Automated Preforming, Part 7: Fill Gesellschaft
Fill automates preforming for 1-min cycle time overmolded thermoplastic automotive parts but supplies automation throughout aero- and autocomposites process chains.
This is final installment of a seven-part series about preforming. For more on this series, click the links below:
part one, part two, part three, part four, part six, part six.
Also, don’t miss the printed version of this series:
Preforming Goes Industrial, Part 1 and Part 2.
Fill focuses on automated equipment for manufacturing lightweight constructions in wood, aluminum and composites. The company is well known in Europe and has been trying to help the U.S. composites industry better understand its capabilities through presentations at Composites World’s (CW) 2016 Carbon Fiber conference and CAMX 2017.
I first saw Fill equipment when I toured FACC. Established in 1966, Fill is family-owned and based in Gurten, Austria, just 15 minutes from FACC and SGL Composites (previously BENTELER-SGL and a Fill customer). It has 800 employees, additional facilities in Shanghai, China and Puebla, Mexico and sales of 160 million euros in 2017.
![]() |
![]() |
SOURCE: Fill Gesellschaft
Automation Case Histories
Fill’s first machines were developed to automate production of skis for Fischer. Today it takes 25 percent of the workers to produce 80 percent of the original annual production volume. Note also that skis are a hybrid design, comprising layers of glass and/or carbon fiber composite, wood cores, steel edges and multiple types of plastic.
![]() |
![]() ![]() |
Fill has supplied multiple generations of automated equipment for producing composite skis. SOURCE: Fill Gesellschaft 2017 CAMX presentation.
BMW
As BMW developed the i3, i8 and new 7 Series models—all of which use carbon fiber reinforced plastic (CFRP) composites—Fill supplied a range of automation solutions.
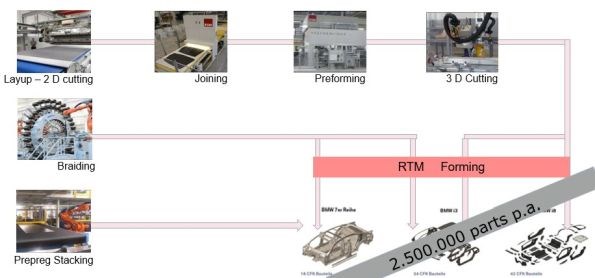
SOURCE: Fill Gesellschaft 2017 CAMX presentation
Composite Monocoques
Fill also developed a unique production line for Mubea CarboTech capable of producing CFRP monocoques for two different car models: the Volkswagen VW XL1 and the Porsche 918 Spyder. This automated line included multi-piece actuated molding tools, high-press resin transfer molding (HP-RTM) press, post-curing and machining capabilities.

Fill supplied a composite monocoque production line for Mubea CarboTech.
SOURCE: Fill Gesellschaft 2017 CAMX presentation
Automating Layup
For automated layup, Fill has developed systems for a range of different materials, including dry fabric up to 3 m in width (for higher-volume production at BMW). The SpeedLayer 800 automatic spar cap laying system for wind turbine blades applies unidirectional carbon fiber prepreg up to 800 mm in width at a reported rate of 1.5 m/s and accuracy of ±1.5 mm. It can handle 600-kg prepreg rolls and integrates process validation and quality assurance functions.
Fill has developed a range of automated layup systems (left) including SpeedLayer 800 for wind blade spar caps using UD carbon prepreg up to 800 mm in width (right).
SOURCE: Fill Gesellschaft 2017 CAMX presentation
The Low-Cost Flexible Integrated Composite Process (LOWFLIP) project was a 3-year (Oct 2013-Oct 2016) EU-funded initiative that included Fill and nine other partners, aimed at automating prepreg layup for out of autoclave (OOA) cured transportation structures. It comprised three demonstrators:
- 2.5 × 2.9 m front wall for a truck trailer
- 1.2 m long automotive cross beam
- 1.0 × 1.2 m stiffened skin aircraft tailcone panel
Fill worked with nine partners in LOWFLIP to develop an automated layup cell for production of large composite transportation structures without an autoclave. SOURCE: Fill Gesellschaft 2017 CAMX presentation
“We used electrical resistance heating to heat the mold up to 120°C,” recalls Wilhelm Rupertsberger, head of Fill’s Competence Center for Composites and Plastics. “The material was always under tension during automated layup,” he adds, “and we achieved wrinkle-less draping directly to the mold. We built a human process, but one using robots to improve repeatability.”
