OCSiAl confirms compliance with IATF 16949 standard for graphene nanotubes
Compliance paves way for wider graphene nanotube application in the automotive industry, including batteries, tires and anti-friction and anti-wear coatings.
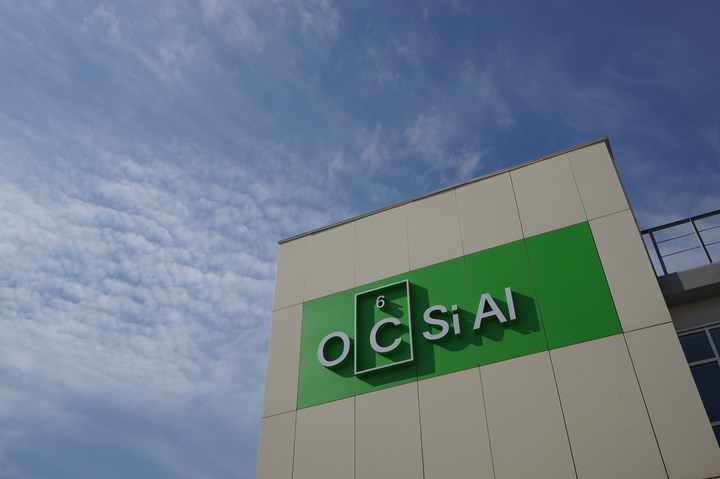
Photo Credit: OSCiAl
OCSiAl (Leudelange, Luxembourg and Columbus, Ohio, U.S.) has confirmed its graphene nanotube solutions production facility and quality management system (QMS) to be compliant with the IATF 16949 standard, validating its status as a reliable graphene solutions supplier and paving the way for wider application of graphene nanotubes in the auto industry. According to the company, key points noted during the IATF check were the company’s system for handling clients’ feedback, the raw material and product storage system, the equipment for nanotube solutions for battery production and the risk assessment system.
“Long, flexible, electrically conductive and strong graphene nanotubes significantly enhance and even grant new properties to literally all materials that are being used in cars. They make it possible to produce safer, lighter, smarter and more eco-friendly vehicles to facilitate the ongoing fundamental transformation of the auto industry,” says Konstantin Notman, OCSiAl senior vice president.
In batteries, OCSiAl says, graphene nanotubes serve as bridges between silicon particles, creating a robust network inside the anode and protecting it from degradation. Additionally, the use of nanotubes reportedly results in an energy density of up to 350 watt-hours per kilogram (Wh/kg), the possibility of increasing SiO content for 90% faster charging and improved safety.
Further, the modification of plastics with graphene nanotubes is said to lead to impressive results in anti-friction and anti-wear coatings, as well as exterior parts painted using the electrostatic painting method. OCSiAl says graphene nanotubes optimize the overall performance of tires, improve abrasion resistance for longer life, bring a strong improvement in wet grip that boosts safety and enables improvement in rolling resistance that reduces vehicles energy consumption and emissions.
“To intensify our joint developments with partners in transportation materials engineering, OCSiAl launched its state-of-the-art R&D and technical support center in Luxembourg in September 2020 with the focus on solutions for auto industry,” adds Mr. Notman. Other centers of this kind are located in Asia and Eastern Europe.
Related Content
-
Recycling hydrogen tanks to produce automotive structural components
Voith Composites and partners develop recycling solutions for hydrogen storage tanks and manufacturing methods to produce automotive parts from the recycled materials.
-
ASCEND program update: Designing next-gen, high-rate auto and aerospace composites
GKN Aerospace, McLaren Automotive and U.K.-based partners share goals and progress aiming at high-rate, Industry 4.0-enabled, sustainable materials and processes.
-
Carbon fiber, bionic design achieve peak performance in race-ready production vehicle
Porsche worked with Action Composites to design and manufacture an innovative carbon fiber safety cage option to lightweight one of its series race vehicles, built in a one-shot compression molding process.