Tepex composite opens up new opportunities for electric skateboards
The continuous fiber-reinforced thermoplastic is used for a trough-shaped skateboard deck application, notable for its high torsional and bending strength, light weight and moisture protection.
Share
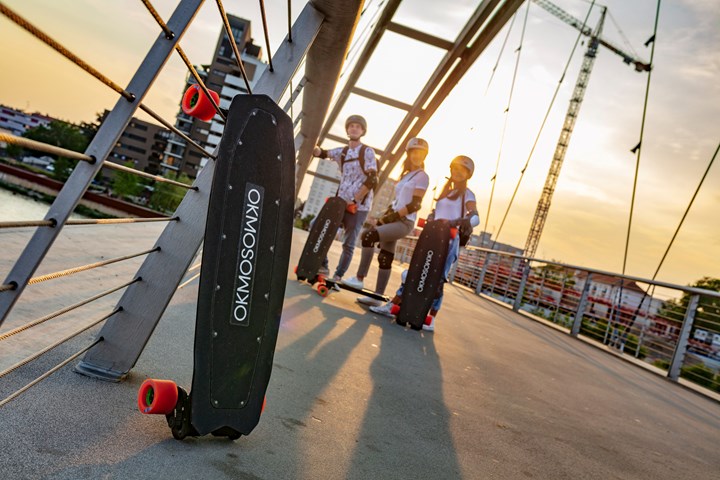
EMI SAS’ OKMOS SL-01 electric skateboards. Photo Credit, all images: EMI SAS
Lanxess (Cologne, Germany) reports that Tepex dynalite continuous fiber-reinforced thermoplastic materials open up new opportunities for electric components that need to be housed in light, compact and confined spaces. This is exemplified by its recent application in OKMOS SL-01 electric skateboards developed by family owned business EMI SAS (Saint-Louis, France), which has also made its name with products such as continuous fiber-reinforced plastic composite parts for lightweight vehicle structures.
Conventional skateboards usually consist of a relatively flat wooden board where the rider stands — also known as the deck. Underneath the deck for electric skateboards is a plastic box containing equipment, including the battery. The EMI design, however, features a trough-shaped deck. With the exception of the motors, which are mounted on the back of the skateboard, this houses all the electric and electronic functions, including the battery. The trough is enclosed by a cover. Using Tepex, EMI is able to manufacture the trough-shaped part with a wall thickness of just three millimeters — and despite the thin walls, the electric and electronic components in the deck are said to be safely protected against impact as well as moisture.
“Tepex is resilient thanks to its high torsional and bending strength, and light weight. The deck weighs just 2.5 kilograms [5.5 pounds],” says Jean-Marie Olivé, technical manager application development at the High Performance Materials (HPM) business unit at Lanxess.
According to Lanxess, the trough-shaped composite part is manufactured in a single hybrid molding process step. A robot inserts the metal base plate used to attach the truck axles into an injection molding tool. Then, a heated and plasticized Tepex section is placed within the tool. In one operation, the section is formed and the entire structure overmolded with a short glass-fiber-reinforced plastic compound.
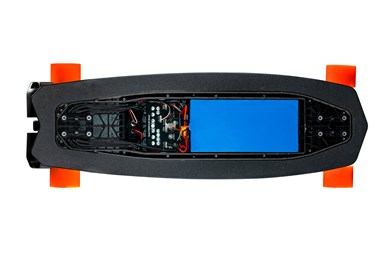
The trough-shaped deck houses all the electric and electronic functions, including the battery, except for the motors, which are mounted on the back of the skateboard.
“The process is very efficient and highly integrated, meaning that not only can the base plate be fixed in place, but fastening elements, wire ducting and the battery holder can also be mounted in the same operation. That means that unlike many conventional electric skateboards, the latter does not have to be screwed in separately,” explains Jules Staedelin, manager for research and development (R&D) at EMI.
The composite section is made from polyamide-6 (PA6)-based Tepex dynalite 102-RG600(6), which is reinforced with six layers of continuous glass fiber rovings. The deck cover is also made from this material. Lanxess’ PA6 Durethan BKV30H2.0EF is used for overmolding. Containing 30% short glass fibers by weight, the compound melt flows easily, making it suitable for this type of application.
Lanxess demonstrates its Tepex material for other applications, such as an automotive load compartment well and a structural bracket.
Related Content
-
Bio-based acrylonitrile for carbon fiber manufacture
The quest for a sustainable source of acrylonitrile for carbon fiber manufacture has made the leap from the lab to the market.
-
Natural fiber composites: Growing to fit sustainability needs
Led by global and industry-wide sustainability goals, commercial interest in flax and hemp fiber-reinforced composites grows into higher-performance, higher-volume applications.
-
Plant tour: Albany Engineered Composites, Rochester, N.H., U.S.
Efficient, high-quality, well-controlled composites manufacturing at volume is the mantra for this 3D weaving specialist.