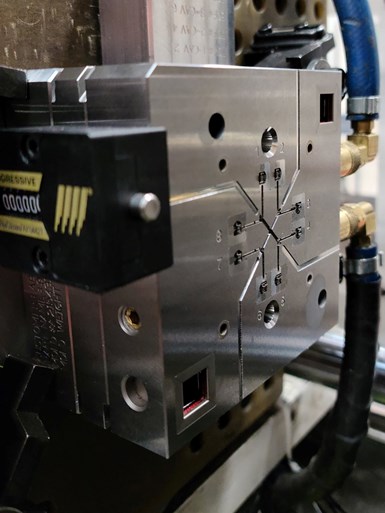
The back half of a micro connector mold that highlights Matrix Tool's engineering-driven, high-precision moldmaking. Photo Credit, all images: Matrix Tool Inc.
Who is Matrix Tool Inc.?
Tom Moyak, Business & Engineering Development: Matrix Tool Inc., founded in 1972, is an engineering-driven manufacturer of custom plastic injection-molded products and high-precision tooling. We are experts in producing high-precision micro- and standard-sized complex parts. These include electrical connectors, computer connectors, automotive under-the-hood components or any other tight tolerance molded part requiring a wide range of engineering-grade thermoplastic resins.
Located in Fairview, Pennsylvania, our 60,000-square-foot facility has a fully staffed and equipped mold design and tooling department, along with a 24-hour mold maintenance, repair and changeover department. We produce tools ranging from single-cavity, production-intent prototypes to multi-cavity, high-volume production molds.
Our tool shop is truly a full-service, in-house tool-building resource. We maintain a complete array of mold-building equipment, including 15 CNC wire and die sinker EDM machines, along with seven high-precision CNC milling machines. We are one of few in the country with the capabilities afforded by our latest AgieCharmilles Cut 2000S wire EDM with precision as fine as 0.000040 inch and finishes as fine as 0.1 Ra using wire as small as 0.002 inch, while our Sodick UH650L high-speed mill is capable of 0.000050-inch precision and excellent surface finishes as well.
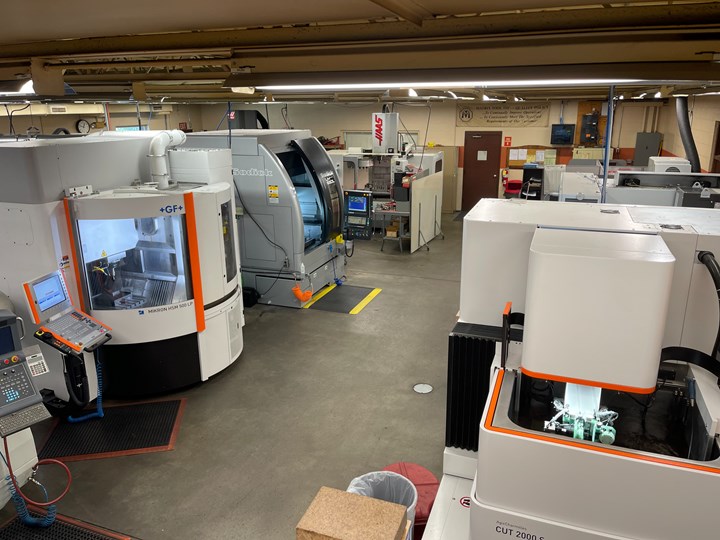
The Matrix Tool tool shop is a full-service, in-house mold-building resource with a fully staffed and equipped mold design and tooling department, along with a 24-hour mold maintenance, sampling and changeover department. The team produces tools ranging from single-cavity, production-intent prototypes to multi-cavity, high-volume production molds.
Matrix has 40 injection molding machines located in two separate molding rooms. Thirty Nissei presses in our Advanced Precision Molding room and 10 Sodick presses in our Advanced Micro Molding room. Press sizes range from 55–240 tons of clamping force in our Advanced Precision Molding room, while the 10 molding machines in the Advance Micro Molding room range from 20-60 tons of clamping force.
Currently, Matrix Tool has 132 employees. More than 25% of our staff consists of either degreed plastics engineers or journeymen toolmakers.
What do you view as your chief competitive advantage(s)?
