ExOne acquisition accelerates expansion into 3D-printed tooling for composites
Patented 3D-printed sand tooling solution from Freshmade 3D applicable for composite layup, vacuum forming, compression molds, with 30-50% cost savings and design flexibility.
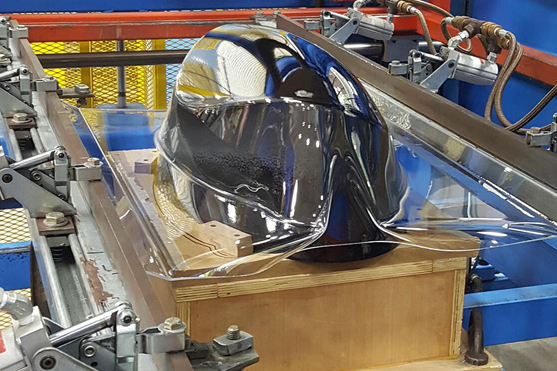
Photo Credit: ExOne
On April 28 ExOne Co. (North Huntington, Pa., U.S.), a binder jet 3D printing technology company announced it has acquired the assets of Freshmade 3D (Youngstown), an Ohio-based startup with a patented method of creating durable AMClad tooling out of sand forms 3D-printed on ExOne machines for a wide range of composite tooling applications. The strategic move will strengthen ExOne’s position as a provider of large-format 3D-printed (also known as LFAM) tooling for industrial applications.
AMClad tooling, which is 3D printed in low-cost sand on ExOne systems and then infiltrated and coated using Freshmade 3D’s patented method, is said to eliminate weeks or months of time spent waiting for conventional tooling. What’s more, Freshmade 3D says, it typically offers a 30-50% cost savings.
“We launched AMClad with the idea of using sand 3D printing technology to deliver hard tooling faster and with more design freedom.”
According to Freshmade 3D, the fast, durable and affordable solution can be used for a wide range of tooling applications, including composite layup, vacuum forming, compression molds, urethane casting molds, trim fixtures, hydroforming, sheet metal stamping and more. AMClad tooling is being used today by customers in the aerospace, art, architecture, automotive, construction and energy industries.
ExOne says it has been developing tooling products for its large, industrial 3D printers since 2014, and currently offers sacrificial tooling for composite layup that washes out with water. However, ExOne believes Freshmade 3D’s patented approach offers additional unique benefits and can help accelerate adoption of 3D-printed sand tooling solutions.
“We are delighted to add Freshmade 3D’s patented process for creating durable 3D-printed tooling to our portfolio,” says John Hartner, ExOne CEO. “We plan to scale up this process for a global aerospace customer, who intends to use this tooling for composite layup of parts. This is an ideal solution for companies looking to shorten supply chains and produce tooling and final products locally.”
In addition to tooling, the AMClad process is being used to produce artwork or restoration pieces, including replication statues for museum exhibits, exterior reproductions for architectural refurbishment, or custom chrome details on classic cars. The versatile surface finishes available with the AMClad process include metal, stone or painted finishes that allow for a range of artistic applications to be realized in a cost-effective manner. An AMClad replica of the Statue of Liberty’s Italian sister — the Liberty of Poetry — was featured at Ellis Island and now resides at Kent State University.
“We launched AMClad with the idea of using sand 3D printing technology to deliver hard tooling faster and with more design freedom, to enable U.S. manufacturers to produce more locally and faster,” says Rich Wetzel, Freshmade 3D co-founder, who will now join ExOne’s applications team. “ExOne is the best company to accelerate this technology as we scale up for customers who’ve decided to leverage our solution to meet production goals faster. Companies are just beginning to discover how robust and affordable this technology is over conventional tooling.”
Freshmade 3D was founded by Wetzel, Christoper Tomko and Dr. Brett Conner in 2016 and is a portfolio company of the Youngstown Business Incubator, which supports the development of innovative high-tech companies in the Northeast Ohio region. Freshmade 3D has also received development support from America Makes, part of the National Network for Manufacturing Innovation established by the Revitalize American Manufacturing and Innovation Act of 2014.
“We’re proud to be a part of Freshmade 3D’s success,” says Barb Ewing, CEO of the Youngstown Business Incubator. “Two of the three founders started their entrepreneurial career as part of our team. They are proof that northeast Ohio is fast becoming the epicenter for additive manufacturing in North America.”
Related Content
Addyx carbon exoskeleton technology enables molded ribs inside hollow composite structures
Using a water-soluble mandrel, carbon exoskeleton opens paradigm for topology-optimized composites, cutting weight, manufacturing time and scrap rate.
Read MoreCorebon induction heating
This sidebar to CW’s August 2024 feature article reviews this technology for more efficient composites manufacturing and why it aligns with Koridion active core molding.
Read MoreNine factors to consider when designing composites cure tooling
Gary Bond discusses the common pitfalls and compromises when designing good cure tooling and their holistic significance for a robust composite production process.
Read MoreProper application of semi-permanent mold release systems
Performing regular maintenance of the layup tool for successful sealing and release is required to reduce the risk of part adherence.
Read MoreRead Next
Developing bonded composite repair for ships, offshore units
Bureau Veritas and industry partners issue guidelines and pave the way for certification via StrengthBond Offshore project.
Read MoreAll-recycled, needle-punched nonwoven CFRP slashes carbon footprint of Formula 2 seat
Dallara and Tenowo collaborate to produce a race-ready Formula 2 seat using recycled carbon fiber, reducing CO2 emissions by 97.5% compared to virgin materials.
Read MoreVIDEO: High-volume processing for fiberglass components
Cannon Ergos, a company specializing in high-ton presses and equipment for composites fabrication and plastics processing, displayed automotive and industrial components at CAMX 2024.
Read More