Loop Technology develops robotic arm for wing box inspection
Part of an R&D project with Spirit AeroSystems, the seven-axis Bravura robotic arm automates inspection and sealing within small spaces like aircraft wing boxes.
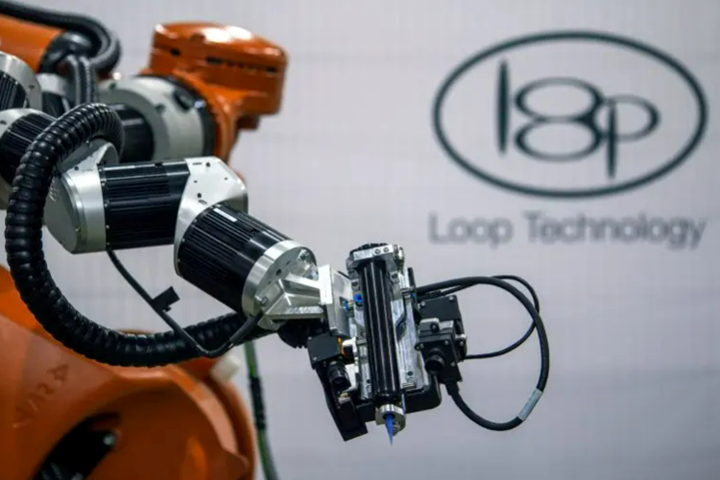
Photo Credit: Loop Technology
Loop Technology (Dorchester, U.K.) announces the development of Bravura, a robotic arm to deliver highly accurate automation including sealing and inspection inside aircraft wings and other confined spaces. The technology is the result of a four-year, Aerospace Technology Institute (ATI, London, U.K.) research project with Spirit AeroSystems (Wichita, Kan., U.S.) that concluded in September 2022.
According to Loop Technology, assembly inside confined spaces such as wing boxes is a major challenge for aerostructure manufacturers. These processes have remained a manual task due to the gap in the market for an automated solution with a high degree of accuracy, a relatively high payload and suitable reach in order to replace the use of hand tools.
In response, Loop Technology has developed a seven-axis, robotically controlled, articulated positioner called Bravura to address this gap. It can be used with an industrial robot to automate subassembly operations including sealing and inspection inside wing boxes, and is said to have potential for other applications such as nut-running and swaging. The system has a reach of 1,100 millimeters and can manipulate tooling end effectors up to five kilograms in weight.
“Bravura extends the possibilities of end of arm tooling [EOAT] by adding 6 degrees of freedom in a compact form factor with high torque motors, continuous rotation and a unique path planning solution,” says Ross Horrigan, technical director at Loop Technology. “Although Bravura is an articulated robot in its own right, it is typically deployed as EOAT for a larger robot. To insert Bravura smoothly and accurately into a wing box, we use the kinematic coupling capabilities of the Bravura controller to move all thirteen axes simultaneously.”
This project was part of a larger project called OptiComp (Optimised Composite Wings and Aerostructures), which was led by Spirit’s Belfast facility to ensure the U.K. aerospace industry is positioned as a global leader in the design, development and production of large, complex aerostructures (particularly wings).
According to Loop, similar technology to target this application has been developed in the past such as snake-arm robots. However, unlike snake-arm robots that can be disadvantaged by low stiffness and compromised accuracy due to being cable-driven, Bravura uses frameless servo motors paired with high ratio harmonic gearboxes for high power density drive units to operate with high precision.
In addition to the end of arm positioner, Loop Technology has also developed a complementary toolkit of EOAT with built-in vision for use in space restricted areas.
Related Content
-
Xnovo Technology, Exciscope introduce X-ray tensor tomography technique
Through a strategic partnership, the companies introduce the FiberScanner3D module, dedicated to bringing more rapid, reliable and robust fiber structure characterization methods to lab settings.
-
Automated robotic NDT enhances capabilities for composites
Kineco Kaman Composites India uses a bespoke Fill Accubot ultrasonic testing system to boost inspection efficiency and productivity.
-
Innovation in ultrasonic inspection and nondestructive testing
With increasingly complex structural components working their way into aerospace programs, the need for versatility in inspection and testing capabilities is growing.