Moyak: Matrix Tool’s nearly 50-year history of providing extremely high-precision tooling and molding services positions us well in the field of precision molding and tooling. Through significant R&D investment in training, equipment and process development, we achieve industry-leading results in precision and throughput. In addition, having very deep and broad technical experience in the design, tooling and molding departments is a significant asset and what we feel is our core differentiator.
Provide an example of the most significant and recent change in your use of technology.
Moyak: Fortunately for Matrix Tool, we were engaged in a capital equipment investment program just as the pandemic began. We brought on several new state-of-the-art machining centers for wire EDM, CNC EDM and CNC milling and a new hole popper. We also purchased three new Sodick micro injection molding machines, six Yushin full-servo robotic systems and related auxiliary equipment. These have positioned us well to meet the surge in demand that’s impacting our industry overall.
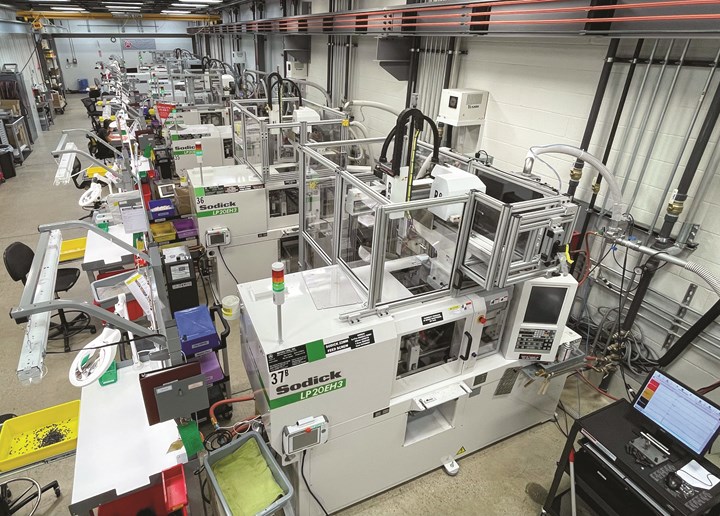
Matrix has 40 injection molding machines located in two separate molding rooms with press sizes range from 55–240 tons of clamping force in the Advanced Precision Molding room and from 20-60 tons of clamping force in the Advance Micro Molding room.
How have you changed your general approach to business?
Moyak: Matrix continues to question the generally accepted standards and norms in both tool design and the injection molding process. This real-time blueprint was created out of necessity. Our customer base continually requests product features and overall sizing that isn’t ideal or efficient to produce in traditional tooling and molding machines. This prompted us to step back and start asking lots of questions. For example, why do we consistently get asked to place smaller parts in larger mold bases with hot runner systems that inherently add a degree of unwanted variation and expense?
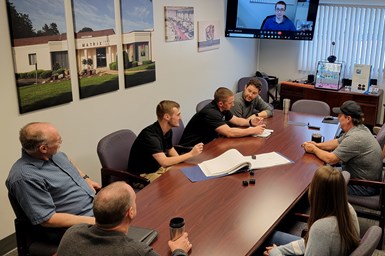
Deep, broad technical experience in design, tooling and molding has been Matrix Tool’s core differentiator.
Once we started asking these hard questions, we went to work developing creative solutions for cavity spacing, tool sizing, runner layout, melt delivery, etc. Matrix’s counterintuitive approach was met with skepticism—even from our existing customer base. Long accepted paradigms are hard to change, but our persistence to challenge the norm continues to pay dividends for our customers. Once they saw the proven results of this unique approach, they realized the benefit of running in a smaller press size at lower cavitation but higher yield.
Fast forward to today, and we continue to push the limits and accepted norms in our industry. We call this approach “The Matrix Way.” Our new business quotations reflect the benefits of designing a “smaller, faster, better” solution for our customers.
What are the most significant ways you expect your business to evolve in the next three to five years?
Moyak: With the ever-growing demand to miniaturize product platforms or product features in nearly every industry, our focus on serving our customers’ high-precision molding and tooling needs will be a key strategy over the next three to five years.
