Solvay, GKN Aerospace renew collaboration agreement
Both companies aim to expand the use of thermoplastic composite materials on high-rate aerospace structures.
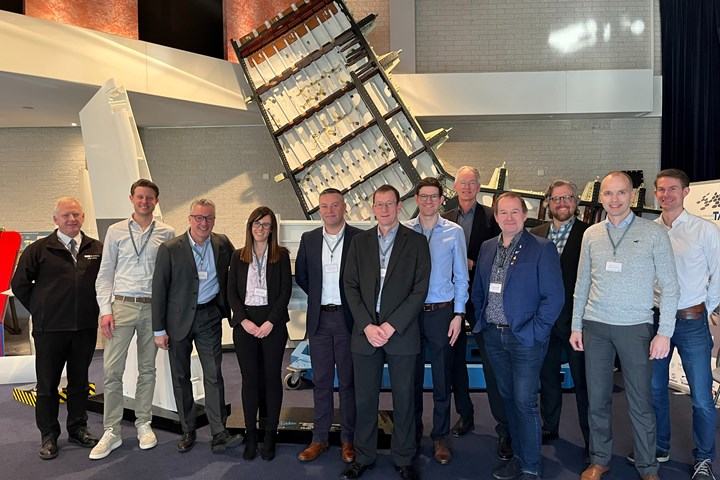
Solvay (Alpharetta, Ga., U.S.) and GKN Aerospace (Solihull, U.K.) have signed an extension to their 2017 collaboration agreement. Under the agreement, both businesses are developing a joint thermoplastic composites (TPC) roadmap to explore new materials and manufacturing processes for aerospace structures, while jointly targeting future strategic high-rate programs.
In addition, Solvay will remain a GKN Aerospace preferred supplier for TPC materials. Over the past six years, Solvay and GKN Aerospace have engaged on successful projects such as a TPC wing rib program where the use of TPC and a one shot manufacturing process enabled the development of a lighter and cost competitive part; as well as the development of a cost-effective AFP TPC fuselage panel opening the door to primary structure applications.
“We are excited to continue collaborating with GKN Aerospace,” says Fabrizio Ponte, head of Solvay Thermoplastic Platform. “Going forward our teams will specifically work on next-generation TPC materials and processes for aerospace applications including commercial aviation and advanced air mobility. Our particular focus on high-rate manufacturing solutions for medium and large structures.”
Arnt Offringa, director of GKN Aerospace’s Global Technology Centre in the Netherlands, says, “We are delighted to renew our agreement with Solvay. Lightweight technologies will play a key role in the journey to more sustainable aviation and working together has strengthened our technology leadership in thermoplastic innovation. Collaboration will be vital as we continue to push the boundaries of technology in order to meet our sustainability targets.”
Solvay reports that its PEKK (polyetherketoneketone) composites and PEKK films play an important role in supporting GKN Aerospace’s TPC development activities in aircraft.
Related Content
-
Jeep all-composite roof receivers achieve steel performance at low mass
Ultrashort carbon fiber/PPA replaces steel on rooftop brackets to hold Jeep soft tops, hardtops.
-
Optimizing a thermoplastic composite helicopter door hinge
9T Labs used Additive Fusion Technology to iterate CFRTP designs, fully exploit continuous fiber printing and outperform stainless steel and black metal designs in failure load and weight.
-
Composites manufacturing for general aviation aircraft
General aviation, certified and experimental, has increasingly embraced composites over the decades, a path further driven by leveraged innovation in materials and processes and the evolving AAM market.