You can see the truck trailer wall at left, as well as the car cross-beam and aircraft tail cone panel demonstrators in the LOWFLIP team photo above.
SOURCE: Fill Gesellschaft 2017 CAMX presentation
Multi-Layup to Multilayer System
Fill’s Multi-Layup System was developed for production of automotive body-in-white (BIW) parts like rear walls and lower bumper stiffeners using thermoplastic tapes. It was envisioned that these parts would include overmolded ribs and other features, thus the layup cycle for the preform would need to match the subsequent injection molding cycle.
My JEC 2017 post-show blog post included a video of the Multi-Layup System, which fed tapes from multiple rolls, placing all of the tapes needed per layer simultaneously, instead of serially, one-at-a-time. In this way, it achieved a cycle time of 10-15 seconds per layer.
Fill has now further modified the system and renamed it the Multilayer. It feeds, cuts and places up to 16 tapes in widths up to 50 mm (each 0.01-0.04 mm thick) onto a rotating table. The tape laying bed can produce parts up to 1.6 × 1.6 m. Tapes are applied at a speed of ≈500 m2/hr—every 12-15 seconds a full-sized part layer is applied for roughly a 1-minute cycle time per finished preform. Layers are not fully consolidated but joined via thermal bonding. As each spool runs out of tape, it is automatically changed without stopping the machine.
Fill’s Multilayer automated preforming system enables a significant reduction in trimming waste while placing tapes only where needed and orienting them as necessary to achieve tailored laminates.
SOURCE: Fill Gesellschaft 2017 CAMX presentation
Finished preforms are then consolidated in a press. “We have integrated Multilayer with an automated consolidation press and Engel injection molding cell which function together to deliver a 1-minute cycle time,” says Rupertsberger. Fill received an order for the first Multilayer system from Swinburne University of Technology (Melbourne, Australia) earlier this year and will demonstrate the equipment live for the first time at JEC World 2019 (Mar 12-14, Paris, France).
RTM Presses and Adaptive Injection
Fill has supplied multiple RTM presses, including HP-RTM presses to SGL Composites.
![]() |
![]() |
Fill has supplied a wide variety of presses for composites production, including HP-RTM presses to SGL Composites (right). SOURCE: Fill Gesellschaft
With Airbus Operations (Stade, Germany) and the Institute of Plastics Processing (IKV) at RWTH Aachen University, Fill has developed an innovative adaptive injection unit for RTM initially for aerocomposite structures. Before parts made with RTM can fly on an aircraft, they must pass a time-consuming and costly quality assurance (QA) process. To shorten this process, RTM forming tools have been equipped with sensors, enabling the QA to be deployed inline during production. IKV, Airbus and Fill have now integrated these sensors into the injection system, eliminating the need to equip every single forming tool. Using disposable cartridges in the same way piston injection systems are used in typical RTM systems, the adaptive injection unit is equipped with a sensor box enabling the following data to be measured and recorded in situ:
- Temperature
- Pressure
- Resin viscosity
- Cross-link density of the resin system
- Glass transition temperature (Tg).
While ensuring the quality of the molded parts, this data may also be used to manage and control the injection process. This Industry 4.0 adaptive injection system is being developed for aerocomposites, and also extended to other industries such as automotive.
Hot Drape Forming
In the recent tour articles Sara Black and I wrote about high-performance composites in Israel, we noted that most of the companies were using hot drape forming. In fact, at Elbit Cyclone, our tour guide Jonathan Hulaty stated, “I don’t know how you do this type of high-rate prepreg parts production without hot drape forming,” referring to beams and stanchions for Boeing 787 assemblies. Hot drape formers (HDF) are also seen as indispensable by FBM and Israel Aerospace Industries. Fill has supplied HDF systems for years, including several units in production at FACC. They are basically vacuum-forming systems, equipped with infrared or other types of heating elements and a reusable silicone rubber membrane to heat and compress—debulk—prepreg layups on their tools prior to cure. HDF becomes a key part in the complete aerocomposites production line shown below.
Hot drape forming has become an important enabler for high-volume production of prepreg composite aerostructures and is automated by Fill as part of its full process chain solutions. SOURCE: Fill Gesellschaft
Industry 4.0 Production Cells for CFRP
At the end of 2013, Fill began developing a production system for manufacturing CFRP stringers, used for stiffening Airbus A320 landing flap shells, in collaboration with the Tier supplier. Upon installation, this system successfully reduced the number of stations, improving production flow, and also improved user-friendliness. It comprises:
- Automatic forming tool storage
- HDF station
- Press-turn-lifting station where laminates are processed into stringers.
