ExOne launches comprehensive industrial-grade, 3D-printed tooling solutions
X1 Tooling, reported to be the broadest portfolio available to manufacturers, offers fast, affordable and local tooling options for the final production of metal, plastic and composite designs.
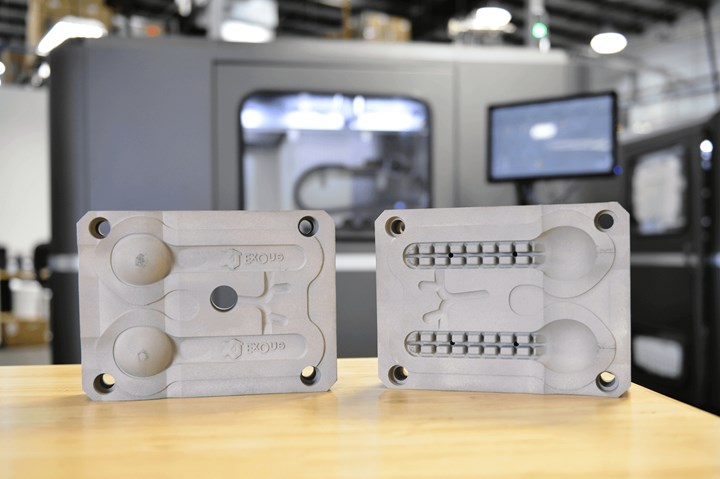
X1 MetalTool is shown for a plastic injection molding application in front of the X1 25Pro metal 3D printer. Photo Credit: Business Wire
ExOne (North Huntington, Penn., U.S.), a company that provides industrial sand and metal 3D printers using binder jetting technology globally, launches X1 Tooling, what it says is the broadest portfolio of industrial-grade, 3D-printed tooling available, the X1 Tooling. The range now offers new solutions for plastic injection molding or forming, composites layup, casting metals and more.
In all, manufacturers are now able to leverage six new and affordable tooling applications from ExOne:
Composites production:
- X1 Layup: A 3D-printed sand form is infiltrated with a durable resin and coated for high-precision, high-temperature composite layup applications. X1 Layup offers dimensional tolerances of ± 0.025” and tooling can be precision machined to ± 0.005” if needed.
- X1 Washout: This 3D-printed sacrificial tooling washes out with tap water after traditional layup and autoclaving of composite materials, including carbon fiber. X1 Washout is a sand form 3D printed with a water-soluble binder and surface coated. Ideal for ducting, mandrels and other designs with trapped geometries.
Plastic production:
- X1 MetalTool: This 3D-printed metal tooling option has passed preliminary tests to replace standard steel or aluminum tooling for plastic injection molding, blow molding and other plastic and foam forming applications. X1 MetalTool is available in 420i, a highly durable and affordable steel-bronze matrix, as well as 316L stainless steel, M2 tool steel and more. This tooling can be finish machined, acid etched and polished to a diamond finish, and is currently ideal for complex inserts. ExOne is currently seeking additional development partners to expand durability testing of this product line.
- X1 ThermoForm: A 3D-printed sand form is infiltrated with a durable resin and coated to create small- to large-format molds for a variety of thermoforming applications, such as vacuum forming, compression molds, foam molding and more.
Metal Production:
- X1 SandCast: For sand molds and cores for metalcasting. Sandcastings can be delivered in a variety of sand types and binders, including sustainable inorganic formulas for high-quality aluminum castings.
- X1 MetalTool: In addition to plastic forming applications, X1 MetalTool can also be used to directly 3D print end-of-arm tooling, and rugged perishable or consumable cutting tools in a variety of metals, including tool steels.
- X1 DieMold: Still in development, rugged die molds 3D printed in H13 tool steel are currently fast-tracked with several global manufacturers after passing proof of concept tests.
Manufacturers can now purchase X1 Tooling products directly from ExOne through the company’s ExOne Adoption Centers—or manufacturers can purchase a 3D printer for tooling applications.
Sizing options vary for the type of tooling as detailed below:
- All sand- and sand-infiltrated tools, which includes X1 ThermoForm, X1 Layup, X1 Washout, X1 SandCast, are produced in the build volume of ExOne S-Max series printers: 1,800 x 1,000 x 700 mm (70.9 x 39.4 x 27.6”). The printed sections can also be segmented and assembled together before epoxy infiltration to make even larger tools.
- Currently, all X1 MetalTool and X1 DieMold tools are 3D printed in an X1 25Pro build volume of 400 x 250 x 250 mm (15.75 x 9.84 x 9.84”), with development underway to 3D print tooling options in the X1 160Pro, which offers a build volume of 800 x 500 x 400 mm (31.5 x 19.7 x 15.8”).
Related Content
Optimized approach to predict delamination failure in CFRTP structures
ARRK Engineering and Mitsui Chemicals improved delamination prediction accuracy to help optimize absorbed energy/failure load for an overmolded TAFNEX CF/PP UD tape bumper beam.
Read MoreJeep all-composite roof receivers achieve steel performance at low mass
Ultrashort carbon fiber/PPA replaces steel on rooftop brackets to hold Jeep soft tops, hardtops.
Read MoreActive core molding: A new way to make composite parts
Koridion expandable material is combined with induction-heated molds to make high-quality, complex-shaped parts in minutes with 40% less material and 90% less energy, unlocking new possibilities in design and production.
Read MoreThe basics of composite drawing interpretation
Knowing the fundamentals for reading drawings — including master ply tables, ply definition diagrams and more — lays a foundation for proper composite design evaluation.
Read MoreRead Next
ExOne acquisition accelerates expansion into 3D-printed tooling for composites
Patented 3D-printed sand tooling solution from Freshmade 3D applicable for composite layup, vacuum forming, compression molds, with 30-50% cost savings and design flexibility.
Read MoreAll-recycled, needle-punched nonwoven CFRP slashes carbon footprint of Formula 2 seat
Dallara and Tenowo collaborate to produce a race-ready Formula 2 seat using recycled carbon fiber, reducing CO2 emissions by 97.5% compared to virgin materials.
Read MoreDeveloping bonded composite repair for ships, offshore units
Bureau Veritas and industry partners issue guidelines and pave the way for certification via StrengthBond Offshore project.
Read More