NREL researchers point to path for improved wind blade recycling rates
Researcher consider strategies like policy regulation and recycling technology development to mitigate the impact of end-of-life wind blades.
Share
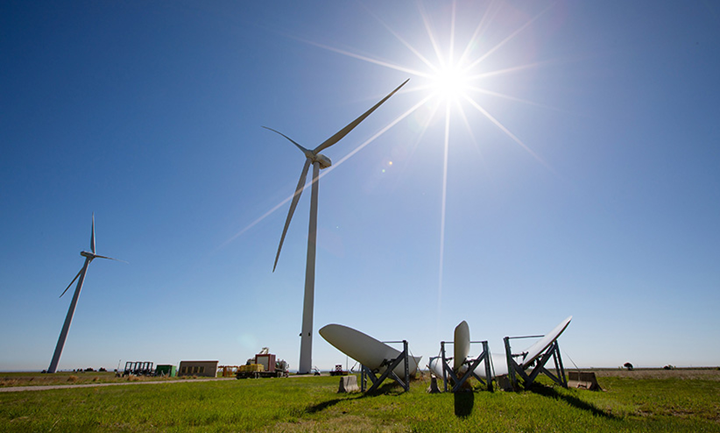
Photo Credit: Werner Slocum, NREL
Researchers at the National Renewable Energy Laboratory (NREL, Golden, Colo., U.S.) are considering circular economy strategies to mitigate the impact of wind turbine blades at the end of their useful lifespan.
The strategies are meant to address what to do with the blades once they are no longer needed, including using new materials that are easier to break down, extending their lifespan and implementing various recycling options. Researchers at NREL have been investigating novel blade materials, like thermoplastics, that are inherently more recyclable, thereby integrating solutions at the earliest stages of turbine component design.
“We want to see everything recycled, ideally,” says Aubryn Cooperman, an engineering analyst at NREL and co-author of a new paper outlining the steps that need to be taken.
Realistically, however, as wind turbines reach the end of their useful, expected 20-year lifespan, some of the blades are bound to be discarded, NREL notes. More than 90% of wind energy facilities in the U.S. began generating power within the last decade. An estimated 10,000 to 20,000 blades annually are expected to be at the end of their lifespan between 2025 and 2040 (learn more, “Defining the landscape for wind blades at the end of service life”).
In the absence of policy change or recycling technology development, as much as 78% of decommissioned blades are expected to end up in landfills.
Owners of wind power plants will be increasingly faced with decisions about what to do with these blades, the researchers noted in a new paper, “Regional Representation of Wind Stakeholders’ End-of-Life Behaviors and Their Impact on Wind Blade Circularity.” In addition to Cooperman, the iScience article was co-authored by NREL researchers Julien Walzberg, Liam Watts, Annika Eberle, Alberta Carpenter and Garvin Heath.
The scientists relied on a computer model that considers behavioral factors, which can undermine the viability of technical solutions. For example, a lack of trust in a new technology may keep it from reaching its full market potential. Therefore, the researchers point out, it is considered critical to understand the behavioral aspects of wind power industry stakeholders’ decisions. Those stakeholders run the gamut from operators of wind sites to companies in the recycling business. The modeling tool, developed by researchers at NREL and publicly available, is the Circular Economy Wind Agent-Based Model.
The researchers say that in the absence of policy change or recycling technology development, as much as 78% of decommissioned blades are expected to end up in landfills, though that still would be a relatively small percentage of the amount of discarded waste at an estimated 1% nationwide in 2050. Among the factors hindering recycling are high transportation costs and subjective norms, which discourage people from recycling the blades if they see others not already doing so. By encouraging enough early adopters, recycling blades would become the norm, according to the NREL.
“Transportation costs are a huge factor, because the blades themselves are huge,” Walzberg, the paper’s lead author, say. “If your recycling facility is far away, that’s going to make it a barrier for you to try to recycle.”
A “more profound shifts in recycling technologies, blade materials or policy may be needed to move towards a circular economy for wind turbine blades.”
Lowering those transportation costs could make a significant difference in how the old blades are disposed of. The blades are typically made of steel, plastic and composite materials. While many of the materials now commonly used for the blades are easily broken down, they can be shredded with the right equipment.
“Shredding the blades makes them smaller and easier to ship to a recycling facility,” Walzberg adds. “That’s kind of a low-hanging fruit. But you need to be able to shred the blades before transportation.”
Even reducing the cost of shredding blades by a third before transportation could decrease the cumulative landfill rate below 50%, the scientists calculated in the new study. Another scenario that involves boosting early adoption of recycling so that it becomes the norm could bring the figure below 10%.
Walzberg says regulations could help boost recycling numbers as well and pointed to laws enacted to keep lead-acid batteries from landfills and old rubber tires from being burned. According to the researchers, future work could study how increasing the number of recycling facilities for wind turbine blades could change the results.
The journal article builds on research published last year by Cooperman, working alongside Eberle and another NREL colleague, Eric Lantz. That article revealed “more profound shifts in recycling technologies, blade materials or policy may be needed to move towards a circular economy for wind turbine blades.”
Suppliers, fabricators and OEMs across the composite wind blade supply chain, for example, are ramping up existing technologies, developing better reclamation methods and designing more recyclable wind blades, “Moving toward next-generation wind blade recycling.”
Funding for the research came from the U.S. Department of Energy’s (DOE’s) Advanced Manufacturing Office and the Office of Strategic Programs.
Related Content
Plant tour: Arris Composites, Berkeley, Calif., U.S.
The creator of Additive Molding is leveraging automation and thermoplastics to provide high-volume, high-quality, sustainable composites manufacturing services.
Read MoreRecycling end-of-life composite parts: New methods, markets
From infrastructure solutions to consumer products, Polish recycler Anmet and Netherlands-based researchers are developing new methods for repurposing wind turbine blades and other composite parts.
Read MoreASCEND program update: Designing next-gen, high-rate auto and aerospace composites
GKN Aerospace, McLaren Automotive and U.K.-based partners share goals and progress aiming at high-rate, Industry 4.0-enabled, sustainable materials and processes.
Read MoreRecycling hydrogen tanks to produce automotive structural components
Voith Composites and partners develop recycling solutions for hydrogen storage tanks and manufacturing methods to produce automotive parts from the recycled materials.
Read MoreRead Next
VIDEO: High-volume processing for fiberglass components
Cannon Ergos, a company specializing in high-ton presses and equipment for composites fabrication and plastics processing, displayed automotive and industrial components at CAMX 2024.
Read MorePlant tour: Daher Shap’in TechCenter and composites production plant, Saint-Aignan-de-Grandlieu, France
Co-located R&D and production advance OOA thermosets, thermoplastics, welding, recycling and digital technologies for faster processing and certification of lighter, more sustainable composites.
Read MoreAll-recycled, needle-punched nonwoven CFRP slashes carbon footprint of Formula 2 seat
Dallara and Tenowo collaborate to produce a race-ready Formula 2 seat using recycled carbon fiber, reducing CO2 emissions by 97.5% compared to virgin materials.
Read More