(click on images to enlarge)
|
Fill has developed three generations of automated production cells (right) for landing gear flap stringers made from prepreg (left).
SOURCE: Fill Gesellschaft
A second-generation system to produce the same type of parts was commissioned in 2017. Where the first system focused on optimizing individual stations, this later system aimed to minimize manual tasks and integrate all of the tool logistics. Three key areas of development enable this second-generation system to achieve high reproducibility and significantly increased productivity:
- Manual retrieval and storage of forming tools are replaced with a fully automatic tool return, shortening the logistics process times. This has also reduced the space requirement by more than 50 percent.
- Further automation of subprocesses has reduced unproductive time.
- Industry 4.0 digitalization of all recording and reporting. Software developed by Fill enables visualization of the process at all times and recording of each component’s history all along the process chain. Sensors detect the availability of tools and materials to avoid bottlenecks and improve reordering.
Press-turn-lifting station used in automated production cells for A320 and A350 landing gear flap stringers.
SOURCE: Fill Gesellschaft
Fill is now working on a third-generation production system for landing flap shells intended for the Airbus A350-900. It too comprises tool storage, membrane-forming (HDF) station, press-turn-lifting station and automatic tool return but has been enhanced with a transport system for autoclave tools, replacing previous manual transport trucks and electric tractors with automated guided vehicles (AGVs). Fill is already working on future systems, looking at how to further improve man and machine collaboration.
Accubot
Even before the composites industry began to verbalize their envisioned future need for a multi-operation work cell, Fill was already developing the first prototypes, what it calls Accubot. The idea was to develop an accurate robot using a laser tracker for spatial compensation as well as direct external measurement systems. This robot would be able to switch out functions with end effectors, becoming not only a nondestructive testing (NDT) cell but also a machining cell. Accubot applications include:
- Drilling
- Riveting
- NDT – Ultrasound with a squirter
- NDT – X-ray
- NDT – Computed tomography
![]() |
![]() click to enlarge
|
Accubot for drilling (left) and NDT using high-speed ultrasonic scan (right).
SOURCE: Fill Gesellschaft.
FlexHyJoin
Fill is a member of the EU-funded project Flexible Production Cell for Hybrid Joining (FlexHyJoin). This 3-year program is aimed at developing a fully automated pilot process for joining metallic brackets/fittings with thermoplastic composites in automotive applications by combining laser joining and induction joining technologies. Fill designed and built the automated cell including software and integration of the various technologies.
Fill’s research and development continues. It understands that innovative and intelligent production systems are required to make manufacturing of composite parts more economical and amenable to higher volumes. And it is committed to developing these systems according to the scale and specific needs of its customers.

SOURCE: FlexHyJoin.
Related Content
Thermoplastic composites: Cracking the horizontal body panel nut
Versatile sandwich panel technology solves decades-long exterior automotive challenge.
Read MoreMcLaren celebrates 10 years of the McLaren P1 hybrid hypercar
Lightweight carbon fiber construction, Formula 1-inspired aerodynamics and high-performance hybrid powertrain technologies hallmark this hybrid vehicle, serve as a springboard for new race cars.
Read MoreASCEND program update: Designing next-gen, high-rate auto and aerospace composites
GKN Aerospace, McLaren Automotive and U.K.-based partners share goals and progress aiming at high-rate, Industry 4.0-enabled, sustainable materials and processes.
Read MoreJeep all-composite roof receivers achieve steel performance at low mass
Ultrashort carbon fiber/PPA replaces steel on rooftop brackets to hold Jeep soft tops, hardtops.
Read MoreRead Next
Automated Preforming, Part 1: Numbers and Landscape
CW’s multi-blog series on preforming begins with an overview and quick look at the numbers: 1-minute take time, 10-15 seconds per layer, 490-kg/hr and 3.5 million parts/year. Are you ready for serial CFRP production?
Read MoreAutomated Preforming, Part 6: Coriolis Composites
Pioneer in automated fiber placement (AFP) advances preforms for overmolded thermoplastic composites enabling production of one automotive part every 20 seconds.
Read More“Structured air” TPS safeguards composite structures
Powered by an 85% air/15% pure polyimide aerogel, Blueshift’s novel material system protects structures during transient thermal events from -200°C to beyond 2400°C for rockets, battery boxes and more.
Read More