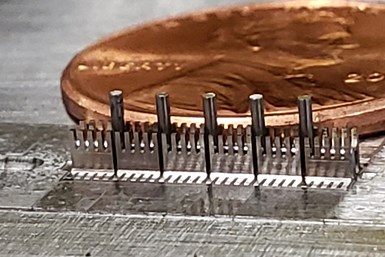
The Matrix Tool team are experts in producing high-precision micro- and standard-sized complex parts, including electrical connectors, computer connectors and automotive under-the-hood components.
Matrix Tool recognizes that to be near or at the leading edge in any industry takes a continual commitment to improve. Most of our OEM customers view Matrix Tool as their technology leader in molding and tooling. Incremental gains through investments in precision, automation and technical employee training will keep Matrix Tool as an industry leader.
Tell us how you are addressing the skills gap in the industry.
Tim Lewis, President: Finding qualified employees for both press operators and higher skilled toolmaker positions has been a challenge—during the pandemic in particular. In terms of skilled tooling positions, Matrix recruits mechanically inclined candidates for enrollment in its Pennsylvania State-Approved Apprentice Program.
Apprentice toolmaker candidates get diverse coursework and hands-on exposure to all aspects of precision moldmaking during their first four years in the trade. In addition, formal in-house training is coordinated as needed for tooling personnel on a variety of technical topics, including new machining technologies, CAD software and CAM software on an as-needed basis.
Matrix has addressed the retention of existing employees by strengthening the overall compensation program offered to our essential workers and offering various incentives to production team members for supporting extended work schedules to meet existing customer demand.
In addition, we’ve implemented other creative ways to show our appreciation for employees, including expanded training opportunities for all team members, enhanced communication and the use of formal/informal motivation programs to recognize employee efforts.
Longer term, Matrix will continue developing and supporting its active internship initiative with the Penn State Behrend Plastics Technology program. This has been a critical resource for developing and retaining talented new employees. We also just kicked off a celebration for our 50th year in business, which will focus on recognizing our greatest asset—our people—throughout the following year.
Matrix continues to question the generally accepted standards and norms in both tool design and the injection molding process.
Describe the most interesting/notable mold project your company was awarded.
Moyak: One of our recent successes involved convincing a Fortune Top 10 company to let us tackle a very high-profile program of theirs using what we call “The Matrix Way.” Our customer initially requested that we quote a 16-cavity mold with a hot runner system and other technology for a micro-featured, delicate product. However, we suggested alternative materials because the material they selected wasn’t optimal and what they requested had a very high probability of failure.
But more importantly, we were only willing to quote our “outside of the box” solution. It took some convincing, but our unique eight-cavity all cold-runner solution provided more throughput with less waste than the Fortune Top 10 company had estimated for their 16-cavity hot runner solution.
The tool we designed and built was simpler and required a much lower capital investment. In addition, it had the bonus of significantly reduced cycle time and smaller runner sizing while greatly improving part quality and consistency. It was a win-win for all and a real eye-opener for our customer.
Related Content
Carbon fiber, bionic design achieve peak performance in race-ready production vehicle
Porsche worked with Action Composites to design and manufacture an innovative carbon fiber safety cage option to lightweight one of its series race vehicles, built in a one-shot compression molding process.
Read MoreJeep all-composite roof receivers achieve steel performance at low mass
Ultrashort carbon fiber/PPA replaces steel on rooftop brackets to hold Jeep soft tops, hardtops.
Read MoreNovel dry tape for liquid molded composites
MTorres seeks to enable next-gen aircraft and open new markets for composites with low-cost, high-permeability tapes and versatile, high-speed production lines.
Read More“Structured air” TPS safeguards composite structures
Powered by an 85% air/15% pure polyimide aerogel, Blueshift’s novel material system protects structures during transient thermal events from -200°C to beyond 2400°C for rockets, battery boxes and more.
Read MoreRead Next
Thermoset Mold Builder Takes on EV Market
New Dynamics and NDC International provide complete tooling and molding solutions for the electric vehicle market and electronic encapsulation technology.
Read MoreNew Ownership Revitalizes Precision Mold Builder with Heavy Capital Investments, New Management Style
A rich history in mold building, recent technology investment and a shift in management philosophy re-energizes a Midwest precision mold builder and contract CNC machine shop.
Read MoreGrowing AM's Presence in Moldmaking
Advanced Michigan mold manufacturer advocates for additive manufacturing in moldmaking through collaboration and education.
Read More