll-recycled, needle-punched nonwoven CFRP slashes carbon footprint of Formula 2 seat
Dallara and Tenowo collaborate to produce a race-ready Formula 2 seat using recycled carbon fiber, reducing CO2 emissions by 97.5% compared to virgin materials.
Read More